Expert Techniques for Cutting Plastic Baseboards
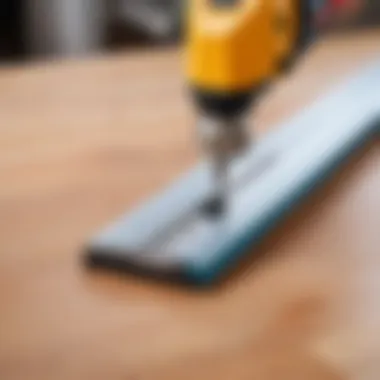
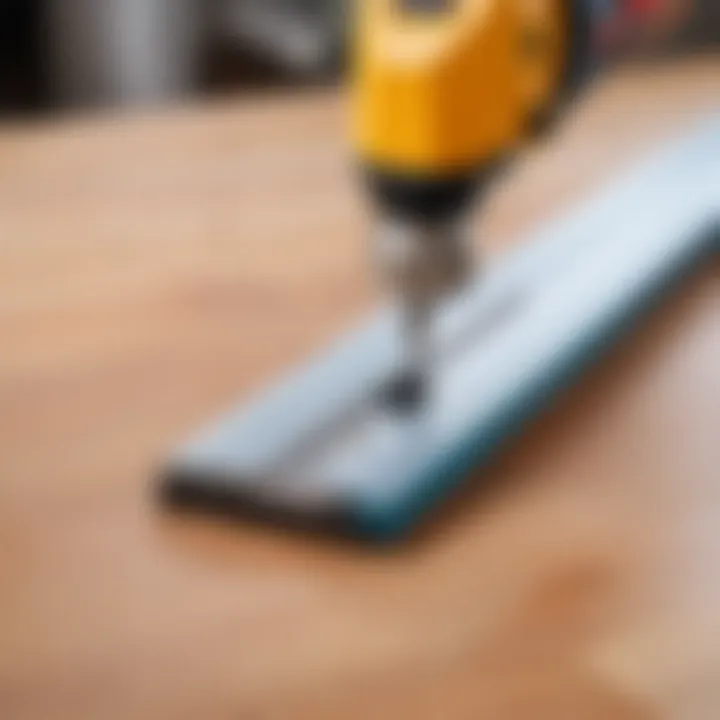
Intro
Cutting plastic baseboards is more than a technical task; it is an essential skill for anyone involved in home improvement of upgrading interior spaces. Plastic baseboards come in various styles and materials that can add a touch of elegance or functionality to a room. When executed correctly, cutting these baseboards can transform the overall aesthetics of a space. However, the process requires careful planning and the right techniques. This article aims to guide readers through the intricate details of effectively cutting plastic baseboards, ensuring that both novices and experienced professionals can achieve the best results.
Проектирование и планирование
Planning is a crucial step before any home improvement project. Understanding the specifics of the project allows for a smoother process and minimizes the chances of errors.
Как выбрать проект для DIY
Choosing the right DIY project often begins with assessing individual capabilities and resources. Consider what style of baseboard best matches the room's design. Some types of plastic baseboards are easier to work with than others. Models with flexible materials can be beneficial if your walls are not perfectly straight, as they can accommodate slight imperfections. Selecting a design that suits your skill level is essential to avoiding frustration.
Оценка времени и ресурсов
It is vital to calculate how much time is available for the project. Smaller rooms may require less time to cut and install baseboards compared to more extensive spaces. Gather necessary tools and materials beforehand to ensure everything is on hand. Common tools include a miter saw for angled cuts and a utility knife for straight cuts. Having protective gear such as goggles and gloves is also important for safety.
Выбор материалов
Picking the correct materials is another crucial aspect in achieving desired results when cutting plastic baseboards. There are numerous types of plastics available, each with different characteristics that may affect the cutting process.
Типы материалов для различных проектов
Plastic baseboards can be found in various grades. Higher-grade plastic is typically more durable and resistant to damage, while lower-grade types might be lighter but are potentially less durable. PVC and polyurethane are common materials. PVC is often favored for its ease of use and affordability. Polyurethane, on the other hand, tends to offer a more premium look and feel.
Советы по покупке и экономии
When selecting materials, it is wise to compare prices from different suppliers to ensure you are getting the best deal. Bulk purchases may also yield discounts. Local building supply stores or online retailers can be valuable resources for shopping. Always read reviews and product descriptions to ensure compatibility with your project needs.
When it comes to cutting plastic baseboards, preparation and the right choice of materials are paramount for achieving a professional finish.
Understanding Plastic Baseboards
Plastic baseboards have become an increasingly popular choice among builders and interior designers. They offer numerous benefits that enhance both aesthetic appeal and functional longevity in various environments. Understanding the composition, types, and advantages of plastic baseboards is essential when considering them for home improvement projects. Knowledge about these aspects not only aids in making more informed decisions but also enables individuals to achieve superior results when it comes to installation and maintenance.
Composition and Types of Plastic
Different types of plastic are commonly used for baseboards. Each has its unique characteristics affecting performance, durability, and ease of cutting.
Polyvinyl Chloride (PVC)
Polyvinyl Chloride is one of the most widely used plastics for baseboards. It offers a combination of strength and resilience that makes it a popular choice for many projects. The key characteristic of PVC is its flexibility, allowing it to conform to various shapes and contours. This property is a beneficial aspect as it eases installation in areas with irregular surfaces. However, one unique feature worth noting is its tendency to expand and contract with temperature changes, which may require careful consideration during installation.
Polypropylene (PP)
Polypropylene is another type of plastic utilized in baseboards. Its main attraction lies in its lightweight nature and moderate strength, which facilitates easy handling and cutting. The key characteristic of Polypropylene is its resistance to many chemicals, making it suitable for use in environments prone to spills or stains. A significant advantage of PP is its ability to retain color and texture even after prolonged exposure to sunlight. Nevertheless, it may not provide the same level of durability as PVC.
High-Density Polyethylene (HDPE)
High-Density Polyethylene is known for its toughness and high impact resistance, making it an excellent choice for areas with potential physical stress, such as children’s rooms or active living spaces. The key characteristic of HDPE is its scratch resistance, which helps maintain a clean appearance over time. Its unique feature is that it can usually withstand wider temperature ranges without warping compared to other plastics. However, its rigidity can make it slightly more challenging to cut and install compared to more flexible options like PVC.
Advantages of Using Plastic Baseboards
The advantages of plastic baseboards contribute significantly to their growing popularity in renovation and construction projects.
Durability
Durability is a primary advantage of plastic baseboards. These materials are designed to withstand the rigors of daily life without losing their visual appeal or structural integrity. This quality makes plastic an ideal choice for high-traffic areas.
Moisture Resistance
Moisture resistance is crucial in areas like bathrooms and kitchens. Plastic baseboards do not absorb water, thus preventing potential mold and mildew development. This feature allows homeowners to maintain a healthier living environment.
Low Maintenance
Low maintenance is another appealing attribute of plastic baseboards. They require minimal cleaning and periodic inspections to keep them looking fresh. Unlike wood, they do not need painting or sealing, which saves time and reduces ongoing costs.
Preparation for Cutting
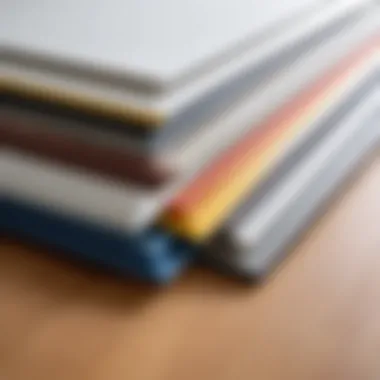
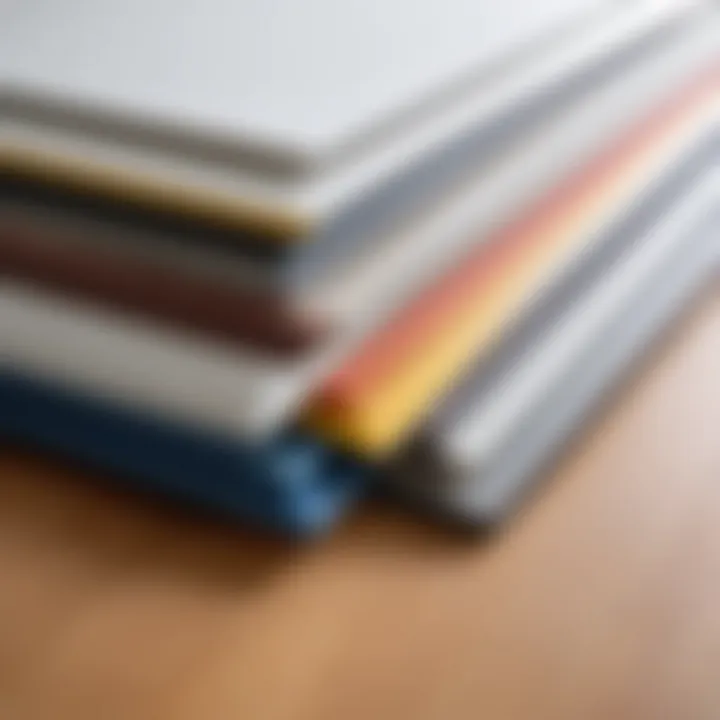
Preparing for cutting plastic baseboards is a critical step that can significantly influence the quality of the final result. Proper preparation ensures that the cuts made are accurate and clean. It also minimises the risk of errors that could lead to wastage of materials or the need for repairs. Moreover, good preparation contributes to safety during the cutting process. Having the right tools and a strategic approach to measuring can enhance the efficiency and effectiveness of the project.
Necessary Tools and Equipment
Measuring Tape
The measuring tape is an essential tool in the preparation phase. Its primary function is to provide precise measurements of both the baseboards and the area they will cover. A significant characteristic of a measuring tape is its flexibility, allowing it to conform to surfaces and reach places that may be difficult to measure with rigid tools.
A popular choice is the Stanley FatMax measuring tape due to its durability and easy-to-read markings. The blade has a magnetic tip which is beneficial when measuring metal surfaces, and the wide blade reduces the chance of bending and provides more accurate measurements.
However, the disadvantage might be its bulkiness, which can make it slightly harder to carry in tight spaces.
Safety Goggles
Safety goggles play a vital role in ensuring safety when cutting plastic baseboards. Their main purpose is to protect the eyes from flying debris that can occur during the cutting process. A key characteristic of safety goggles is their snug fit, which prevents any particles from entering the eye area.
Choosing goggles that meet safety standards, like the 3M Virtua Clear Safety Glasses, can provide comfort while ensuring protection. They come with an anti-fog coating, which enhances visibility. However, a possible downside is the discomfort that might come from extended wear, particularly in warmer conditions.
Cutting Tools
Cutting tools are pivotal in achieving clean and accurate cuts when working with plastic baseboards. Options like a miter saw, utility knife, and power saw all have unique strengths. A primary characteristic of these tools is their ability to make precise cuts, which is essential for a professional finish.
For example, the DeWalt DWS779 miter saw stands out for its powerful motor and accurate cutting angles, making it a favorable choice. Such tools can significantly reduce cutting time, allowing for more efficient project completion. However, the downside is that they can be more costly and require a certain level of experience to use correctly.
Measuring and Marking
Measuring Lengths
Measuring lengths accurately is one of the most critical aspects of preparing for cutting. It ensures that each piece fits properly in the designated space. The measuring process involves checking the lengths multiple times before cutting to avoid mistakes. A measure that offers both metric and imperial units can simplify this task, catering to different preferences.
An advantage of thorough measurement is that it provides confidence moving forward, as the chances of cutting errors drastically decrease. However, if measurements are rushed, it can lead to inaccurate cuts, resulting in excess material waste or poor fitting.
Making Accurate Marks
Making accurate marks is fundamental for achieving precision in cuts. Using a fine-tipped marker allows for clear visibility of measurements. This step requires attention to detail because even slight discrepancies can lead to significant issues during installation.
Choosing a marker that dries quickly, such as a Sharpie, can reduce the likelihood of smudging while working. The negative aspect is that not all markers work on plastics, hence ensuring compatibility with the material is essential prior to usage.
Using a Square Tool
The square tool is instrumental in ensuring that cuts are perfectly straight. This tool helps create a right angle for measuring marks and aligns them accurately. One notable aspect of a square tool is its robustness, which maintains its shape over time, contributing to consistent results.
Tools like the Empire 1210 Speed Square are favored for their ease of use and versatility. They can assist in both measuring and marking, thus streamlining the preparation process. However, the potential downside is that if not used properly, they can introduce inaccuracies if the user does not ensure that they are perfectly aligned.
Cutting Techniques
Cutting plastic baseboards requires specific techniques, as improper methods can lead to damage or unsatisfactory results. This topic is crucial for ensuring that the cutting process is both efficient and effective. Choosing the right cutting technique can determine the overall quality of the installation, helping both DIY enthusiasts and professionals to achieve desirable finishes.
Various methods exist, and each has its unique set of features, advantages, and potential drawbacks. Understanding these will help in making informed decisions while executing home improvement projects.
Using a Miter Saw
Setup Process
The setup process for using a miter saw is an essential step that lays the foundations for precise cutting. Ensuring that the saw is properly aligned and secured helps maintain accuracy. A clean, flat surface lets the user operate with confidence. This method is a preferred choice as it allows quick adjustments and is effective for angled cuts, common in baseboard installations.
One notable feature of the setup process includes adjusting the saw to the desired cutting height. This contributes to consistent cuts across multiple pieces. However, not setting up correctly can lead to uneven cuts and wasted materials.
Cutting Angle Adjustments
Adjusting the cutting angle is fundamental to achieving clean joints, especially in corners. The miter saw’s adjustable settings enable users to select the correct angles needed for precise joints. The convenience of this feature makes it popular among professionals and amateurs alike.
A unique aspect of angle adjustments is the ability to create either 45-degree or 90-degree cuts, allowing flexibility in design. Despite its usefulness, improper adjustments can result in significant inaccuracies, making careful planning essential.
Technique for Clean Cuts
The technique used to ensure clean cuts involves a steady hand and a firm grip on the material. Initiating the cut without force is key as it minimizes chipping at the edges. This approach is beneficial, allowing for smoother, more polished cuts.
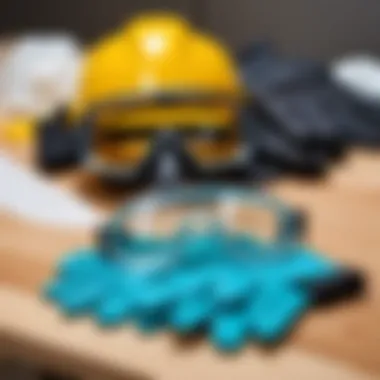
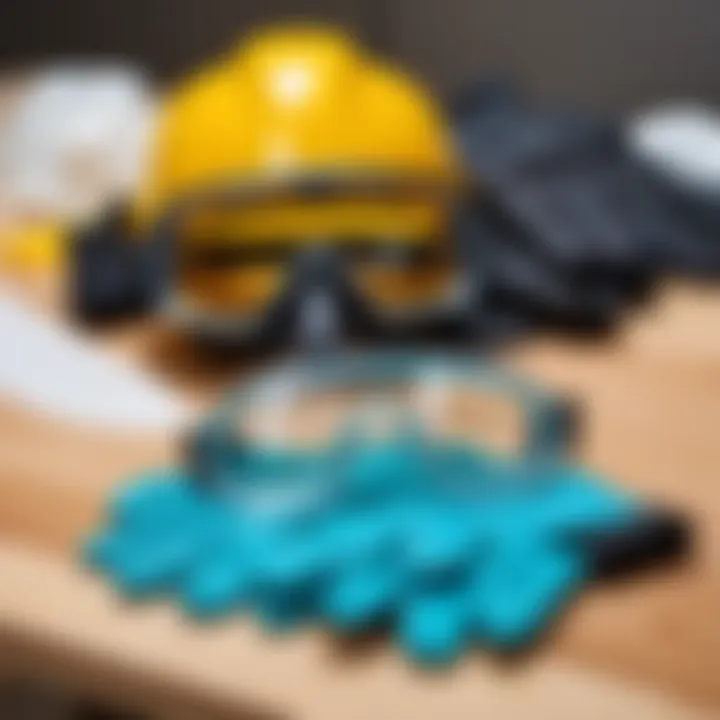
A notable characteristic of this technique is its reliance on the saw's speed settings. Higher speeds can lead to cleaner finishes but require managing the material's pressure. It’s a best practice to experiment with different settings to find the optimal balance for specific plastic types.
Using a Utility Knife
Selecting a Suitable Knife
Choosing the right utility knife is crucial for cutting plastic baseboards, particularly for thinner materials. A sharp, retractable blade can reduce exertion and increase safety. This selection poses advantages in cutting around more intricate shapes, which might not require heavy tools.
A unique feature here is the knife's ability to provide more controlled cuts for delicate or detailed work. However, using a dull knife can result in jagged edges and unnecessary effort, which is a significant disadvantage for this method.
Scoring Technique
The scoring technique involves making shallow cuts on the surface before fully separating the material. This is particularly effective and a preferred method for creating clean breaks in plastic baseboards. The initial score defines the clean line along which to break the piece, reducing the risk of chipping.
Highlighting its practicality, the scoring technique requires minimal tools, making it accessible for many users. Nonetheless, it requires steady hands to be effective; otherwise, users risk uneven cuts.
Finishing Edges
Finishing edges is an important concluding step in the cutting process. Smooth, neat edges enhance the overall look of plastic baseboards once installed. A fine file or sandpaper can be used effectively to achieve this. This method is beneficial as it helps in blending the cuts with existing materials, promoting an aesthetically pleasing installation.
The distinct feature of finishing edges lies in its role in preventing future damage. Rough edges can snag or deteriorate quickly over time. Yet, users may overlook this important step, leading to less-than-perfect installations.
Using a Power Saw
Preferred Types of Power Saws
Power saws, such as circular saws or jigsaws, are efficient for cutting thicker plastic baseboards. They provide more power and speed, which can be beneficial for larger projects. This characteristic makes them a favored choice among contractors who require quicker results.
Each type of power saw has its unique traits. For instance, a circular saw allows for straight cuts while a jigsaw provides more versatility with curves. However, one major drawback is the learning curve; they can be intimidating for less experienced users.
Utilizing Blade Settings
Utilizing different blade settings is crucial for effective cutting. Not all blades are created equal; therefore, selecting the right blade type that complements plastic is essential. This contributes significantly to how smoothly the cutting process goes.
The ability to adjust settings allows users to tackle various thicknesses, demonstrating adaptability. However, the wrong setting can lead to rushed cuts, resulting in damage or less professional finishes, which should always be avoided.
Safety Considerations
Safety considerations cannot be overlooked when using power saws. Proper protective gear, such as safety goggles and gloves, is important to prevent injuries. Understanding the common hazards associated with each saw type is critical to ensuring a safe cutting environment.
This aspect emphasizes training and preparation. It ensures users are aware of safety protocols, which can greatly reduce risks and lead to more effective work output. Negligence of safety can lead to accidents, making this a non-negotiable focus while cutting.
Post-Cutting Procedures
Post-cutting procedures may seem unimportant at first, but they play a crucial role in the overall success of your project. Properly smoothing edges, cleaning up the workspace, and conducting final inspections can ensure both safety and aesthetics. Focusing on these elements can lead to improved long-term durability and a polished look in your installations.
Smoothing Edges and Finishing Cuts
Sanding Techniques
Sanding after cutting plastic baseboards is essential for achieving a smooth and even finish. This process removes sharp edges and imperfections left from cutting. Sanding is effective because it allows for controlled abrasiveness, reducing the risk of damaging surrounding materials. A key characteristic of sanding techniques is the range of grits available, from coarse for initial smoothing to fine for a polished touch.
Advantages of sanding include its affordability and simplicity. However, the dust generated can be a drawback, requiring adequate ventilation and cleanup measures.
Using a Deburring Tool
A deburring tool is another option for smoothing edges after cutting plastic baseboards. Its primary function is to remove jagged edges, ensuring safety and enhancing the visual appeal. A notable aspect of using a deburring tool is its precision; it allows for meticulous work on the edges that might be overlooked with a sander.
This tool also offers the benefit of minimizing the amount of waste produced, as it typically removes only the necessary excess. However, one disadvantage can be the learning curve for proper use, as improper handling can lead to uneven edges.
Ensuring a Neat Finish
Ensuring a neat finish is vital for aesthetics and functionality. This process involves examining the edges post-cutting for any rough spots or inconsistencies. A neat finish reflects attention to detail and may prevent issues later on, such as peeling or lifting.
The meticulous nature of this task reinforces its significance as a best practice in home improvement projects. However, it may require time and careful consideration, which some may view as a disadvantage due to the potentially time-consuming effort needed to achieve perfection.
Cleaning Up the Workspace
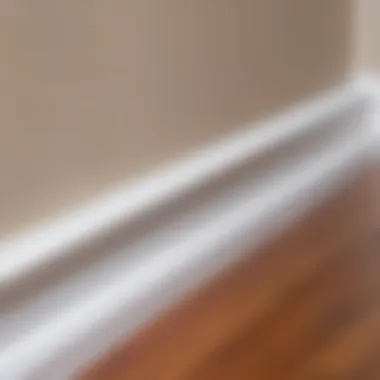
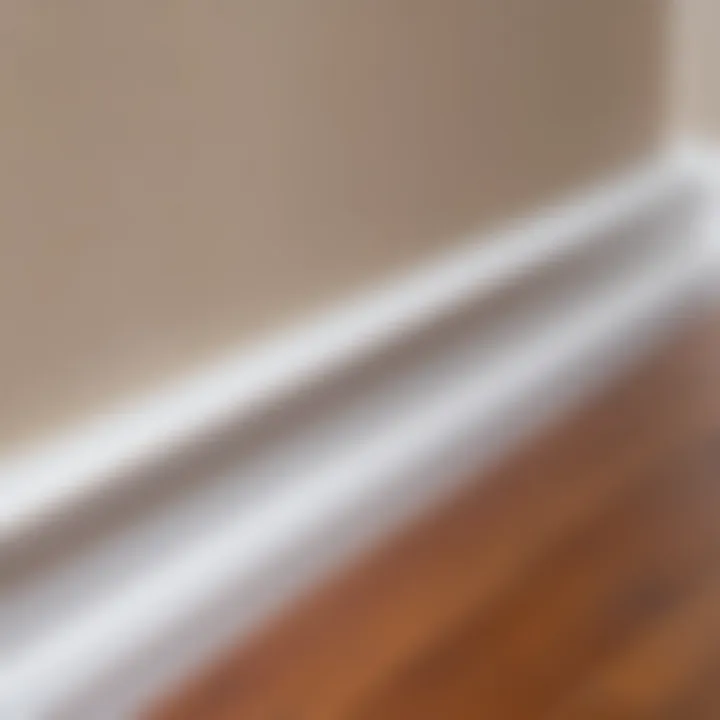
Disposing of Plastic Waste
Disposing of plastic waste correctly is crucial in maintaining an organized workspace and environmental responsibility. Many local guidelines are in place regarding plastic disposal, and following them can prevent future issues. A key benefit of proper waste management is the ability to uphold sustainable methods, thereby reducing your ecological footprint.
Additionally, separating waste for recycling keeps the workspace tidy. Nevertheless, individuals may find this process intimidating due to the need for knowledge about local recycling regulations.
Storing Tools Safely
Storing tools safely after a project not only prolongs their lifespan but also minimizes the risk of accidents. A well-organized storage system can streamline workflow on future projects. This characteristic makes proper storage options beneficial, as they save time and effort in searching for tools later.
Despite these advantages, developing an efficient storage means may require upfront investment in organizational solutions, which can be seen as a disadvantage initially.
Final Inspection
Conducting a final inspection is a crucial step post-cutting procedures. This involves reviewing the work completed to ensure that all cuts meet the desired specifications and quality standards. A fundamental advantage of a final inspection is the opportunity to correct potential mistakes before they escalate into more significant problems.
This process helps to reinforce good practices and ensures that the finished product is satisfactory. However, it can be time-consuming and may require an attentive eye, which not all individuals might possess.
"Attention to detail in post-cutting procedures can significantly affect the quality and aesthetics of your project."
Common Challenges and Solutions
Understanding common challenges faced when cutting plastic baseboards is crucial for achieving professional results. Missteps can lead to wasted materials and increased frustration. By knowing potential pitfalls, the DIYer can be more prepared to overcome obstacles. Experience, both from successes and mistakes, helps refine technique over time. This section explores specific issues such as uneven cuts and chipping, providing effective solutions.
Dealing with Uneven Cuts
Uneven cuts can occur for various reasons, and recognizing this error is the first step towards resolution.
Identifying Mistakes
Identifying mistakes is a vital aspect of the cutting process. Often, cuts do not align properly during installation. One common reason stems from inaccurate measurements or lack of a steady hand while cutting. Noticing these mistakes early can save time and material. It is important to scrutinize the edges after cutting. Uneven edges can compromise the overall appearance. A helpful characteristic of identifying mistakes is that it encourages a mindset focused on precision and improvement.
Tools for Correction
Tools for correction play an essential role in rectifying uneven cuts. A simple hand file or power sander can effectively smooth out jagged edges. Adopting these tools offers the advantage of avoiding waste. However, caution is necessary to avoid removing too much material. The precision of the tool can influence the correction quality. A careful approach can help achieve a better outcome.
Preventative Measures
Preventative measures ensure the project goes smoothly from the start. Taking time to measure accurately and double-checking before making cuts can reduce errors. Using clamps while cutting can help stabilize the plastic. This practice minimizes movement, leading to cleaner edges. Advantages include time efficiency and reduced material loss.
Managing Chipping and Cracking
Chipping and cracking are frequent challenges when cutting plastic baseboards. Addressing these concerns can enhance the final appearance of your project.
Causes of Damaged Edges
Many causes lead to damaged edges. Using an incorrect cutting tool, applying excessive pressure, or cutting at the wrong angle can result in chipping. Understanding these causes helps tailor the approach to cutting. Identifying these issues early on is beneficial as it dictates the choice of material and techniques. By taking this into account, better outcomes can be expected.
Repair Methods
Repair methods are important for salvaging damaged sections. Depending on the severity, methods might range from using adhesive fillers to re-cutting the section to size. Utilizing an appropriate adhesive can create a seamless repair. This characteristic ensures that the repair blends well into the overall design. Having a few repair methods in mind can ease the restoration process.
Choosing the Right Saws
Choosing the right saws is critical to cutting success. Different saws provide different results. A miter saw is preferred for precise angle cuts, while a jigsaw works well for curves. Each option presents unique features that contribute to the cutting efficiency. A common advantage of the right saw is the reduced risk of cracking during cuts. However, selecting the wrong tool may lead to unnecessary frustration and wasted materials.
Key Point: Always examine your methods and tools. Addressing these common challenges will lead to a smoother experience and enhance your skills in cutting plastic baseboards.
Finale
In the realm of home improvement, effectively cutting plastic baseboards holds significant importance. This practice not only enhances the aesthetic appeal of interiors but also ensures a proper fit, fostering lasting durability. Understanding various cutting techniques can help both DIY enthusiasts and professionals achieve a precise outcome with minimal effort. Knowledge about tools, measurement, and safety strongly contribute to the overall efficiency of the task.
Recap of Key Points
To summarize the essentials covered in the article:
- Diverse Materials: Familiarity with different types of plastic, such as Polyvinyl Chloride (PVC), Polypropylene (PP), and High-Density Polyethylene (HDPE), is crucial for appropriate material handling.
- Preparation: Ensuring proper preparation, including necessary tools, accurate measurement, and efficient marking, forms the foundation for successful cutting.
- Cutting Techniques: Knowledge of methods like using a miter saw, utility knife, or power saw empowers the user to select the best technique for the job.
- Post-Cutting Procedures: Smoothing edges and maintaining a clean workspace reflect professionalism and attention to detail.
- Challenges: Addressing common challenges, such as uneven cuts and chipping, enhances the quality and longevity of the work performed.
Final Thoughts on Best Practices
Adopting best practices in cutting plastic baseboards can vastly improve results. Prioritize the following considerations:
- Safety First: Always wear safety goggles and handle tools with care to prevent injuries.
- Choose the Right Tools: Using suitable cutting tools ensures precision and reduces the risk of material damage.
- Plan Before Cutting: Take time to plan measurements and cuts accurately to avoid mistakes.
- Cleanliness After Work: Dispose of any waste properly and organize tools to maintain a tidy workspace.
By integrating these insights and practices, one can elevate their skills in the craft of cutting plastic baseboards, resulting in a polished and professional finish.