Understanding Pressure Gauges in Hydroaccumulators
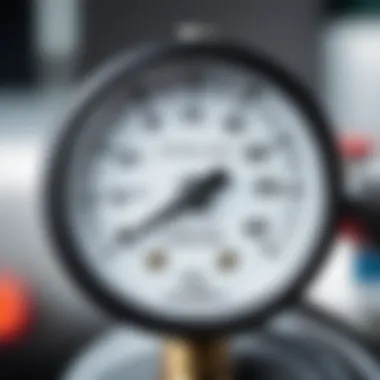
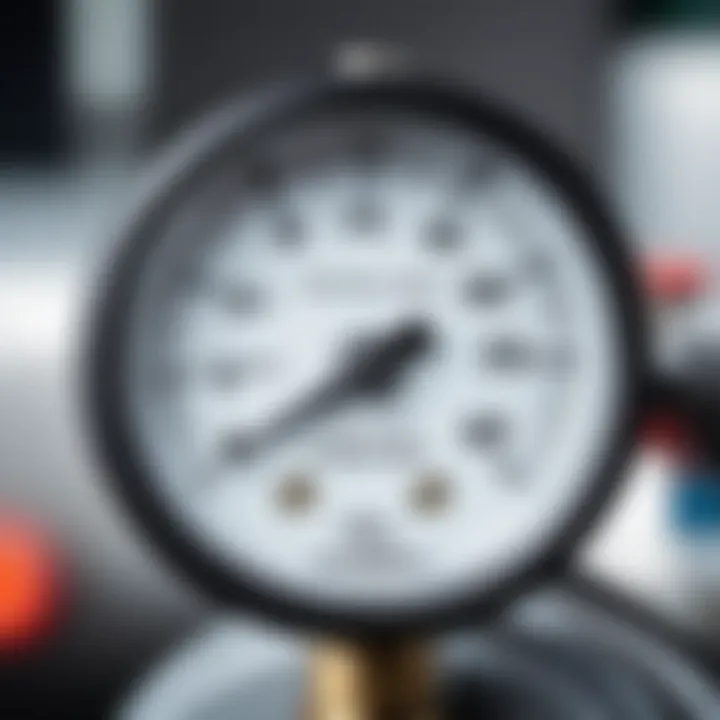
Intro
Hydroaccumulators play a crucial role in various hydraulic systems. They store and manage energy, ensuring smooth operation in applications ranging from automotive to industrial machinery. The pressure gauge is vital in this setup, providing accurate readings of the fluid's pressure within the hydroaccumulator. This allows for efficient monitoring and maintenance, essential for safety and reliability.
Understanding how to select, install, and maintain pressure gauges can enhance the functionality of hydroaccumulators. This knowledge is especially relevant for DIY enthusiasts, interior designers, and builders who often engage with hydraulic systems in their projects.
In this article, we will explore the intricacies of pressure gauges tailored for hydroaccumulators. We will discuss the types of gauges available, installation methods, and best practices for maintenance. By evaluating these aspects, readers can gain practical insights for their endeavors.
Проектирование и планирование
Planning is crucial before embarking on a project that involves hydroaccumulators. It helps ensure that all relevant aspects are considered, minimizing errors and enhancing efficiency.
Как выбрать проект для DIY
Choosing the right DIY project is the first step. Consider your skill level and the specific needs of the project. Assess the complexity of the hydroaccumulator system you will work with and the type of pressure gauge that will best suit your requirements.
A few factors to keep in mind include:
- The system’s pressure range.
- The environment where the gauge will be installed (e.g., temperature, exposure to elements).
- Your budget for materials and tools.
Оценка времени и ресурсов
Estimating the time and resources necessary for the project is vital. Create a checklist to track materials, tools, and manpower required. This will aid in scheduling tasks effectively.
Be realistic about your timeline to avoid rushing through critical steps. Factor in potential delays or complications that may arise during installation or testing.
Выбор материалов
Selecting the right materials for your hydroaccumulator project is essential, especially when it involves pressure gauges. The integrity of the entire system depends on the quality and compatibility of these components.
Типы материалов для различных проектов
Different types of gauges may be made from various materials suited for specific applications:
- Stainless Steel: Offers good corrosion resistance, ideal for high-pressure applications.
- Brass: Commonly used for low-pressure systems and has excellent machinability.
- Plastic: Appropriate for less demanding environments, often used in small DIY systems.
Советы по покупке и экономии
When purchasing pressure gauges, compare prices and features to make informed decisions.
- Look for deals from reputable suppliers to save costs without compromising quality.
- Consider online marketplaces and second-hand options for budget-friendly alternatives.
Keep the project’s specific needs in mind as you shop.
The accuracy and reliability of the pressure gauge directly influence the performance and safety of the hydroaccumulator.
Prologue to Hydroaccumulators
Hydroaccumulators are vital components in hydraulic systems, providing functionality that enhances efficiency and reliability. Understanding their operation and significance helps for effective implementation. Pressure gauges are a key aspect in this context, ensuring that systems operate within safe limits. This section serves as a foundational block for the entire article, guiding readers through the concepts and benefits of hydroaccumulators.
Definition of Hydroaccumulators
A hydroaccumulator is a device that stores hydraulic energy. It uses pressurized liquid to store energy in a confined space. When needed, this energy can be released to perform work, such as lifting, shifting, or hydraulic actuation. They can be found in various applications, including construction equipment, agricultural machinery, and even in elevators.
Hydroaccumulators typically consist of a cylinder divided into two sections by a flexible diaphragm. One section holds a compressible gas like nitrogen, while the other holds the hydraulic fluid. The separation of these two mediums allows for the absorption of pressure changes, hence stabilizing the system.
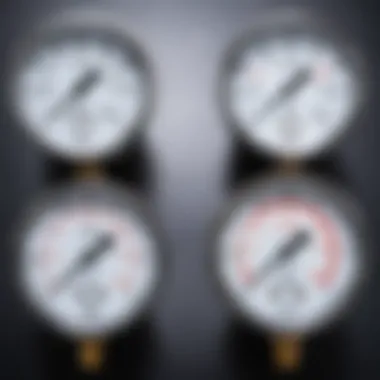
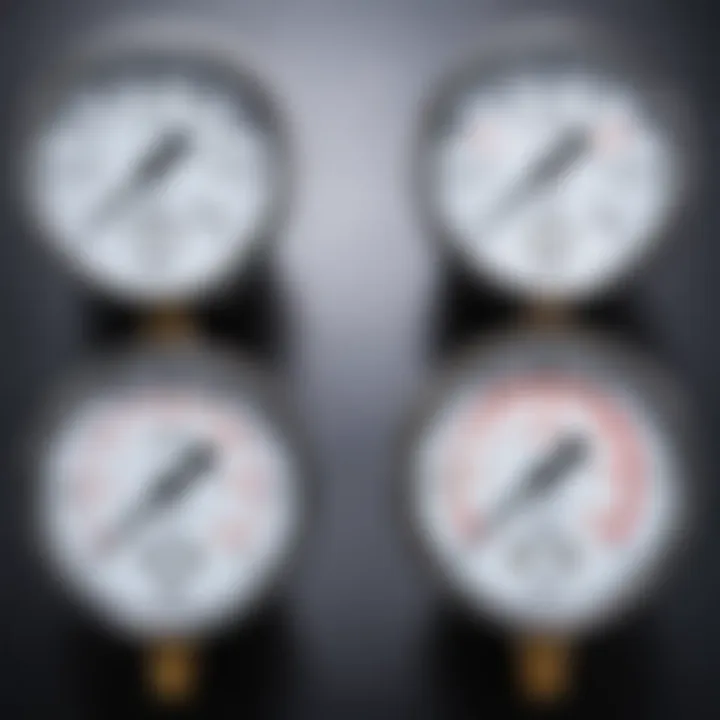
Purpose and Benefits
The purpose of hydroaccumulators includes:
- Energy Storage: They enable systems to recover energy during operation, making processes more efficient.
- Pressure Stabilization: By absorbing hydraulic surges, they help stabilize pressure fluctuations in the system, ensuring consistent performance.
- Fluid Flow Management: Hydroaccumulators can assist in maintaining fluid flow during peak demands, leading to smoother operations.
- Noise Reduction: They can also reduce noise generated by hydraulic pulsations, contributing to a quieter working environment.
In summary, hydroaccumulators are essential for achieving optimized performance in hydraulic systems. Understanding their role lays the groundwork for appreciating the importance of monitoring and maintaining pressure levels with the help of pressure gauges.
What is a Pressure Gauge?
Pressure gauges play a crucial role in monitoring and maintaining the performance of hydroaccumulators. Understanding their function and types is essential to ensure optimal system operation. A pressure gauge measures the pressure of gases or liquids within a system. In the context of hydroaccumulators, it helps to maintain the balance between hydraulic energy storage and release, enhancing both safety and effectiveness.
Functionality of Pressure Gauges
The core functionality of a pressure gauge is to provide real-time data on the internal pressure of a system. This can affect both the operational safety and performance. When connected to a hydroaccumulator, the gauge can quickly indicate whether the pressure is within the designated range. If the pressure is too high or low, operators can take immediate action to adjust the system. Debris in the system or improper maintenance can alter accuracy, making regular checks essential.
Types of Pressure Gauges
Pressure gauges come in various types, each serving unique purposes. The most commonly used types in the context of hydroaccumulators include:
Mechanical Pressure Gauges
Mechanical pressure gauges are often considered the traditional type. They are known for their simplicity and reliability. A key characteristic of mechanical gauges is their use of a Bourdon tube, which bends under pressure. This movement is translated into a reading on a dial. They tend to be durable and don’t require power supply. However, their accuracy can be limited in highly dynamic conditions, and they might not perform well in extreme temperature variations.
Digital Pressure Gauges
Digital pressure gauges offer more precise readings compared to mechanical ones. They convert pressure data into electronic signals displayed on a screen. A significant advantage is their ability to record and store data. This can be particularly beneficial in monitoring long-term system performance. Digital gauges easily incorporate features such as alarms for pressure deviations. However, they require a stable power source to operate. If power is lost, the readings will be unavailable until power returns.
Bourdon Tube Gauges
Bourdon tube gauges, a subtype of mechanical gauges, are widely used for their accuracy and reliability. The unique feature of this type lies in the design of the Bourdon tube, which forms a curved shape. As pressure increases, this tube straightens, moving a needle on a dial to indicate pressure. Their advantage is accuracy in various applications. However, they can be sensitive to shocks and vibrations, which may lead to incorrect readings. Regular calibration is necessary for maintaining integrity in measurements.
Accurate pressure readings are vital for ensuring the safety and efficiency of hydroaccumulators.
Understanding these types will empower operators to choose the right gauge according to their specific needs. Selecting the appropriate pressure gauge enhances the reliability and safety of hydroaccumulators dramatically.
Importance of Measuring Pressure
Measuring pressure is crucial in the operation of hydroaccumulators. This process ensures the system functions within safe parameters. An incorrect pressure reading can lead to severe issues such as equipment failure or dangerous safety hazards. Therefore, understanding pressure stability is vital for anyone involved in maintenance or operation of these systems.
Safety Considerations
Safety must always be a priority in any engineering context. Pressure gauges act as an essential line of defense by providing accurate readings. If the gauge fails to measure correctly, it might indicate safe conditions where danger is imminent. This discrepancy could lead to over-pressurized conditions, which can result in leaks, ruptures or even explosions of hydroaccumulators. Regularly checking and maintaining pressure gauges helps ensure their reliability.
For example, consider how inadequate pressure levels can compromise the integrity of a hydroaccumulator. It can cause components to wear prematurely, risking failure.
- Key safety considerations include:
- Regular calibration of gauges to ensure accuracy
- Immediate replacement of faulty gauges
Monitoring pressure is not only a best practice but also a regulatory requirement in many industries that utilize hydroaccumulators.
Operational Efficiency
Efficient operation of a hydroaccumulator involves maintaining optimal pressure levels. Accurate pressure measurements facilitate effective system design and operation. With precise readings, it becomes easier to adjust parameters, optimize fluid dynamics, and enhance system performance.
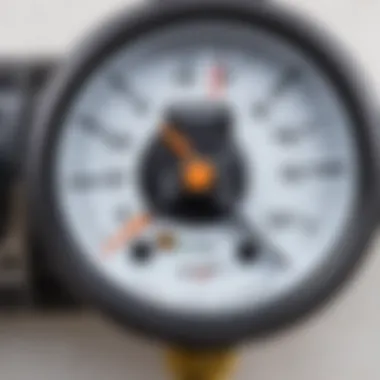
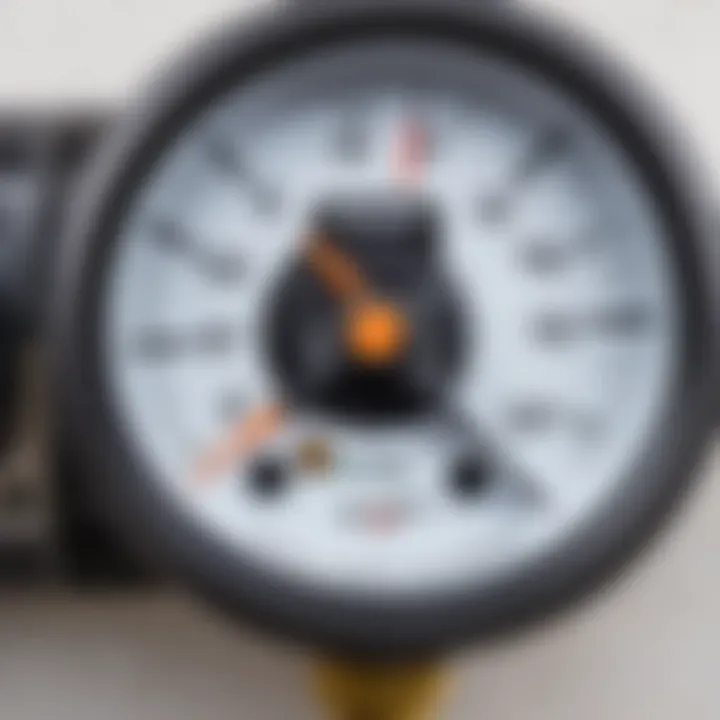
Moreover, consistent measurement of pressure contributes to energy efficiency. For instance, a well-regulated hydroaccumulator can store and release energy more effectively, reducing waste and lowering operational costs.
- Benefits of efficient pressure measurements include:
- Improved energy conservation
- Extended lifespan of the equipment
- Reduced maintenance costs
By recognizing the importance of these factors, individuals in the field can ensure that systems run smoothly and safely while adhering to industry standards. Accurate pressure measurements, therefore, are foundational to operational success.
Selecting the Right Pressure Gauge for Hydroaccumulators
Selecting the right pressure gauge for hydroaccumulators is crucial for achieving optimal performance and safety. The choice of gauge impacts the efficiency of the system, the accuracy of pressure readings, and overall operational reliability. When gauging options, it is essential to evaluate key factors meticulously to ensure the selected instrument aligns with system requirements.
Factors to Consider
Pressure Range
The pressure range of a gauge is significant as it determines how much pressure it can accurately measure. A right pressure range should exceed the maximum pressure expected in the hydroaccumulator system. Choosing a gauge with a narrow range can lead to inaccuracies. On the other hand, an excessively high-pressure range may not offer the necessary detail for lower pressure readings. It is prudent to select a gauge that balances the expected operating range while also providing a buffer for pressure spikes, thereby maintaining the reliable performance of the hydroaccumulator.
Compatibility
Compatibility refers to the ability of the pressure gauge to function correctly with the existing hydroaccumulator system. Different materials and fluids in hydroaccumulators may require specific types of gauges. For example, a gauge might be compatible with water but not with oil-based fluids. Ensuring compatibility helps avoid potential issues, such as corrosion or inaccurate readings. It is important to review the technical specifications of both the gauge and the hydroaccumulator to ascertain suitability.
Accuracy
Accuracy is a vital characteristic of any pressure gauge. It dictates how closely the gauge's readings reflect the true pressure within the system. Pressure gauges typically have an accuracy specification, often expressed as a percentage of full scale. A more accurate gauge usually yields more reliable results, which is integral in maintaining system health and safety. However, higher accuracy often comes at a premium cost, making it essential to consider whether the additional investment aligns with the operational requirements of the hydroaccumulator.
Common Brands and Models
When selecting a pressure gauge, various brands and models may offer distinct features and benefits. Some common brands include:
- Ashcroft
- Wika
- Meucci
- Omega
Each manufacturer has its own models which vary in terms of design, features, and price. It is beneficial to compare models based on user reviews, warranty, and availability of replacement parts to ensure a wise investment in a pressure gauge.
Installation Process for Pressure Gauges
Proper installation of pressure gauges is essential for the accurate measurement of pressure in hydroaccumulators. A correctly installed gauge ensures that readings are reliable, preventing potential safety hazards and operational inefficiencies. Without a proper gauge setup, users may face challenges in maintaining optimal pressure levels, which can lead to equipment failure or disaster. This section will outline the steps necessary for proper installation and highlight common mistakes to avoid. Overall, mastering the installation process contributes to the effectiveness of hydroaccumulators in various applications.
Steps for Proper Installation
The process of installing a pressure gauge involves several critical steps that must be performed with care:
- Select the Right Location: Identify a suitable location for the gauge. It should be easily accessible for monitoring and maintenance, and positioned where it can provide accurate readings without interference from vibrations or other equipment.
- Prepare the Surface: Ensure that the surface where the gauge will be installed is clean and clear of debris. This step reduces the risk of contamination within the system.
- Use Teflon Tape: Apply Teflon tape to the threads of the gauge connection. This prevents leaks and ensures a tight seal when the gauge is connected to the hydroaccumulator.
- Tighten Securely: Screw the gauge into the designated port. Use a wrench to tighten it securely, but avoid over-tightening as it may damage the threads or the gauge itself.
- Check for Leaks: Once installed, activate the system to check for any leaks around the gauge connection. Use soapy water to identify escaping air; the presence of bubbles will indicate a leak.
- Calibrate the Gauge: If applicable, calibrate the pressure gauge to ensure that it provides accurate readings. Refer to the manufacturer's specifications for calibration procedures.
Setting up the gauge properly can greatly extend its lifespan and enhance the accuracy of measurements.
Common Mistakes
Several common mistakes can occur during the installation of pressure gauges. Recognizing these pitfalls can aid in avoiding them:
- Ignoring the Manufacturer's Instructions: Each pressure gauge may have specific installation guidelines. Ignoring these can lead to improper setup and inaccurate readings.
- Over-tightening Connections: Applying excessive force can damage the gauge, resulting in failures or leaks that compromise system performance.
- Poor Location Choice: Selecting an inappropriate location, such as near high-vibration equipment, can lead to false readings due to external interference.
- Neglecting Calibration: Failing to calibrate the gauge upon installation may result in persistent errors, rendering the gauge ineffective for pressure monitoring.
"Proper installation and regular checks play a vital role in the performance of pressure gauges in hydroaccumulators. Negligence could result in costly failures and hazards."
By adhering to best practices, one's installation process will significantly enhance the reliability and accuracy of pressure gauges in hydroaccumulators. Understanding these steps and avoiding common mistakes ensures that users can maintain safe and efficient systems.
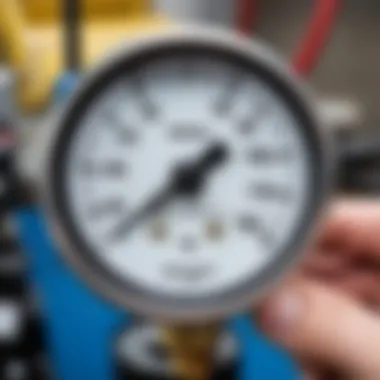
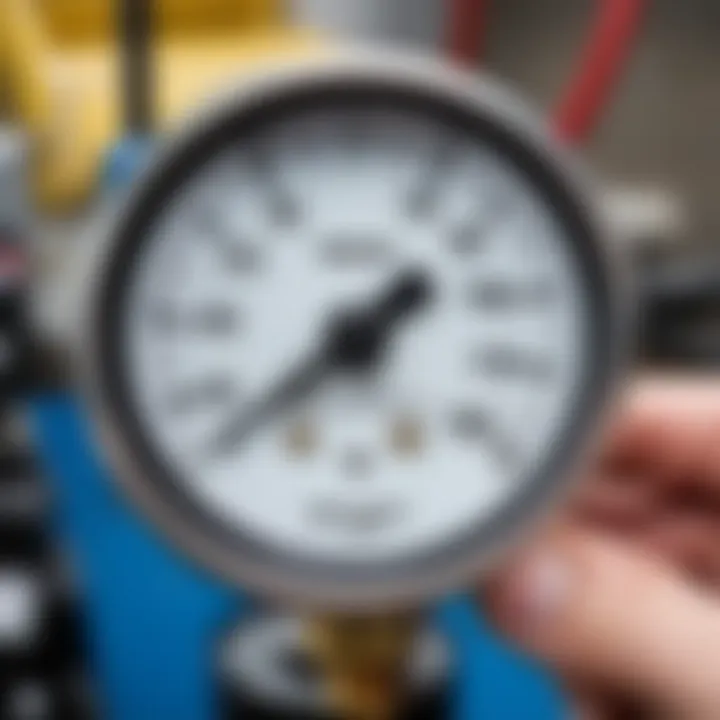
Maintenance of Pressure Gauges
Maintaining pressure gauges is crucial for ensuring their accuracy and longevity. Regular maintenance not only prolongs the life of the gauge but also assures that it performs reliably in measuring pressure within hydroaccumulators. The responsibilities of the user include routine inspections and awareness of potential issues that can arise from negligence.
Routine Checks
Routine checks are the first line of defense in maintaining pressure gauges. They allow users to identify any early signs of wear or malfunction before they escalate into larger problems. Here are some essential aspects to consider during routine checks:
- Inspection of the Dial: Ensure that the dial is clear and readable. Any signs of fogging or damage can affect visibility and interpretation of readings.
- Check Connections: Regularly examine the connections between the gauge and the hydroaccumulator. Loose or corroded connections can lead to inaccurate readings.
- Calibrate Periodically: Calibration should be performed at regular intervals as per the manufacturer’s specifications. This ensures that the readings stay accurate.
- Test for Leaks: Inspect for any leaks in the system. A leak can significantly alter the measurements and be unsafe.
Making a checklist for these checks can simplify the process and ensure nothing is overlooked.
Troubleshooting Issues
While routine checks may help prevent some problems, issues can still arise. Here are common troubleshooting steps to address problems with pressure gauges:
- Inaccurate Readings: If readings seem off, start by verifying calibration. If it is out of spec, recalibrate or replace the gauge.
- Gauge Failure: If the gauge fails to register any pressure, check the input line for blockages or leaks. Ensure that the gauge is not malfunctioning due to environmental factors like extreme temperatures.
- Physical Damage: Inspect the gauge for any physical damage. Cracks or severe scratches on the display can compromise its functionality.
- Electronics Check: For digital gauges, a simple battery check may be required. A dead battery can lead to loss of readings.
Proper maintenance and timely troubleshooting can significantly enhance the operational reliability of pressure gauges in hydroaccumulators.
Regular engagement with these practices will not only support the gauge’s performance but also safeguard the overall functioning of the hydroaccumulator system.
Troubleshooting Common Problems
Troubleshooting common problems with pressure gauges is essential for maintaining the functionality and reliability of hydroaccumulators. A pressure gauge that is malfunctioning can lead to serious issues in the system, such as inefficiencies or even catastrophic failures. Understanding the symptoms and solutions for these problems allows users to address and rectify issues promptly, ensuring safety and optimal performance.
Inaccurate Readings
Inaccurate readings are one of the most common problems one might face with pressure gauges in hydroaccumulators. Several factors can cause this issue. One primary element is calibration. Over time and usage, gauges can drift from their original readings, leading to wrong information being displayed. Regular calibration ensures that the gauge remains accurate and reliable.
Another reason could be mechanical wear. If a gauge experiences excessive vibration or shock, its internal mechanisms may become damaged, yielding false readings. Additionally, environmental factors like temperature fluctuations can affect the materials used in the gauge, adding further uncertainty to its accuracy.
To troubleshoot inaccurate readings:
- Check Calibration: Always start by verifying if the gauge is properly calibrated. Test against a known standard if possible.
- Inspect Physically: Examine the gauge for any signs of damage or wear. Look for cracks in the casing or any noticeable signs of deterioration.
- Review Installation: Ensure the gauge is appropriately installed and not subjected to undue stress from the piping.
Addressing these factors can often restore the gauge's accuracy, allowing for precise monitoring of the system's pressure levels.
Gauge Failure
Gauge failure occurs when the pressure gauge stops functioning altogether. This can manifest as a needle that does not move or a digital display that remains blank. Such failure can significantly hinder operations. Thus, recognizing the signs of potential gauge failure is crucial.
A primary cause of gauge failure might be exposure to pressures beyond the gauge's rating. Over-pressurization can damage the internal components irreparably. Similarly, corrosion can lead to failures, especially in gauges used in corrosive environments.
To troubleshoot gauge failure:
- Check Pressure Rating: Ensure that the gauge used is rated for the specific pressures involved. Replace any gauge undersized for the job.
- Examine for Corrosion: Look for rust or corrosion on the gauge or its fittings. If corrosion is observed, replace the gauge and consider preventative measures against exposure to corrosive substances.
- Test Electrical Connections: For digital gauges, malfunction might stem from faulty wiring or connection issues. Verify all electrical connections to ensure they are secure and without damage.
In summary, understanding the troubleshooting process for common problems associated with pressure gauges helps in maintaining their functionality in hydroaccumulators. Quick identification and resolution of issues like inaccurate readings and gauge failure can enhance safety and prolong the life of the equipment.
Epilogue
In this article, we explored the intricate relationship between pressure gauges and hydroaccumulators. Understanding these components is essential for anyone involved in their maintenance or installation. Pressure gauges play a crucial role in ensuring operational safety and efficiency by providing accurate readings of pressure levels. This is key in various scenarios, such as assessing whether a hydroaccumulator is functioning within its optimal range.
Summary of Key Points
- Functionality: Pressure gauges measure the pressure of fluids within hydroaccumulators, directly impacting their performance.
- Types: Different pressure gauges, including mechanical and digital, offer unique advantages based on specific needs and applications.
- Installation: Proper installation is vital to achieving longevity and accuracy, avoiding common mistakes that could lead to failures.
- Maintenance: Regular checks and troubleshooting can ensure that pressure gauges continue to provide reliable readings.
- Troubleshooting: Understanding common problems, like inaccurate readings or gauge failure, can help in timely resolution, preventing larger system issues.
By summarizing these elements, it becomes clear how vital accurate pressure measurements are to the system’s overall performance.
Final Thoughts on Pressure Gauges and Hydroaccumulators
The integration of pressure gauges within hydroaccumulators cannot be overstated. As technologies evolve, the need for precision in measurement and diagnostics grows. DIY enthusiasts, builders, and designers alike must consider the various aspects of these gauges when engaging in projects. Accurate pressure readings impact both safety and efficiency, preventing costly encounters with system failures.