Constructing a Durable Floor for Your Metal Garage
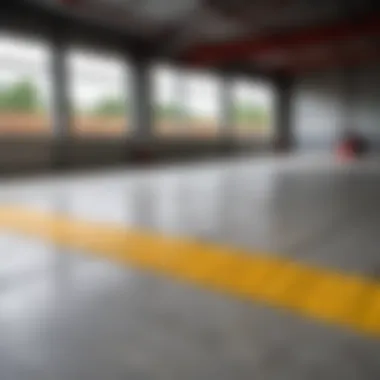
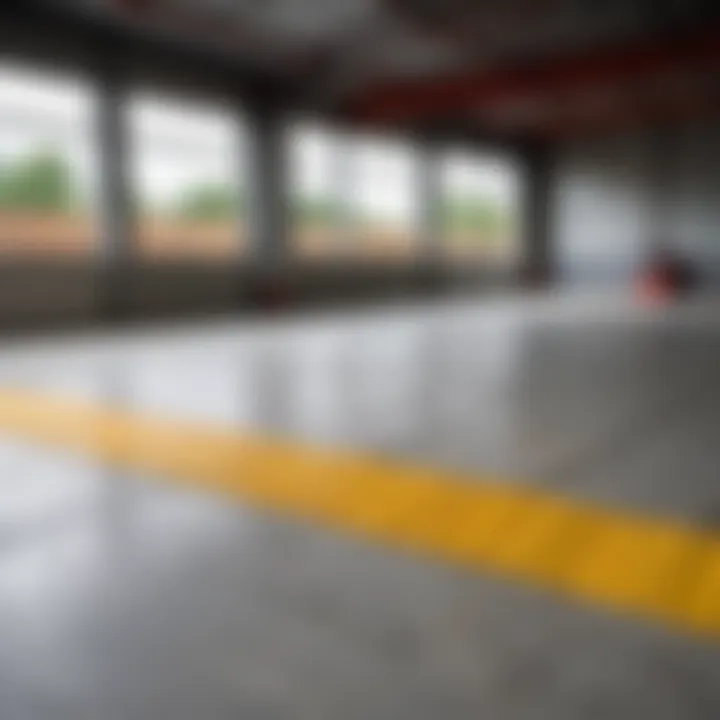
Intro
Constructing a robust floor for your metal garage is no small feat, but with the right approach, it can be a gratifying endeavor. A solid floor not only enhances the functionality of the space but also contributes to the longevity of the entire structure. In this guide, we’ll shed light on the various steps involved, ensuring your project is set up for success, whether you're a DIY enthusiast or a seasoned builder. From the planning phase to the materials you'll need, we’ll cover it all in a manner that’s straightforward and easy to follow.
Проектирование и планирование
Underestimating the planning phase is a common pitfall. Before laying a single tile or pouring concrete, it's essential to understand how to select the right project for your DIY garage floor. Factors such as the size of the garage, the type of vehicles or items stored inside, and your local climate conditions all play a pivotal role in determining the ideal approach.
Как выбрать проект для DIY
When deciding on a project for your floor, consider a few key aspects:
- Purpose of the Garage: Are you using it primarily for parking, storage, or as a workshop? Your intended use will dictate the material choices and design.
- Traffic Expectations: How much wear and tear will the floor experience? High-traffic areas may require more durable solutions.
- Environmental Conditions: Think about moisture levels, temperature fluctuations, and other local weather concerns. For instance, if you're in a wet climate, waterproofing becomes crucial.
Оценка времени и ресурсов
Now that you’ve got a project in mind, it's time to evaluate your timeline and resource allocation. A proper schedule not only keeps you on track but also helps in managing costs efficiently. Here are tips to consider:
- Create a Checklist: Outline each step of the process, from preparation to installation. This makes it easier to track your progress.
- Estimate Time: Allocating sufficient time for each task, including drying times for materials, prevents rushing toward the end.
- Budgeting: Determine what you can afford. Include all expenses, from materials to tools, in your calculation to avoid surprises down the road.
Remember: Planning ahead often saves time and money in the long run. Skipping this step might lead to mistakes that are costly and time-consuming to fix.
Выбор материалов
Choosing the right materials lays the foundation for a successful project. Not all materials suit every garage, and understanding what’s available is half the battle.
Типы материалов для различных проектов
When it comes to garage floors, consider popular choices:
- Concrete: Resilient and easy to customize; ideal for heavy loads.
- Epoxy Coatings: Offers a durable finish and is resistant to spills, making it excellent for workshops.
- Rubber Tiles: Provide comfort and noise reduction, perfect for garages doubling as workspaces.
- Stained or Polished Concrete: Aesthetic and easy to clean, gives a nice finish while retaining durability.
Советы по покупке и экономии
Purchasing materials doesn't have to break the bank. Here are some practical tips:
- Shop Around: Local hardware stores, online retailers, and wholesale outlets often have varying prices.
- Consider Bulk Purchases: If you're working on a larger garage, buying in bulk can lead to significant savings.
- Look for Sales or Discounts: Keep an eye out for seasonal sales or coupon codes on construction supplies.
Prelims to Garage Flooring
Constructing the floor of a garage is not just an afterthought—it's the very foundation that supports the entire structure and its contents. A proper garage floor sets the tone for functionality, durability, and overall efficiency in use. When considering how to build a floor for a metal garage, several factors come into play.
First and foremost, the importance of a solid garage floor lies in its capacity to withstand heavy loads, provide a smooth surface for mobility, and manage potential moisture issues. For example, if you’re planning to park multiple vehicles or store heavy tools and equipment, a sturdy floor can prevent cracking or sagging over time, which could lead to costly repairs down the road.
Moreover, a good floor design can enhance the aesthetic appeal of your garage, which can be an important factor if you envision using the space for hobbies or work. A well-finished floor doesn’t just look nice; it also plays a crucial role in keeping the entire area easily manageable in regards to cleaning and maintenance.
The Importance of a Proper Garage Floor
When you build it right, a garage floor amplifies your space's functionality. Here are several key reasons why:
- Load Bearing: With vehicles and equipment, the weight can be a real concern. A proper concrete mix, laid with precision, ensures the floor can absorb this load without a hitch.
- Moisture Control: Garages are susceptible to moisture. A well-constructed floor, particularly with a moisture barrier, helps prevent structural issues and mold growth.
- Aesthetic Value: Whether you opt for basic concrete or stylish epoxy coating, a good floor improves appearance. It’s the first thing anyone notices, after all.
"The success of a garage floor often dictates the longevity of everything else built atop it."
Unique Considerations for Metal Garages
Metal garages present their own set of unique challenges. Unlike traditional wooden structures, metal garages can experience significant temperature fluctuations, which affect the floor's integrity. Here are a few considerations to keep in mind:
- Expansion and Contraction: Metal expands when heated and contracts in the cold. It's vital to pick flooring materials that can handle these changes without cracking.
- Installation Surface: Depending on the soil or foundation underneath, you may need to prep that surface differently than you would for a wooden garage. This could include laying gravel to assist drainage or using a vapor barrier to address moisture issues.
- Finishing Needs: The materials you choose, whether it's concrete, epoxy, or rubber, must accommodate the specific requirements of a metal garage to prevent short-term failures.
Creating a durable garage floor is not just about the initial installation but also about planning for the future. Your choices will affect how the space performs over time, directly tying into both functionality and maintenance aspects.
Assessment of the Garage Environment
Assessing the garage environment is a crucial step when constructing a floor in a metal garage. This evaluation ensures the foundation is solid and ready to hold up against the weight and wear that will be placed upon it. Neglecting this step can lead to unforeseen issues, costing time and money down the line. The right analysis can save a lot of headaches.
Evaluating Soil and Foundation Conditions
When you're getting ready to lay down a floor, the first thing you need to do is check out the soil and foundation. Start by digging a little deeper, both literally and metaphorically. This isn’t just about looking at the surface; you want to understand what’s underneath. A common mistake folks make is assuming all soil is created equal. Soil can vary widely in terms of its strength and stability. For instance, sandy soils can shift under load, while clay soils expand and contract with moisture, both presenting unique challenges.
Upon evaluating, it’s a good idea to conduct a soil test. This might show you the soil's composition, bearing capacity, and moisture levels. If the soil is too loose or unstable, you might need to consider options like reinforcements, a thicker base, or even excavation to put in a more stable foundation. Remember, the strength of the garage floor is only as good as what it's built upon.
Benefits of Evaluating Soil Conditions:
- Ensuring stability and longevity of the garage floor.
- Identifying the need for reinforcement strategies that can prevent future issues.
- Understanding how the floor will hold up under various loads.
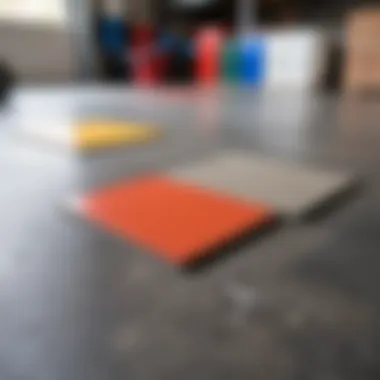
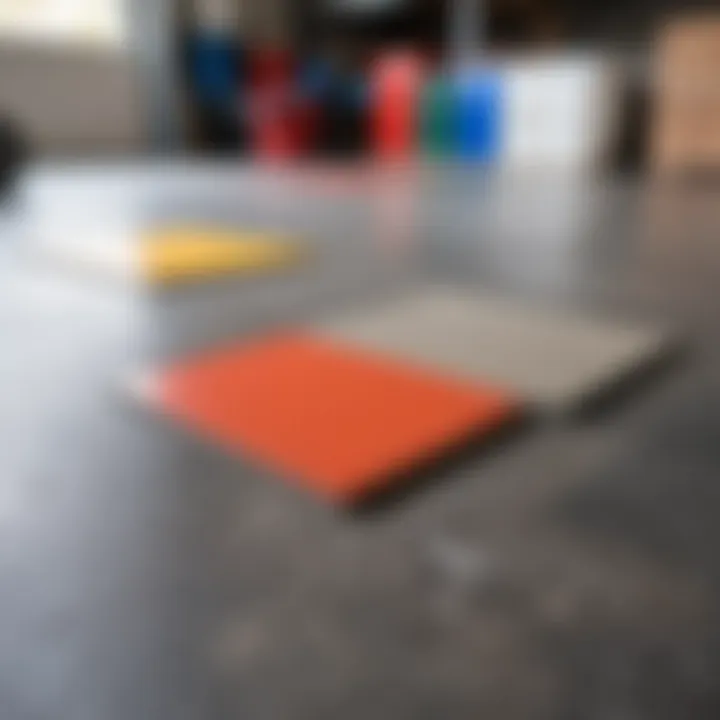
Understanding Moisture Levels
Next up is moisture levels. This aspect often gets overlooked but can be a silent killer when it comes to a garage's structural integrity and floor health. Water moves through soil in unexpected ways, pulling the microscopic strings that can lead to bigger problems, like cracking and even mold growth.
One way to assess moisture levels is to perform a simple moisture test on the ground. This could involve placing a plastic sheet on the soil for 24 hours. If you see condensation on the underside of the sheet, that’s a telltale sign you’ve got moisture issues that you’ll need to address.
Additionally, consider the drainage systems surrounding the garage space. Ensure gutters and downspouts are directing water away from the structure. The faster rainwater gets away, the better it is for the floor and the metal structure itself.
Considerations for Moisture Management:
- Proper drainage solutions to prevent water pooling around the foundation.
- Use of vapor barriers to protect the floor from moisture coming up.
- Regular monitoring of moisture levels, especially after rainfall.
Just because you can't see it doesn't mean it’s not there; moisture knows how to hide and create chaos.
By thoughtfully assessing these two critical aspects—the soil and moisture levels—you lay the groundwork for a garage floor that stands the test of time. Investing this effort upfront pays dividends you won’t see until years later.
Selecting Appropriate Materials for Garage Flooring
When it comes to choosing materials for the floor of a metal garage, the options are diverse but not every choice will stand the test of time and usage. The right material plays a crucial role not only in enhancing the overall aesthetic but also in providing durability, resistance to wear and tear, and ease of maintenance. Let's explore three common options: concrete, epoxy coatings, and rubber flooring.
Concrete as a Foundation
Concrete is perhaps the most traditional and widely accepted choice for garage floors. It’s synonymous with strength and longevity. A concrete foundation is capable of bearing heavy loads and resists the wear associated with vehicle traffic, which is vital in a garage setting.
- Durability: Concrete can last for decades if properly cured and maintained. For a metal garage, concrete provides a stark contrast to the steel structure, ensuring a solid and stable base.
- Cost-Effective: While the initial investment might require more upfront funds, the long-term savings from maintenance make it an economic choice.
- Versatile Finishing Options: Once the concrete floor is laid and cured, homeowners can choose from various finishes to suit their desired aesthetics, making it both functional and visually appealing.
In constructing the concrete foundation, it’s important to plan for reinforcement and proper drainage to avoid future problems like cracking or water pooling.
Epoxy Coatings for Enhanced Durability
Epoxy coatings take the durability of concrete to the next level. Once applied to a concrete surface, it forms a chemical bond, making the floor resistant to stains, chemicals, and impacts. Here’s why applying an epoxy coating could be beneficial:
- Enhanced Appearance: Epoxy floors can be customized in various colors and finishes, providing a clean, glossy surface that can brighten up the garage.
- Improved Safety: Many epoxy coatings can be infused with anti-slip additives, reducing the chances of slips and falls, particularly in high-traffic areas or when working with oil and other slippery substances.
- Resistant to Wear and Tear: Epoxy coatings help to create an impermeable barrier against moisture, protecting the concrete underneath while also reinforcing the floor’s strength.
Rubber Flooring Options
Rubber flooring is another viable option, particularly for those who prioritize comfort and noise reduction. Over the years, it has gained traction among DIY enthusiasts and builders, and for good reason.
- Comfort: Rubber flooring provides a softer surface, which can be advantageous for anyone spending extended time in the garage working on projects. Standing on a rubber floor is easier on the joints.
- Shock Absorption: Placing heavy tools or equipment on rubber flooring can help lessen the impact and prevent damage to both the floor and objects themselves.
- Easy Maintenance: Rubber is water-repellent and easy to clean, which can save time in upkeep.
However, it’s worth noting that rubber flooring may not be as durable under extreme weights compared to concrete, so consideration should be given regarding how the garage will be used.
A well-considered choice of materials not only extends the life of the garage surface but also significantly impacts the overall utility and appearance of the space.
Preparation Steps Before Installation
Before diving into the installation of a garage floor, there’s a significant amount of prep work that needs to be tackled. This phase is critical for ensuring not just the quality of the floor, but also its longevity. Rushing through these steps might lead to an unstable surface or exacerbate existing issues. So, let’s break down what needs to be done.
Clearing the Garage Space
First things first, clearing out the garage space is essential. It may sound simple, but it’s a foundational step that sets the tone for everything that follows. A clutter-free environment not only provides a clear area to work but also ensures that you won't trip over random items while pouring concrete or laying tiles.
When you’re about to clear out the space, take the time to categorize what you have. There are generally three categories for your items:
- Keep: Tools and materials you regularly use.
- Store Elsewhere: Seasonal items or rarely used tools that can go into a storage shed or another location.
- Discard or Donate: Broken items or those that haven’t been used in a year or more.
This categorization makes the process smoother, allowing you to reclaim your garage space effectively. Besides, a clean slate will help you visualize your new floor layout, helping to prevent any mistakes during installation.
Repairing Existing Surfaces
Once the area is clear, you need to address any existing surface issues before laying down anything new. This step can’t be brushed aside if you want a finished product that’s rock solid. Here, you’ll likely find cracks, uneven patches, or maybe pealing paint that needs to be attended to.
When it comes to repairing these surfaces, it’s important to:
- Inspect Thoroughly: Walk around and examine any blemishes or damage on the floor. Use a moisture meter on concrete if needed, this step will help you get a firm grasp on the health of the existing surface.
- Fill in Cracks and Holes: Use a concrete patch product for large cracks and holes. For smaller cracks, a crack filler or epoxy can work wonders. The aim is to create a level base for whatever flooring you choose to install.
- Leveling the Surface: If you're working with an uneven floor, self-leveling compounds may be necessary. They help fill dips and ensure that upon drying, you have a perfectly smooth surface.
This surfaces repair stage might feel like an uphill battle, but it’s key to preserving the integrity of your floor installation. After all, if the surface underneath isn’t stable, why would you expect the new flooring to hold up?
"An ounce of prevention is worth a pound of cure."
Taking these preparatory steps ensures that your investment in flooring won’t go to waste in the long run, saving you from potential headaches later on.
Installing a Concrete Floor
Installing a concrete floor in a metal garage is not merely about functionality; it’s about laying a strong, reliable foundation that will stand the test of time. A concrete floor can handle the weight of vehicles, tools, and heavy equipment, while also providing a surface free from wear and tear that other materials might suffer over time. Beyond durability, it offers a solid barrier against moisture, pests, and various environmental factors that often plague less robust flooring systems.
Selecting concrete comes with numerous benefits as well, including ease of cleaning, its ability to withstand high traffic, and resistance to stains. However, it’s essential to approach this installation with forethought, ensuring that all preparatory measures, mixing ratios, and curing stages are meticulously handled. When pour and set correctly, concrete becomes a steadfast companion for any metal garage.
Creating a Form for the Concrete
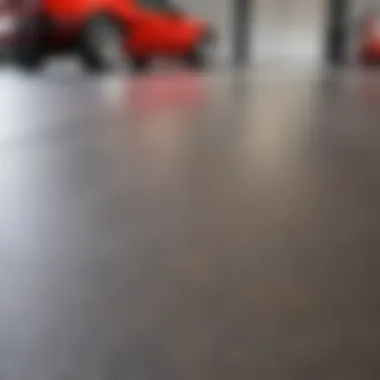
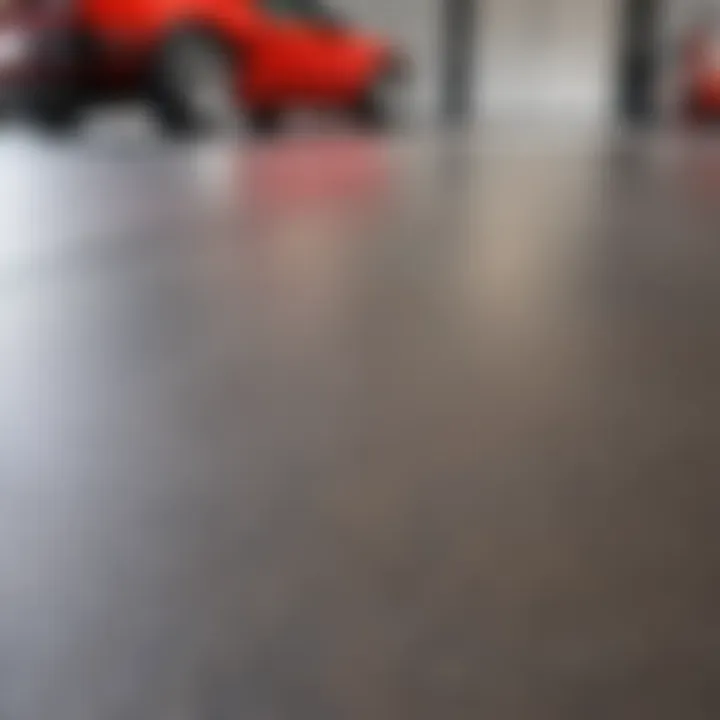
Creating an adequate form for pouring concrete is one of the crucial first steps in the installation process. The form dictates the final shape and size of your concrete slab, so attention to detail is vital. Begin by determining the dimensions of the slab; it’s advisable to mark out the area with stakes and string to visualize the space clearly. Ensure that the area is free from any debris and level.
Once marked, construct a wooden frame using 2x4s or plywood. This form should align with your measurements and be secured tightly to withstand the weight of the concrete. Additionally, think about incorporating a slight slope to direct water runoff away from the garage, which will guard against pooling and moisture damage.
"A well-built form is like a blueprint for success; it sets the stage for a solid outcome."
Pouring and Leveling the Concrete
Pouring concrete is akin to a dance; rhythm and timing are essential for achieving a seamless finish. Before mixing the concrete, ensure that your form is clean and prepared. Consult specific instructions on the concrete mix you're using, as every project may have slightly different needs. When ready, pour the concrete into the form in sections, using a wheelbarrow for easier transport if needed.
As you pour, the focus should be on achieving an even distribution throughout the form. Utilize a straightedge or screed board to level the surface effectively. This may require several passes over the slab until it’s smooth and uniform. Remember, it’s crucial to keep the concrete wet during leveling to avoid cracks as it begins to set.
Curing the Concrete for Strength
Once the concrete has been poured and leveled, curing is the next important phase that cannot be overlooked. Curing involves maintaining moisture in the concrete, allowing it to strengthen over time. In general, concrete should be kept wet for at least a week after pouring to ensure adequate hydration. Consider draping wet burlap or using curing compounds to assist in this process.
The benefits of thorough curing are enormous. It prevents surface cracking, ensures longevity, and reinforces the strength of the floor. If you're in an area with hotter climates, be particularly vigilant; concrete can dry too quickly without proper care, leading to disastrous results.
An effective approach to curing is to choose specific days of the week for checking the moisture levels, and adjust as needed to maintain optimal conditions. Remember, a well-cured concrete floor can stand as a testament to the work put into crafting a robust metal garage.
Applying Epoxy Coating
Applying an epoxy coating is a crucial step that can greatly enhance the durability and aesthetic appeal of the floor in your metal garage. A floor with an epoxy finish not only stands up to the typical rigors of a garage environment but also boasts easy maintenance qualities. It creates a reliable barrier against common issues such as stains, spills, and other contaminants. In essence, epoxy coatings transform a plain concrete slab into a robust, functional platform ready for any task.
Preparing the Concrete Surface for Coating
Before diving into applying epoxy, thorough preparation of the concrete surface is paramount. If you skip this step, you may as well be throwing money down the drain. Here are key factors to consider:
- Clean the Surface: Start with a deep clean. Use a degreaser to remove any oil stains and a stiff brush to scrub away dirt and dust. This ensures that the epoxy adheres properly.
- Patch Any Cracks: No surface is perfect. Fill in cracks and holes with a concrete patching compound suitable for garages. Allow enough time for it to cure before moving forward.
- Etch the Surface: To promote adhesion, consider etching the concrete. This can be done with an etching solution, which helps create a rough texture for the epoxy to grip onto.
Adhering to these processes makes all the difference. Skipping proper cleaning can lead to peeling or chipping down the line, so take your time here.
Mixing and Applying the Epoxy
Getting the mixing right is often where people trip up. Most epoxy kits will come with both a resin and a hardener. Follow the manufacturer’s instructions for the precise ratios to ensure the correct chemical reaction. A common mix is two parts resin to one part hardener.
- Use a Paint Mixer: When combining, a paint mixer on a drill can help achieve a lump-free solution, saving you from any nasty surprises during application.
- Timing is Key: Understand the pot life of your epoxy, which tells you how long you have to work before it begins to harden. You want to apply the epoxy while it’s fresh, so prioritize efficient application.
When applying, use a roller for a smooth finish. Start in the farthest corner of the garage and work towards the exit to avoid stepping on wet epoxy. For corners and edges, a brush may serve you better. Don’t rush here; the application should be even and methodical.
Final Touches and Curing Process
After laying down the epoxy, it’s crucial to let it cure properly. This curing period is what solidifies the finish and provides that robust layer of protection.
- Follow Curing Times: Refer to the manufacturer’s guidelines on curing times to know when it’s safe to walk on the floor and when it is ready for heavy loads. Typically, a minor walk-on time ranges from 2 to 24 hours, but full chemical resistance can take several days.
- Consider the Environment: Keep in mind that temperature and humidity levels may affect curing times. It’s best to keep the garage well-ventilated but avoid drastic temperature changes during this period.
In summary, taking the right steps both before and during the epoxy application leads to a long-lasting, high-performance floor. Applying this coating not only fortifies your floor but also improves its overall look – a win-win situation for any garage owner.
"Proper prep and application of epoxy can save you from costly repairs in the future. Don’t cut corners!"
Rubber Flooring Installation Process
The installation of rubber flooring in a metal garage can truly transform the usability and aesthetic of the space. Rubber flooring offers numerous advantages—it's durable, provides traction, and is resistant to various chemicals. It's particularly relevant given the unique conditions of metal garages, which can experience different levels of moisture and temperature changes. Understanding the correct installation process is key to ensuring that this flooring option performs its best.
Choosing the Right Rubber Flooring Material
When selecting the right rubber flooring material, several factors come into play. It's important to consider the thickness of the rubber. Thicker rubber tiles tend to offer better cushioning and sound absorption, while thinner options can be a cost-effective choice for low-traffic areas. Many who are knowledgeable about garage needs recommend selecting products with an appropriate texture for enhanced grip, especially in a workspace that might see spills or heavy equipment.
There's a variety of types to choose from, such as interlocking tiles, rolled rubber flooring, and mats. Interlocking tiles are particularly popular due their ease of installation, as they can be installed without adhesive. Rolled rubber, on the other hand, provides a seamless look and can cover larger spaces more efficiently. In contrast, mats might fit well in smaller areas or to place beneath specific machinery.
One thing worth noting is to ensure that the rubber flooring is suitable for indoor use. Some outdoor rubber flooring options might not perform well in a closed environment due to off-gassing and odor. Checking for high-quality, low-VOC (volatile organic compounds) materials can result in a healthier garage environment.
Preparing the Base for Installation
Preparation of the base is a crucial step before laying down rubber flooring. First, the floor should be thoroughly cleaned. Removing all debris, dust, and any adhesive residue is a must to ensure a strong bond between the rubber and the surface beneath it. Sometimes, a light scrub with soapy water can work wonders to lift stubborn grime. After cleaning, letting the area dry completely is just as important; moisture trapped beneath can lead to mold or floor deterioration over time.
Some people tend to overlook the importance of leveling the concrete surface before installation. If there are any cracks or uneven areas, they should be filled with an appropriate leveling compound. This will not only improve the installation process but also extend the life of your flooring. Imperfections in the base can lead to cracks in the rubber and frustration down the line as you visit the garage.
Laying and Securing the Rubber Tiles
When it’s time to install rubber tiles, a systematic approach can save you a lot of hassle. Start by mapping out where the tiles will go. Using a chalk line can help establish clean, straight lines that will keep your tiles aligned. Having the right layout accommodates the natural expansion and contraction of the rubber, particularly in environments with varying temperatures.
As you lay down the tiles, ensure that they're pressed firmly together to avoid gaps. If you're using interlocking tiles, it's advisable to alternate tiles from different boxes to create a more uniform appearance. Once all tiles are in place, securing them with appropriate adhesives enhances stability.
Finally, rolling over the surface with a heavy roller can help to firmly bond the tiles to the floor, removing any trapped air. Allow the floor to set as recommended by the manufacturer, usually around 24 hours, before subjecting it to regular use. Pay attention to instructions regarding curing times, as skipping this step can compromise the longevity and appearance of your floor.
"Proper preparation and installation can make a world of difference in the performance of your rubber flooring. Don’t underestimate it!"
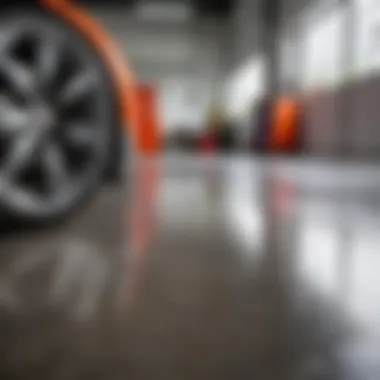
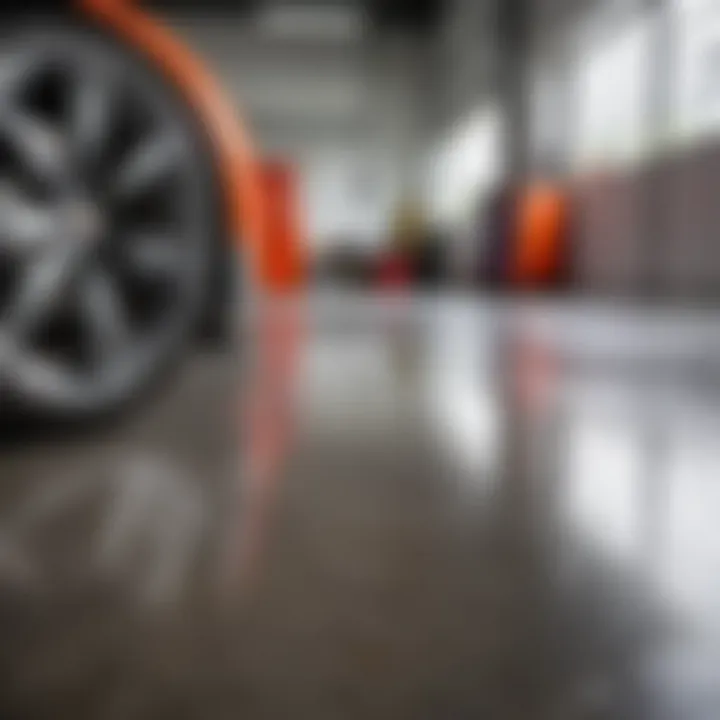
Following these steps closely will not only improve the quality of your rubber garage floor but also provide a lasting surface that can withstand the demands of a garage environment, making it a smart choice for any DIY enthusiast.
Maintenance of Garage Flooring
Maintaining the floor of your metal garage is not just about aesthetics or keeping things tidy. It’s about preserving the structural integrity of the floor itself and extending its life. A well-maintained garage floor enhances safety, promotes a more functional workspace, and saves you from hefty repair costs down the line. When neglected, even the toughest flooring can succumb to wear and tear, which may lead to significant deterioration or damage.
Benefits of Regular Maintenance
- Enhanced Longevity: Consistent upkeep prevents small issues from snowballing into big headaches, thereby prolonging the life of your flooring.
- Safety: A clean and well-managed floor minimizes risks like slips and trips, especially when you’re maneuvering heavy tools or vehicles.
- Cost-Effective: Simple maintenance can drastically reduce the likelihood of needing significant repairs, which can be a wallet-buster.
It's essential to have a maintenance routine tailored specifically for the type of flooring in your garage. Whether it's concrete, epoxy, or rubber, understanding what works best for your materials will keep them in tip-top shape.
Regular Cleaning and Upkeep
Keeping your garage floor clean is often about using the right methods and products. Different flooring surfaces require distinct cleaning regimens. For example, concrete floors can often collect dirt and oil residue, while a rubber floor may be more resistant to spills but still needs periodic attention.
Key Cleaning Steps:
- Sweeping or Vacuuming: Remove dust, dirt, and debris regularly. This is a no-brainer but crucial for both aesthetics and safety.
- Mopping: Use a suitable cleaner diluted with water. Make sure it’s effective for your floor type; for instance, when cleaning epoxy, use a pH-neutral cleaner.
- Stain Removal: Address stains promptly. For oil or grease, try using dish soap mixed with warm water. Let it sit for a bit before scrubbing gently.
You don't have to treat cleaning as a laborious task – make it a part of your routine, like taking out the trash or changing the oil in your car. Just a few minutes each week can go a long way in preserving the beauty and function of your garage floor.
Identifying and Addressing Damage
Even with regular maintenance, wear can happen. It's vital to catch damage early, before it becomes a pricey problem. Look for signs like cracks, peeling, or discoloration. Each of these can indicate underlying issues that need attention.
Common Signs of Damage:
- Cracks and Chips: These can be architectural considerations gone awry or could lead to bigger structural issues.
- Deteriorating Coatings: If your epoxy or other coatings look worn or are bubbling, it might be time to reapply or repair.
- Surface Discoloration: Changes in color can indicate moisture problems or material degradation.
Addressing these issues can include:
- Repairing Cracks: Use a suitable crack filler for the type of flooring you have. Make sure to follow the manufacturer’s instructions closely.
- Re-coating: If you find substantial wear on the surface, consider redoing the epoxy or protective layer. It can sometimes be a simple DIY fix.
- Professional Help: When in doubt, consult a professional. Sometimes, it’s best to let the pros handle what they do best.
"An ounce of prevention is worth a pound of cure."
Regular maintenance paired with early detection of damage ensures a long-lasting floor in your metal garage. In the end, treating your garage’s floor with due respect makes the entire space more enjoyable and functional.
Common Mistakes to Avoid
Constructing a floor in a metal garage might seem straightforward, but there are pitfalls even seasoned DIYers can stumble into. Avoiding these common mistakes not only saves time and money but also ensures a solid, durable foundation that stands the test of time. Being cautious about how you approach the installation process could safeguard your project from future headaches.
Overlooking Moisture Control
One of the most significant missteps folks make is not giving moisture control the attention it deserves. If you're in an area known for high humidity or frequent precipitation, ignoring this factor could lead to all sorts of trouble down the road. Water can seep into the concrete, create mold, and cause the floor to crack.
Here are some thoughts to keep in mind:
- Assessment of Surroundings: Before you lay down the concrete or rubber flooring, consider the environment surrounding your garage. Is it prone to flooding? Is there proper drainage around the structure? Knowing this can inform your next steps.
- Moisture Barriers: Installing a moisture barrier beneath your floor is almost a no-brainer. A vapor barrier can help keep moisture from rising up through the concrete, creating a dry and stable environment. This is a particularly smart move if your garage will house items sensitive to dampness.
- Ventilation Solutions: Good airflow is essential. Poor ventilation can trap moisture in the garage, leading to these persistent issues. Adding vents or even a dehumidifier can make a world of difference.
"Controlling moisture isn’t just about today, it’s about preparing for tomorrow. A vigilant approach keeps your garage floor in tip-top shape well into the future."
Neglecting Proper Surface Preparation
Another common slip-up is neglecting to properly prepare the surface before installation. It's critical to remember that the quality of your floor is directly related to how well you prep the surface.
Think of it like cooking - if your ingredients aren’t fresh, no recipe can save the dish!
- Cleanliness is Key: Before laying down any floor material, ensure the existing surface is free of dirt, grease, and other contaminants. Sweep and mop it well; a clean surface promotes better adhesion, especially for coatings like epoxy.
- Leveling the Area: Take some time to check for any dips or bumps in the floor. Ideally, you want a smooth, level base to work with. Consider using a self-leveling compound if necessary. Otherwise, those imperfections could spell disaster later on, leading to uneven wear and tear.
- Repair Cracks and Holes: Don’t overlook any cracks or holes in the underlying concrete. Fill them as needed prior to installation. Failing to do so may result in these cracks expanding over time, which can compromise the integrity of your new floor.
The right preparation transforms your project from a hastily put-together mess to a structure that looks professional and performs well. Clear attention to moisture control and surface preparation can make a world of difference in the longevity of your garage floor.
The End and Recommendations
In wrapping up our guide on constructing a floor in a metal garage, it’s crucial to reflect on the journey taken through each phase of the process. A solid foundation isn't just about aesthetics; it plays a pivotal role in determining how functional and long-lasting your garage will be. Ensuring that you've chosen the right materials, successfully prepared the installation site, and implemented effective maintenance practices goes a long way in providing the garage space with resilience against wear and tear.
The benefits of a well-constructed garage floor are manifold. For starters, you’re setting the stage for a safer and more organized environment. Adequate flooring helps prevent accidents, especially in a busy workspace where tools and vehicles are often in motion. Moreover, investing time in the installation process lays down the groundwork for future enhancements. With a solid floor, you can easily incorporate additional features like storage solutions or even specialized zones for specific activities, be it automotive work or creative projects.
When considering recommendations moving forward, it’s wise to think about potential improvements over time. For instance, you might start with a concrete base and later add coatings or mats to enhance longevity and appearance. Keeping an eye on seasonal changes can influence your maintenance schedule, particularly in climates prone to moisture fluctuations that could affect the flooring integrity.
Remember: Simply constructing a durable garage floor isn’t enough. Regular checks and timely reinforcements will guarantee that the initial efforts continue to pay dividends down the road.
Recap of Key Points
During this entire article, several key points stood out:
- Understanding Environment: Evaluating soil and existing conditions is essential to ensure stability.
- Material Selection: Concrete, epoxy, and rubber each serve unique purposes, contributing positively to floor durability.
- Installation Techniques: Proper pouring, leveling, and curing are critical for solid results.
- Maintenance is Key: Routinely checking and addressing any damage prevents future costs and unsafe conditions.
Future Considerations for Garage Improvements
As you consider potential upgrades to your garage environment, keep in mind:
- Enhanced Climate Control: Depending on your region, insulating your garage or using advanced flooring materials can regulate temperature.
- Smart Technology: Look into automated systems for ventilation or lighting to further improve usability.
- Sustainability: Incorporating eco-friendly materials can not only enhance floor durability but also promote environmental responsibility.
- Customization: Personalizing your garage with unique finishes or markings can also be a great way to create a space that reflects your style and needs.
Ultimately, constructing and maintaining the floor of your metal garage does not just solve a simple issue but instead opens the door to a whole new realm of possibilities. Keeping a long-term view in mind will allow you to adapt and enhance your garage as needs evolve.