Sealing Threaded Connections: Techniques for Success
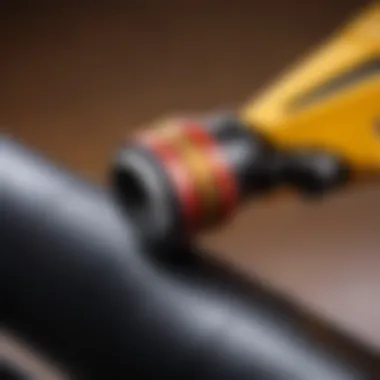
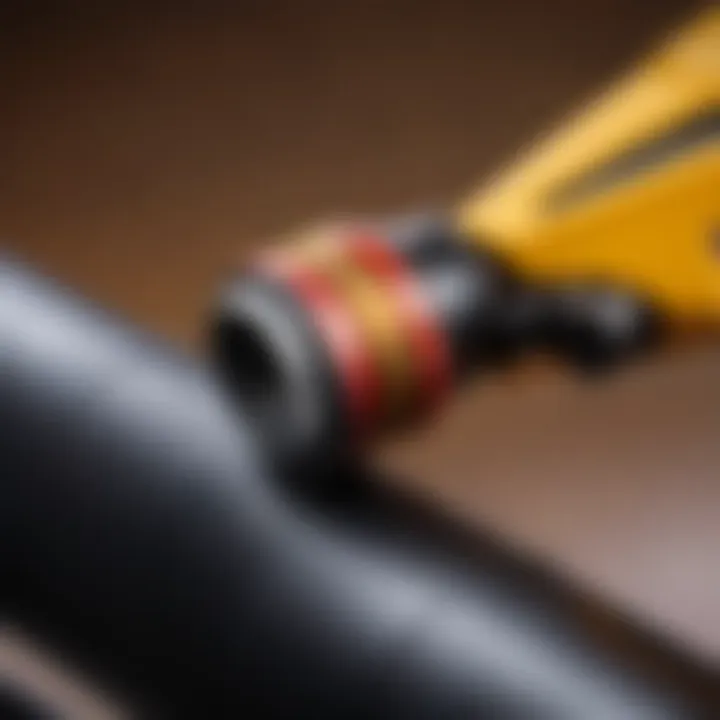
Intro
Sealing threaded connections is a fundamental aspect of DIY projects, impacting both functionality and overall durability. The effectiveness of these seals can significantly influence the longevity of various applications, whether in plumbing, automotive, or construction. Understanding how to proficiently seal these connections involves exploring various materials, techniques, and preparation processes. This article aims to elucidate best practices and techniques for achieving reliable, leak-proof results.
Проектирование и планирование
Effective planning is the cornerstone of a successful sealing project. Before initiating any task, it is vital to carefully consider both the project requirements and the resources at hand.
Как выбрать проект для DIY
Selecting the right DIY project hinges on one's skills, tools, and desired outcomes. Start by evaluating your current capabilities. If you're a novice, opt for simpler tasks that allow you to build confidence. Alternatively, experienced DIY enthusiasts may opt for more complex installations, ensuring a clear understanding of the sealing processes involved.
Once you identify a suitable project, research the necessary sealing methods. Assess how these methods align with the materials and conditions pertinent to your project. For example, for plumbing connections, it may be wise to choose PTFE tape or pipe dope, depending on the specific requirements.
Оценка времени и ресурсов
Time management is essential. Assess how much time you are willing to devote to the project. A rushed job may lead to inadequate sealing, resulting in leaks. Create a timeline, allocating sufficient time for each step, including preparation, application, and curing time if applicable.
Resources, including tools and materials, should be measured against your project scope. Identify what you need to avoid delays. Evaluate whether you should purchase or borrow tools. If order materials online, factor time for delivery into your project timeline.
Выбор материалов
Choosing the right materials for sealing threaded connections is imperative. The material selection process can often dictate the overall success of your project.
Типы материалов для различных проектов
There are various sealing materials available, including
- PTFE tape: Best for plumbing applications due to its chemical resistance.
- Anaerobic sealants: Suitable for metal threads, providing a strong bond.
- Silicone sealants: Effective for flexible connections.
Consider the specific requirements of your project. For example, if it involves chemicals or high pressure, opt for materials designed to withstand such conditions.
Советы по покупке и экономии
When purchasing sealing materials, always compare prices at different retailers. Bulk buying can save money for larger projects. Additionally, consider multi-use products that serve different applications. This reduces waste and saves space.
Check for product reviews online before making a purchase. Inputs from other users can give insight into performance and durability.
"A well-sealed connection can enhance the efficiency of the overall project and minimize future repairs."
In summary, a successful sealing project begins with careful planning and material selection. By understanding the requirements of your project and the functions of various sealing materials, you create a strong foundation for reliable and effective threaded connections.
Understanding Threaded Connections
Threaded connections play a vital role in various industries, including plumbing, construction, and automotive sectors. Understanding these connections is essential for achieving secure assemblies and preventing leaks. This section explores the definition and types of threaded connections, laying the groundwork for effective sealing techniques that will be discussed later.
Definition and Importance
Threaded connections are mechanical junctions formed between two components using spiral grooves, commonly known as threads. These grooves allow for a secure fit when two parts are screwed together, providing stability and strength to the assembly.
The importance of threaded connections lies in their ability to hold components together under tension and shear forces. They are prevalent in numerous applications, from simple DIY projects to complex machinery. A well-designed threaded connection reduces the risk of mechanical failure and leaks, which can lead to costly repairs and safety hazards. Ensuring that these connections are sealed correctly is critical for maintaining integrity and functionality.
Types of Threaded Connections
Understanding the various types of threaded connections helps in selecting the appropriate sealing materials and techniques. Three common types are:
Parallel threads
Parallel threads, characterized by their straight grooves, are widely used in applications where easy disassembly is desired. This type of thread doesn't tighten under load, preventing damage during assembly. The key characteristic of parallel threads is their versatility, often found in applications such as plumbing fittings and mechanical fastenings.
The unique feature of parallel threads is their capability to accommodate a range of sealing methods, including O-rings and compression seals. The advantages of using parallel threads include ease of maintenance and reduced wear on the threads during repeated assembly and disassembly. However, they may not provide the same level of sealing effectiveness as tapered threads.
Tapered threads
Tapered threads are designed with an angle that allows the thread diameter to decrease towards the end, creating a wedging action as the connection is tightened. This specific aspect enhances the sealing capability, making tapered threads a popular choice for high-pressure applications like gas and water pipelines. The key characteristic of tapered threads is their ability to achieve a tight seal simply by tightening the connection without the need for additional sealing materials.
A unique advantage of tapered threads is their self-sealing property, but this can also lead to difficulty in disassembly if over-tightened. Careful installation is essential to balance the benefits and potential disadvantages.
Specialized threads
Specialized threads include various thread designs catered for specific application needs, such as pipe threads, acme threads, and buttress threads. Each type serves a unique function and provides distinct advantages, catering to specific industry requirements. The key characteristic of specialized threads is their customization, allowing engineers to select the ideal thread for precise applications.
The unique feature of these threads often lies in their enhanced performance capabilities, such as greater load carrying or unique sealing configurations. However, they may require specialized tools or methods for application and removal, which could be seen as a disadvantage in certain circumstances.
"Choosing the appropriate type of threaded connection is integral to ensuring the overall reliability of the assembly."
In summary, an understanding of threaded connections, their definition, and the types available sets the foundation for selecting the right sealing methods. This knowledge leads to better decision-making when it comes to preventing leakage and ensuring the longevity of projects.
Common Issues with Threaded Connections
Understanding the common issues associated with threaded connections is crucial for ensuring their effectiveness. Threaded connections form the backbone of many assemblies in plumbing, construction, and mechanical applications. Failure to address problems can lead to leaks, structural failures, and costly repairs. This section highlights the primary issues that can affect the integrity of these connections, providing insights into their causes and implications.
Leakage Problems
Leakage problems are among the most prevalent issues with threaded connections. These leaks can occur due to a variety of factors, such as improper sealing materials, incorrect installation, or wear and tear over time. When a leak develops, it can lead to significant consequences including water damage, loss of fluids in hydraulic systems, or the escape of gases in pressurized situations. Therefore, seeking the right materials and applying them correctly is essential.
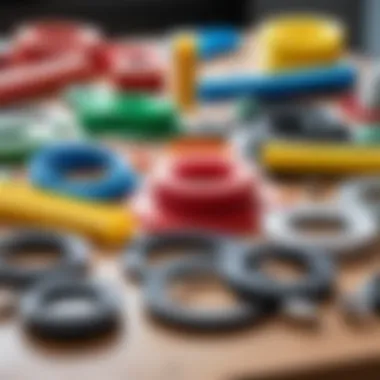
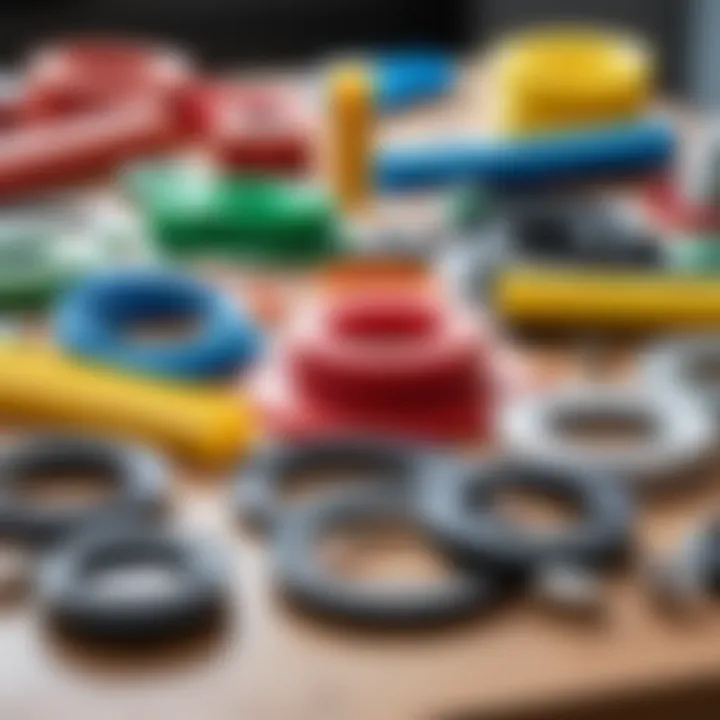
Common causes of leakage include:
- Incompatible sealing materials
- Insufficient tightening of the connection
- Wear on the threads over time
To prevent leakage, it is vital to inspect the sealing materials regularly. Using appropriate thread sealants can enhance the overall tightness of the connection.
Corrosion and Wear
Corrosion and wear can also significantly impact threaded connections. These two processes can compromise the structural integrity of the threads, leading to issues such as increased friction or, in severe cases, complete failure of the connection. Threaded materials exposed to harsh environmental conditions or corrosive substances are particularly at risk.
Factors contributing to corrosion and wear include:
- The use of dissimilar metals
- Unprotected exposure to moisture or chemicals
- Mechanical stress during operation
To mitigate corrosion, selecting compatible materials for connections is essential. Regular maintenance checks can help identify early signs of wear or corrosion, allowing for timely interventions.
Thread Damage
Thread damage is another common issue that can arise in threaded connections. Damage can occur during installation or over time due to external stresses. Stripped or cross-threaded connections can lead to significant problems, such as leakage or total joint failure.
Common forms of thread damage include:
- Stripped threads due to excessive force
- Cross-threading from improper alignment during assembly
- Surface imperfections caused by debris or contamination
To avoid thread damage, it is crucial to follow proper installation procedures. Using the correct tools and ensuring careful handling can greatly reduce the risk of damaging threads during assembly.
Materials for Sealing Threaded Connections
Understanding the different materials used for sealing threaded connections is crucial for achieving a reliable and leak-free setup. Each material serves distinct purposes, has unique properties, and is suited for specific applications. Selecting the appropriate sealing material not only enhances the longevity and performance of the connection but also reduces maintenance costs in the long run. Careful consideration should be given to the compatibility of these materials with the substances being sealed, as well as environmental factors such as temperature and pressure. Here, we will explore four key materials commonly used in sealing threaded connections, highlighting their unique benefits and practical considerations.
Teflon Tape
Teflon tape, often known as PTFE tape, is a widely used sealing material in plumbing and piping applications. It is a thin, pliable tape that is resistant to chemical reactions, making it suitable for various fluids, including water, oil, and gas. Its primary function is to fill the gaps between threaded connections, forming a tight seal when the components are joined.
Benefits of Teflon tape include:
- Ease of Use: It is simple to apply and does not require special tools.
- Chemical Resistance: It withstands a wide range of chemicals, providing versatility in usage.
- Reduced Friction: It helps to prevent thread damage by minimizing friction during assembly.
However, it is essential to avoid over-wrapping Teflon tape, as excess tape can lead to difficulty in tightening the connection.
Pipe Joint Compound
Pipe joint compound, commonly referred to as pipe dope, is a thick paste used to seal threaded joints. It helps to fill gaps and can enhance the sealing effect of the joint. This material is particularly useful for metal-to-metal connections and is often used in plumbing applications.
Benefits of pipe joint compound include:
- Versatility: Suitable for a range of piping materials, including PVC, steel, and copper.
- Improved Seal Integrity: It can provide a stronger seal than Teflon tape in some applications.
- Temperature Tolerance: Many compounds are designed to withstand high temperatures and pressures.
Nonetheless, it may take longer to cure than Teflon tape, requiring patience for the best results.
Anaerobic Sealants
Anaerobic sealants are specially formulated adhesives designed for sealing and locking threaded metal connections. They cure in the absence of oxygen, providing a robust and durable seal. This technology is widely used in industrial applications, especially where high-pressure resistance is necessary.
Advantages of anaerobic sealants are:
- Strong Bonding: They offer exceptional adhesion, making them ideal for critical applications.
- Leak Prevention: They effectively seal gaps, preventing leaks in both static and dynamic connections.
- Vibration Resistance: Their properties help maintain integrity even in vibrating environments.
It is important to note that once applied, anaerobic sealants often require specific conditions for curing, thus ensuring proper application is necessary for effective results.
O-Rings and Gaskets
O-rings and gaskets provide mechanical seals, preventing fluid leakage between surfaces. O-rings are circular seals that fit into grooves, while gaskets are flat pieces typically used between two flat surfaces. These materials are often used in hydraulic and pneumatic applications and offer reliability in sealing.
Pros of using O-rings and gaskets include:
- Customization: Available in various materials and sizes to meet specific application requirements.
- Temperature Range: They can endure diverse temperature ranges depending on the material.
- Accessibility: Generally easy to replace, allowing for straightforward maintenance.
However, proper selection of the material (e.g., rubber, silicone, or fluoropolymer) is essential to align with the working environment.
Proper selection of sealing materials based on the specific application is vital to achieve reliable, leak-free connections.
Choosing the Right Sealing Material
Selecting the proper sealing material is crucial when sealing threaded connections. Not all materials work equally well with every type of connection. Hence, understanding the compatibility and performance characteristics of different sealing options is key to ensure both durability and effectiveness.
The right material not only enhances the sealing integrity but also addresses specific project requirements. By taking into account the physical and chemical properties of the materials, one can successfully avoid issues such as leaks, corrosion, and premature wear. In essence, the proper selection can lead to long-lasting, reliable seals.
Compatibility with Threaded Materials
Compatibility with the base materials is the first element to consider. Each threaded connection, whether composed of metal or plastic, demands a sealing solution that can accommodate its specific characteristics. For instance, Teflon tape is suitable for most threaded plastic pipes but can be inappropriate for certain metals. Understanding the base material prevents chemical reactions leading to seal failure.
It is also important to match the thread type to the sealing approach. For parallel threads, Teflon tape or pipe joint compound can be effective. In contrast, tapered threads benefit from anaerobic sealants, which cure in the absence of air. Selecting the right sealant based on material compatibility can greatly reduce failure rates.
- Some common sealing materials include:
- Teflon Tape
- Pipe Joint Compound
- Anaerobic Sealants
- O-Rings and Gaskets

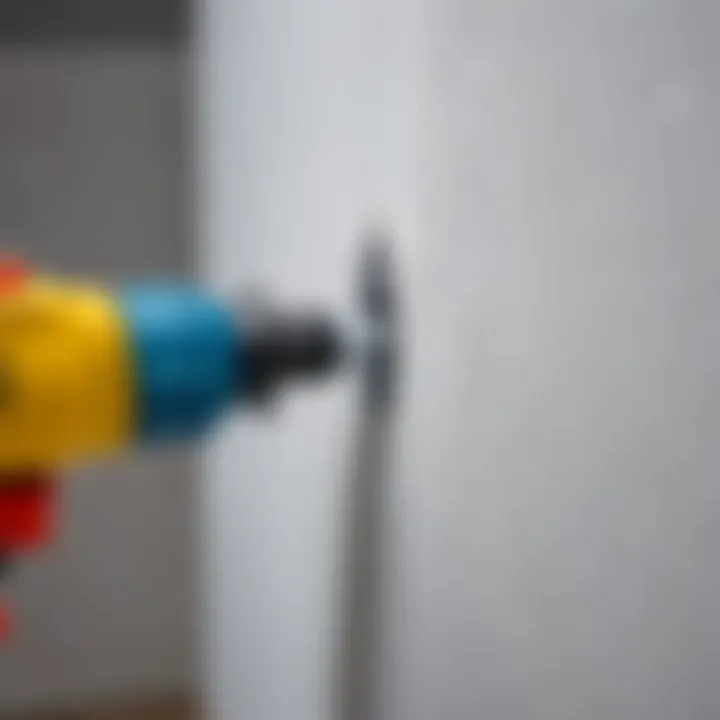
Temperature and Pressure Considerations
Temperature and pressure conditions where the threaded connection operates must be addressed. Both factors influence a sealing material's performance. A material that works well at normal temperature may fail under high thermal or pressure conditions.
For example, anaerobic sealants are known for their excellent performance in higher pressures but may degrade at high temperatures. Conversely, Teflon tape can accommodate a wide range of temperatures but may not withstand high pressures effectively. Therefore, always check the specifications provided by the manufacturer.
Proper sealing material selection protects essential connections from stress and strain, ensuring needed reliability.
Preparation for Sealing
Proper preparation for sealing threaded connections is an essential step in ensuring reliability and durability. This phase significantly influences the performance of the seal and can help prevent issues such as leaks or material degradation. Ignoring this stage could lead to suboptimal seals, resulting in costly repairs or even system failures in some cases. Therefore, its importance cannot be overstated.
Being thorough in preparation includes several critical elements. The first is cleaning the threads. This step removes dirt, grime, and old sealing materials that could interfere with the new sealant. A clean surface is crucial for creating a proper bond between the sealing material and the threaded surfaces.
The second element is inspecting for any visible damage on the threads. Undetected nicks or wear can compromise the integrity of the connection and lead to leakage or increased wear on both the sealing material and the threads themselves. Addressing such issues beforehand ensures a longer lifespan for the connection and its sealed components.
Both cleaning and inspecting not only improve the sealing effectiveness but also provide insights into the overall condition of the connection. This initial groundwork paves the way for the succeeding sealing techniques, making it a vital part of the sealing process.
Cleaning the Threads
Cleaning the threads is a straightforward but vital task that should not be neglected. The presence of contaminants like dust, oil, or old sealants can hinder proper sealing. Begin by using appropriate cleaning agents, depending on the material of the threaded connection. Commonly, isopropyl alcohol or acetone can be effective for metal threads, while plastic threads might require gentler options. Make sure to apply the cleaning agent thoroughly, ensuring all thread sections are treated.
After applying the cleaner, a cloth or brush can be used to scrub the threads gently. This action will remove debris and old sealant residues that could impact the new sealant. Once done, rinse with a clean solvent to remove any cleaning agent residues and let them dry completely. It’s crucial to ensure the threads are dry before applying any sealing material, as moisture can compromise the performance of sealants.
Inspecting for Damage
Inspecting threaded connections for damage is an important task often overlooked. This step is crucial, as any irregularities could lead to failures down the line. When checking for damage, look for signs of wear, such as uneven threads, nicks, or cracks. These defects can create spaces for leaks, leading to inefficiencies and potential hazards.
If you find any significant damage, it's advisable to replace the damaged components before proceeding with sealing. Minor wear can sometimes be repaired, but it’s important to weigh the cost and time of such repairs against potential risks.
In summary, both cleaning and inspecting the threads are foundational practices in preparing for sealing threaded connections. They ensure that the connection surface is optimal for sealing, significantly enhancing the effectiveness and longevity of the seal.
Application Techniques for Sealing
The application techniques for sealing are critical in ensuring the effectiveness of threaded connections. Proper application not only maximizes the sealing potential of the chosen material but also extends the lifespan of the connection. Knowledge of different sealing methods allows for informed decision-making, enhancing reliability and performance. Each sealing technique has its own characteristics, advantages, and specific situations where it excels. Understanding these nuances helps prevent potential issues down the road, ensuring a leak-free connection that meets the requirements of the project.
Using Teflon Tape
Teflon tape, or polytetrafluoroethylene tape, is a popular choice for sealing threaded connections. Its unique properties make it suitable for various applications, particularly involving plumbing and gas fittings. The tape creates a smooth surface that facilitates the easy tightening of threads. Moreover, Teflon tape helps resist moisture and chemical infiltration, significantly reducing the risk of leaks.
When applying Teflon tape, follow these simple steps:
- Identify the direction of the thread; wrap the tape around the male threads in the same direction.
- Begin wrapping at the base and go upwards, overlapping slightly with each turn.
- Apply 2 to 3 wraps for optimal sealing, depending on the thread profile.
- Ensure the tape is flat and smooth, avoiding wrinkles that could impede the seal.
Proper application of Teflon tape ensures efficient sealing and prevents leakage in threaded connections.
Applying Pipe Joint Compound
Pipe joint compound, also known as pipe dope, offers another reliable sealing option. This viscous material fills gaps between threads while providing a solid seal. The compound is versatile and can be used with various materials, including metal and plastic. Its application is straightforward but requires careful attention to detail.
To apply pipe joint compound, consider these key points:
- Clean the threads to remove any old material or debris before application.
- Apply a thin layer of compound to the male threads, ensuring complete coverage.
- Avoid over-applying, as excess compound can run into the system, compromising functionality.
- Tighten the connection according to the manufacturer's specifications to achieve the best seal.
Additionally, always check compatibility between the compound and the materials being joined.
Using Anaerobic Sealants
Anaerobic sealants are advanced materials designed for sealing threaded connections in environments where air is absent. Once applied, these sealants cure, forming a strong bond that prevents leakage. They are particularly favored in industrial settings, automotive applications, and anywhere high-performance sealing is crucial.
When employing anaerobic sealants, utilize the following guidelines:
- Clean the threaded surfaces thoroughly to remove oil or dirt.
- Apply a small amount of sealant to the male threads, ensuring even coverage.
- Assemble the joint while the sealant is still wet, allowing it to fill any gaps as the threads engage.
- Tighten the connection and allow sufficient curing time based on the product instructions.
Anaerobic sealants can also provide resistance to vibration, making them ideal for high-pressure situations.
Understanding how to effectively apply each sealing technique is essential for achieving optimal results in sealing threaded connections. Proper techniques, combined with suitable materials, lead to dependable and long-lasting seals.
Testing Sealed Connections
Testing sealed connections is an essential step that ensures the effectiveness of sealing methods used in threaded connections. A proper and reliable seal is not just about applying materials; it is critical to verify that these materials have formed an airtight and watertight bond. Neglecting this step can result in leaks, which can lead to significant damage over time as well as increased maintenance costs.
In this article, we will discuss two primary testing methods: visual inspection and pressure testing. Each method serves its unique purpose in determining the integrity of the joint. Being diligent in testing sealed connections enhances safety and reliability, especially in applications involving critical systems where failure could result in accidents or equipment damage.
Visual Inspection
Visual inspection is the first step in assessing the integrity of a sealed connection. It involves examining the joint surface for signs of improper sealing, such as gaps, misalignment, or excess sealing material. This initial assessment can identify obvious defects that may compromise the seal's effectiveness.
When conducting a visual inspection, consider the following points:
- Alignment: Ensure that the threads are properly aligned. Misalignment can create uneven pressure, leading to leaks.
- Surface Condition: Look for signs of corrosion, pitting, or contamination on the threads and sealing surfaces.
- Excess Sealant: Too much sealing material can be a sign of improper application, which may hinder the sealing process and lead to failure.
- Debris Presence: Check for dirt or debris that might prevent a proper seal.
A thorough visual inspection can save time and money by highlighting issues before they escalate. It allows for early intervention, which is key in maintaining system reliability and performance.
Pressure Testing
Pressure testing is another pivotal method to verify the effectiveness of sealed connections. This process involves subjecting the sealed joint to pressure and then monitoring it for leaks. Pressure testing can be performed in various systems, such as plumbing, gas lines, and hydraulic systems, making it a versatile tool in many fields.
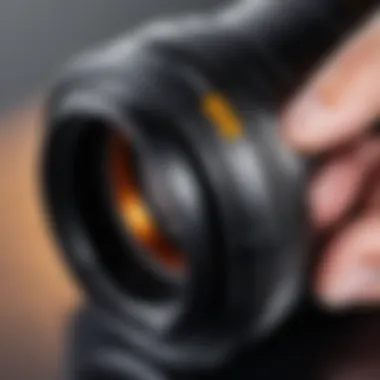
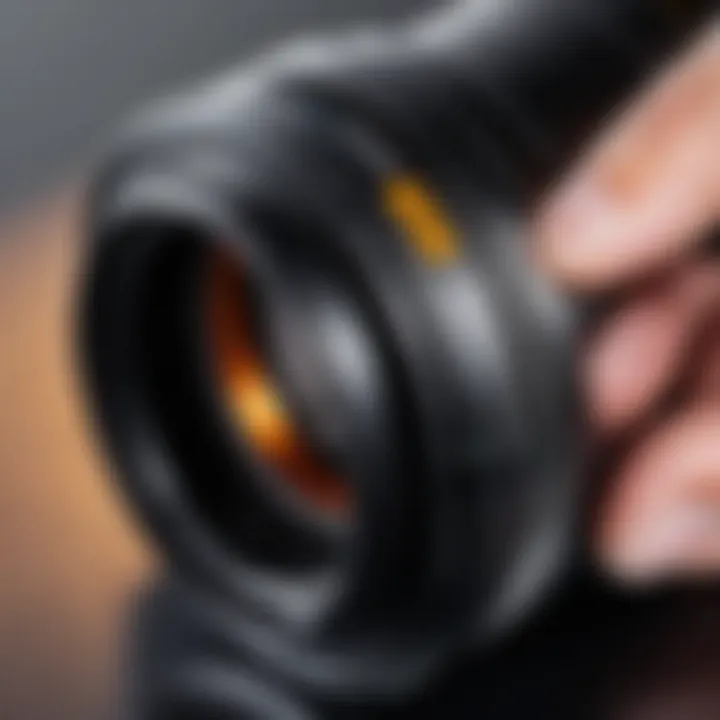
There are several considerations for effective pressure testing:
- Choose the Right Pressure: Apply a pressure that is appropriate for the system’s specifications to avoid damaging the seals.
- Monitor the System: Use pressure gauges to monitor the pressure continuously. A sudden drop in pressure may indicate a leak.
- Duration of the Test: Maintain pressure for a specified duration to ensure that any potential leaks can be identified.
- Leak Detection: Employ soapy water or other leak detection solutions around the joint to visually identify leaks. Bubbles forming at the joint are a clear indicator of failure.
Conducting pressure tests also gives insights into the overall system integrity, as it evaluates not just the seal but the performance of the entire connection under operational conditions.
"Effective testing not only prevents failures but also ensures that your sealing techniques are reliable."
Maintenance of Sealed Connections
Maintaining sealed connections is crucial for the longevity and effectiveness of any assembly involving threaded joints. Over time, environmental conditions, mechanical stress, and other factors can compromise the integrity of seals. Regular maintenance ensures that any potential issues are identified and addressed before they escalate into significant problems. Furthermore, maintaining sealed connections can prevent leakage, corrosion, and failure, which could lead to costly repairs and unsafe conditions.
Regular Inspections
Conducting regular inspections of sealed connections is the first step in effective maintenance. This should be done periodically based on usage, environmental exposure, and the nature of the application itself. Inspections allow one to spot early signs of wear, damage, or improper sealing. It is advisable to check areas with exposure to fluids or temperature changes more frequently.
During an inspection, look for any visible signs of leakage or wear on the sealing material. Additionally, inspect the threads on bolts or fittings for stripping or deformation. Engaging in these regular visual checks can help in maintaining the overall health of the connection.
Addressing Warning Signs
Leaks
Leaks are often the most immediate concern when it comes to sealed connections. They can signify issues in the sealing method or the material used. The presence of a leak can lead to fluid loss, not only causing operational issues but also creating safety hazards. It is essential to identify the exact point of leakage.
One key characteristic of leaks is their unpredictable nature; they may develop suddenly or gradually worsen over time. Addressing leaks promptly can prevent further damage and continuity issues in systems. The unique feature of leaks is the broad range of factors that can cause them, such as temperature fluctuations or material degradation.
Corrosion
Corrosion poses a serious threat to sealed connections. Chemicals, moisture, and environmental conditions can lead to the deterioration of both sealing materials and the metals involved in the connection. Corrosion can significantly compromise the integrity of the seal, leading to leaks and failure.
A key characteristic of corrosion is its gradual nature; it may take time to detect its onset, but its effects can be severe. Identifying corrosion early can help to mitigate its impact. Corrosion often requires the replacement of sealing materials or even components of the threaded connections.
Troubleshooting Common Sealing Issues
Sealing threaded connections effectively is crucial in various applications, from plumbing to mechanical assembly. However, even the most diligent preparations and applications can lead to issues down the line. Understanding how to troubleshoot these common sealing problems not only helps in maintaining the integrity of the connections but also enhances the overall reliability of the projects. This section aims to detail the importance of identifying and addressing sealing issues, ensuring long-lasting performance of your work.
Identifying Causes of Leakage
Leakage can stem from several different causes. The first step in troubleshooting is to ascertain the root of the problem. A few significant factors that lead to leaks include:
- Incompatibility of sealing materials: Sometimes the chosen sealing material does not bond well with the threaded surfaces.
- Improper application: Not applying the sealant correctly can result in gaps or unevenness that leads to leaks.
- Over-tightening or under-tightening: Both scenarios can jeopardize the effectiveness of the seal.
- Thread damage: Worn or corroded threads can create spaces that allow liquids or gases to escape.
To diagnose these issues, consider conducting thorough visual inspections. Examine the area for signs of leakage, paying attention to any pooling of liquid or gas residue. Sometimes, conducting a pressure test may help to reveal minute leaks.
Repairing Damaged Threads
If damage to the threads has been identified, repair is essential to restore functionality. Depending on the extent of the damage, there are several methods available:
- Thread Repair Kits: These kits often include helicoil inserts which can restore stripped threads to their original condition. Installing these inserts usually involves drilling out the damaged threads and inserting the new ones.
- Thread Taps: If the threads are slightly damaged but not completely stripped, using a thread tap can help to re-establish the threading.
- Adhesive Sealants: In some cases, if physical repair is not feasible, using a strong adhesive sealant can assist in mitigating leaks temporarily.
When repairing threads, it’s important to choose the right method based on the specific type of damage. Evaluate the condition of your threaded connection and decide whether a more temporary fix or a permanent solution is necessary.
"Effective troubleshooting ensures the longevity and reliability of threaded connections."
By mastering these troubleshooting skills, you not only enhance your DIY abilities but also gain confidence in managing complex projects. Addressing these common issues promptly will ensure that your sealing practices remain effective and efficient.
Future Trends in Sealing Technology
In the world of sealing threaded connections, advancements are ongoing. The future of sealing technology promises increased reliability and efficiency. These developments are crucial for industries where precision and safety are paramount. As technology evolves, new materials and methods are reshaping how we approach sealing.
Innovations in Sealing Materials
The landscape of sealing materials is changing rapidly. Traditional materials like Teflon and pipe joint compounds are being complemented by innovative options. Newer sealants made from advanced polymers exhibit better resistance to chemicals and extreme temperatures. These innovations enhance the durability and effectiveness of seals in various applications. Furthermore, bio-based sealants are emerging, offering an environmentally friendly choice. The trend towards sustainability is also influencing material selection. As manufacturers focus on reducing environmental impact, bio-based materials become more prevalent.
- Benefits of innovative sealing materials:
- Enhanced resistance to extreme conditions.
- Improved longevity and performance.
- Environmentally friendly options.
Advancements in Application Techniques
As new materials enter the market, application techniques must also advance. Enhanced application methods can improve the effectiveness and ease of sealing threaded connections. Automated systems are becoming more common in industrial settings, providing accurate and consistent application of sealants. Moreover, training and educational resources are improving. This development helps DIY enthusiasts and professionals utilize modern sealing techniques effectively.
"The right application technique can make the difference between a reliable seal and a failure."
Efficiency is now a focus in application processes. Techniques that require less time and reduce the margin for error are in demand. Moreover, methods such as spray-on sealants have gained traction, allowing for quick and uniform coverage on complex geometries. The push for precision and reliability is driving these advancements.
Adopting the latest sealing materials and application techniques is essential. It not only addresses current challenges but also prepares users for future demands in sealing technology. By staying informed of these trends, those involved in sealing threaded connections will maintain a competitive edge.
Ending
The conclusion serves as a crucial part of this article, synthesizing the main insights and emphasizing the overarching themes in sealing threaded connections. Understanding the best practices and techniques discussed greatly enhances one’s competency in this area. First, the significance of selecting the right sealing materials cannot be overstated. The durability and effectiveness of the seal depend heavily on compatibility with the threaded materials, temperature, and pressure conditions.
Secondly, preparation plays a pivotal role in ensuring successful sealing outcomes. Clean and undamaged threads form the foundation for a reliable seal. The maintenance procedures discussed earlier further highlight the necessity for regular inspections. This diligence prevents minor issues from escalating into significant problems.
Finally, knowing how to troubleshoot, from identifying causes of leakage to repairing damaged threads, empowers individuals in handling common issues with confidence. In summary, this conclusion ties together the extensive knowledge provided throughout the article, reinforcing the importance of a methodical approach in sealing threaded connections while encouraging readers to utilize these insights in their practical endeavors.
Summary of Key Points
- Importance of Material Selection: Choosing correct sealing materials is vital for a sustainable and effective connection.
- Preparation is Key: Cleaning and inspecting threads before sealing ensures better outcomes.
- Regular Maintenance: Ongoing inspections are essential to maintaining the integrity of sealed connections.
- Troubleshooting Knowledge: Understanding common sealing issues equips users to address problems promptly.
Final Thoughts on Sealing Practices
In reflection, mastering sealing practices for threaded connections is not merely a technical skill, but an essential component for those engaged in renovations, interior design, and construction. As systems and requirements evolve, staying informed on innovations in sealing materials and application techniques allows professionals to uphold the highest standards in their work. Emphasizing a proactive approach to maintenance can extend the life of threaded connections while ensuring their effectiveness. Thus, whether one is a novice or an expert, committing to the best practices in sealing is invaluable for achieving reliable, leak-proof results.