Selecting the Right 220V Welding Machine for Home Use
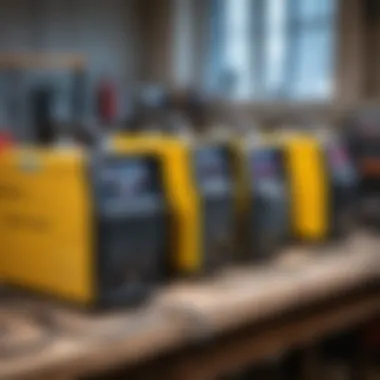
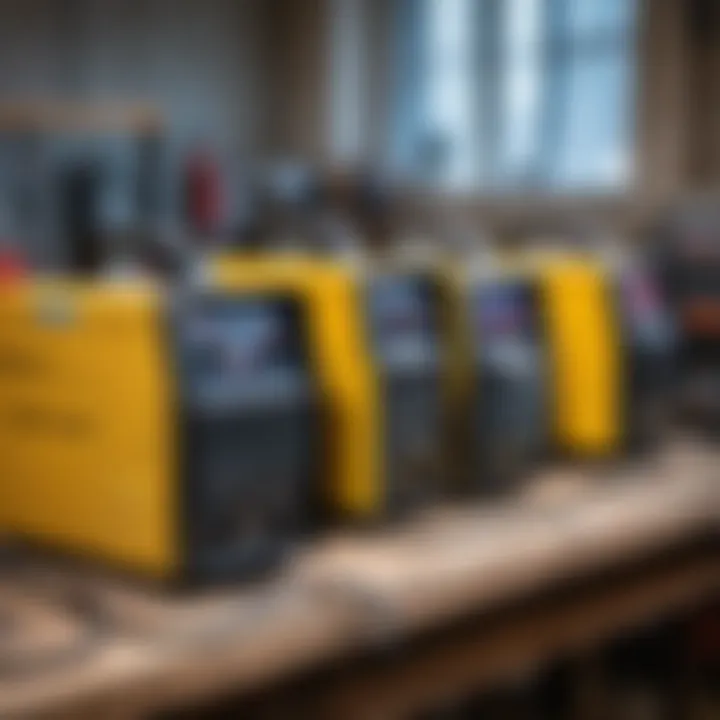
Intro
Selecting the right welding machine for home and garden projects is more than just picking a device. It involves understanding your specific needs, the types of welding processes available, and the safety measures you must take. With a 220V supply, you open a world of options suitable for various DIY tasks, from simple metal repairs to intricate outdoor creations.
Before diving into the details, it is crucial to recognize the increasing significance of welding skills in do-it-yourself culture. Knowing how to weld not only enhances your capabilities but also offers a means to repurpose materials effectively. This guide will provide a comprehensive look at the essential considerations for choosing an appropriate welding machine, tailored to both novice and experienced enthusiasts.
Проектирование и планирование
Как выбрать проект для DIY
Choosing a project is often the first step in your welding journey. It's vital to select a project that aligns with your skills and the capabilities of the welding machine. Consider starting with simple items, like garden furniture or railings, before attempting more complex projects.
Identify projects that require minimal materials and tools to begin with. This will allow you to focus on mastering techniques without overwhelming yourself. Collect ideas from various sources such as social media platforms like Instagram or Facebook, and forums on Reddit, where other enthusiasts share their experiences and designs.
Оценка времени и ресурсов
After you have an idea of what project to tackle, evaluating the time and resources becomes essential. Assess the availability of materials and tools needed for your specific project. Create a timeline that includes research, preparation, construction, and finishing phases. This structured plan will help you stay organized and ensure that you allocate enough time for each step.
Also, consider the costs involved. A clear budget can help manage expenses and avoid overspending. Whether you opt for high-quality steel or more affordable alternatives can greatly affect both the final outcome and your budget.
Выбор материалов
Типы материалов для различных проектов
Materials play a critical role in the success of your welding projects. Common materials include aluminum, stainless steel, and mild steel. Each has unique properties and is suited for different applications.
- Mild Steel: Easy to work with and weld; ideal for structural projects and furniture.
- Stainless Steel: Offers great corrosion resistance; excellent for outdoor projects.
- Aluminum: Lightweight and versatile but can be challenging to weld without proper technique and equipment.
Understanding the material properties ensures that you select the right one for your intended project, enhancing durability and effectiveness.
Советы по покупке и экономии
When purchasing materials, consider sourcing from local suppliers or recycling centers. This not only aids in reducing costs but also supports sustainability. Always check for deals or discounts at hardware stores or take advantage of online platforms. Utilizing resources effectively will ensure that you stay within your budget while achieving quality results.
It's wise to keep an eye on materials that are on sale and to build connections with local suppliers; they can provide valuable insights and might offer bulk discounts.
By thoroughly understanding the planning process and material selection, you're better equipped to make informed decisions about your welding projects. This knowledge will undoubtedly enhance your effectiveness and enjoyment of welding.
Understanding Welding Machines
Selecting the right welding machine requires a solid understanding of welding machines themselves. The proper machine can significantly impact the quality, efficiency, and safety of your projects. It’s essential to recognize specific elements at play, such as welding processes, machine capabilities, and the applications relevant to home and garden use. By understanding these features, you can make a more informed decision that aligns with your needs, whether you are a beginner or have prior experience.
What is a Welding Machine?
A welding machine is a device used to join materials, typically metals, through various techniques that involve heat. Welding machines come in different forms, such as MIG, TIG, Stick, and Flux-Cored, each suited for various applications. Their primary purpose is to create a strong bond between two materials, which is essential for construction, repairs, and artistic endeavors in metalworking. Knowing what constitutes a welding machine is a crucial first step when selecting equipment for domestic use.
Types of Welding Processes
Understanding different welding processes is vital because each method has unique advantages and applications.
MIG Welding
MIG (Metal Inert Gas) welding is often favored for its ease of use. This method uses a continuous wire feed to create a strong weld. One key characteristic of MIG welding is its versatility; it works well with thin and thick materials alike. This makes it a popular choice for both beginners and experienced welders engaged in home projects. However, it generally requires a stable power source and can be less effective in windy conditions due to its reliance on shielding gases.
- Advantages:
- Disadvantages:
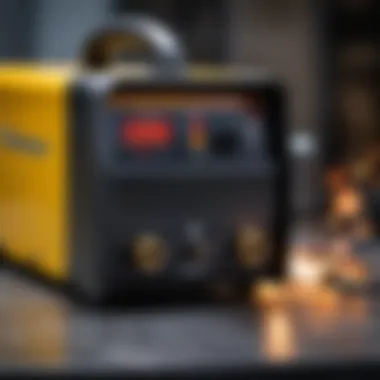
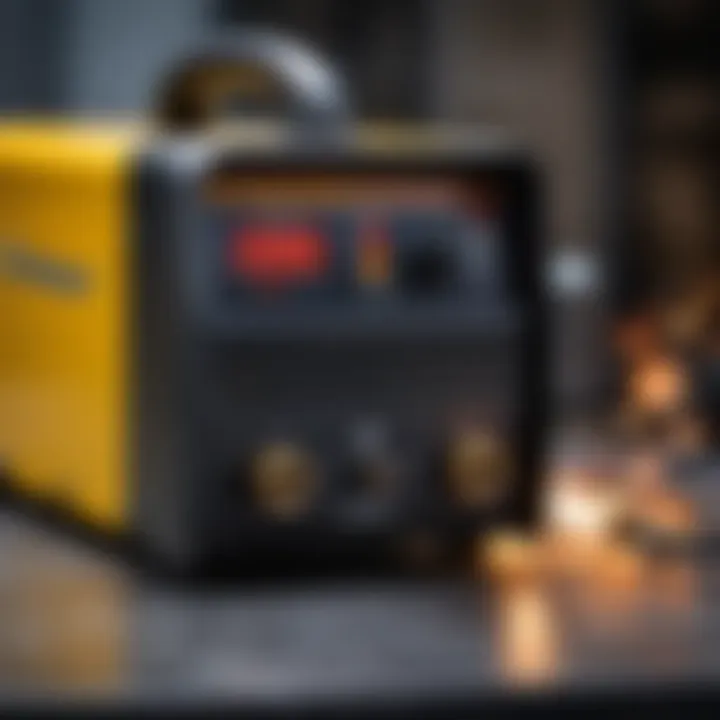
- Faster welding compared to other methods
- Less post-weld cleanup needed
- Requires gas supply
- Often unsuitable for outdoor use due to wind sensitivity
TIG Welding
TIG (Tungsten Inert Gas) welding is known for its precision. It uses a non-consumable tungsten electrode to produce the weld, making it ideal for thin materials like aluminum and stainless steel. TIG welding allows for a cleaner, high-quality finish. While it offers control, the learning curve can be steeper than MIG.
- Advantages:
- Disadvantages:
- Superior control for thin materials
- Produces high-quality welds
- Slower process, requiring more skill
- More equipment needed (like foot pedals)
Stick Welding
Stick welding, or Shielded Metal Arc Welding (SMAW), is a straightforward and robust process. It uses a consumable electrode that melts to create the weld. This type of welding can be done outdoors successfully, making it a great option for home and garden projects. It is also less sensitive to contaminants and works well with dirty materials.
- Advantages:
- Disadvantages:
- Portable and versatile
- Effective on rusty or dirty materials
- Produces more slag requiring extra cleanup
- May not provide the finest finish
Flux-Cored Welding
Flux-Cored welding is an alternative to TIG and MIG. It uses a tubular wire filled with flux, which protects the weld pool and produces slag. This method is particularly suited for thicker materials and is effective for outdoor work since it is less affected by wind. While it shares some similarities with MIG, it does not require a shielding gas, making it more convenient for home users.
- Advantages:
- Disadvantages:
- Excellent penetration in thick materials
- No external gas needed
- Produces more smoke and spatter
- Can lead to less clean welds
Understanding these processes and their characteristics allows potential users to select the most appropriate welding machine based on their specific needs and project requirements.
Electricity Considerations
Understanding the electricity requirements for welding machines is crucial for any home or garden project. Welding machines operate on specific power levels, and ensuring compatibility with your home's electrical setup is the first step to achieving successful and safe welding results. Without a clear grasp of electrical considerations, users may face disruptions or even damage to their equipment.
Understanding 220V Supply
A 220V supply is commonly utilized for various high-powered appliances and tools. It provides a more stable and efficient source of energy compared to lower voltage systems such as the standard 110V. When welding with a machine that operates on 220V, users gain the advantage of enhanced power output and faster welding speeds. This is especially beneficial for heavy tasks often found in construction and metalworking.
A few key points about the 220V supply include:
- Increased Efficiency: Machines running on 220V tend to operate more efficiently, leading to less energy waste.
- Suitable for Heavy-Duty Tasks: This voltage enables welding tasks that require significant power, such as welding thicker metals.
- Fewer Circuit Overloads: Using 220V can help in reducing the risk of circuit overloads compared to 110V setups, which can be limiting for demanding machinery.
However, it’s vital to ensure that the local electrical infrastructure can handle this voltage safely.
Connection and Compatibility
Connecting a welding machine to a 220V supply involves careful consideration to ensure compatibility. Not all outlets are designed for such high voltage, and using the wrong setup can lead to poor performance or even equipment failure. When checking for compatibility, consider the following:
- Socket Type: Different regions may have specific types of 220V outlets. Ensure your welding machine's plug fits the socket available in your home. Adapters may be necessary.
- Wiring: The wiring in your home should be able to support the amperage required by the welding machine. Using insufficient wiring can create safety hazards, including electrical fires.
- Circuit Breakers: Ensure that your circuit breakers are appropriate for the amperage draw of the welding machine. A dedicated circuit is often recommended to manage the load.
To summarize, carefully assess your home’s electrical setup when planning to use a 220V welding machine. Not only does this ensure optimal performance, but it also reinforces safety measures vital for any welding operation.
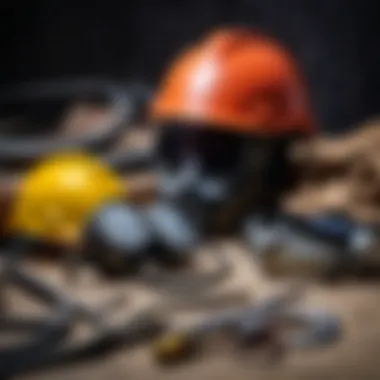
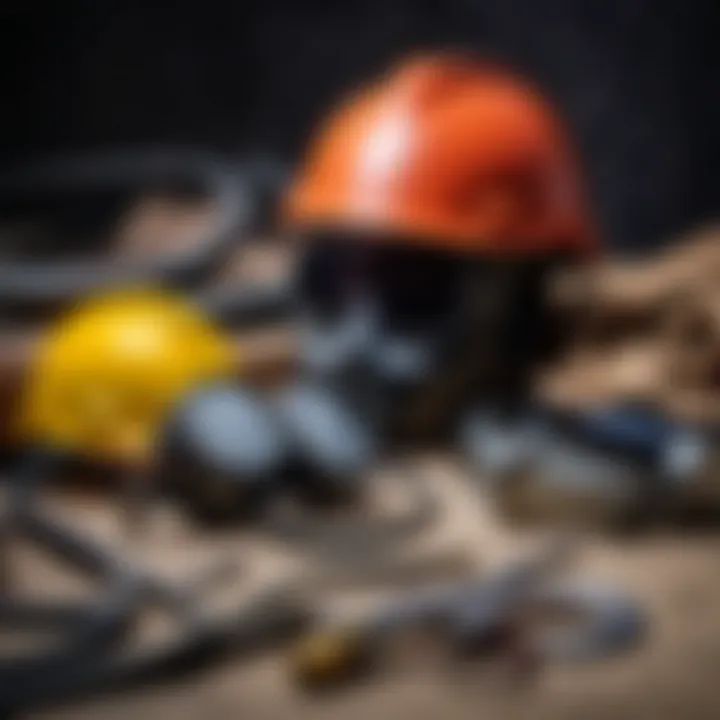
Choosing the Right Welding Machine
Choosing the right welding machine is crucial for anyone looking to undertake projects in home or garden settings, particularly when limited to a 220V power supply. The decision impacts not just the quality of the work, but also the safety and efficiency of the process. Selecting a well-suited welding machine ensures that you can tackle various tasks competently, be it for repairs, fabrication, or creative projects. With diverse types available, understanding your specific needs will guide you to the most suitable option.
Assessing Your Needs
An initial step in selecting a welding machine is to assess your actual needs. This means determining the kind of projects you will be tackling and the materials involved. If you are primarily working with thin metal sheets or doing light fabrication, a MIG welder may be more advantageous. Alternatively, if your work involves heavier materials like steel, a TIG or Stick welder may be necessary. Furthermore, evaluate the frequency of use. Are you a hobbyist doing occasional work, or do you plan to weld regularly? Your commitment level greatly informs the machine’s specifications and durability.
Key Features to Look For
Power Output
The power output of a welding machine is a defining aspect of its performance. A robust power output determines how effectively the machine can handle different thicknesses of material. Machines with higher wattage can often work on thicker materials and may provide more consistent welds. A notable characteristic of power output is the ability to adjust settings based on your project. This flexibility can contribute greatly to the quality of welds produced. However, higher power machines may also come with increased complexity and price, requiring careful consideration.
Duty Cycle
The term "duty cycle" refers to the amount of time a welding machine can operate continuously before needing to cool down. It is generally expressed as a percentage. For example, a machine rated at 60% duty cycle can weld for six minutes out of ten before requiring rest. A high duty cycle means the machine can work longer without interruptions, making it beneficial for larger projects. A unique feature of duty cycles is that they can be misleading; a machine with a lower duty cycle could still suit your needs, depending on how you plan to use it.
Portability
Portability is another vital aspect of a welding machine, especially for home and garden use where moving between locations is often required. Many users prefer lightweight models that are easy to transport. Yet, this characteristic must be balanced with the stability and performance of the machine. Some portable machines may compromise on power or features to achieve a lightweight design. Therefore, it’s essential to find a unit that offers a suitable compromise between portability and functionality.
Control Settings
The control settings on a welding machine play a significant role in how effectively you can manage your welding tasks. Advanced machines may offer options for precise voltage controls and feeding speeds. These controls allow for a more tailored welding experience, helping to produce higher quality welds. A key characteristic of control settings is the simplicity of use. Beginners might benefit from machines that provide easy-to-navigate settings while experienced welders often seek more complex controls for advanced projects.
Budget Considerations
Budget is a critical aspect when selecting a welding machine. Setting a realistic budget helps narrow down your options without sacrificing essential features. Examine the total cost of ownership, which includes maintenance, accessories, and consumables. Higher initial costs can sometimes result in greater long-term efficiency and durability. Always compare multiple brands and models to assess their value proposition, ensuring you choose a machine that fits both your needs and budget without compromising on quality.
Top Brands and Models
Selecting a welding machine involves more than just understanding the types and features. Recognizing reputable brands can greatly influence your decision. Top brands often reflect quality, customer service, and reliability. These elements are crucial in achieving consistent results in home and garden projects. When you opt for a well-known brand, you often benefit from better warranties and customer support. Consumers tend to prefer proven brands with good reviews, as this can mitigate the risks of purchasing faulty equipment. This section will evaluate renowned brands and provide a comparative analysis of popular models, enabling you to make an informed decision.
Overview of Renowned Brands
Several brands stand out in the welding industry, known for their advanced technology and durable products. Hobart, Lincoln Electric, and Miller Electric are a few such names. Each brand has its own strengths.
- Hobart: Often recommended for beginners, Hobart welding machines are user-friendly. They offer a variety of models suitable for both MIG and stick welding, making them versatile for home projects.
- Lincoln Electric: This brand is known for its innovation. They provide professional-grade equipment with excellent performance ratings. Many users appreciate the longevity and productivity of Lincoln products.
- Miller Electric: Renowned for their industrial-grade machines, Miller focuses on high performance and advanced technology. Their equipment is often more expensive, but the investment can lead to superior results.
When choosing a brand, consider not only the machine's performance but also customer service and availability of replacement parts. It can be particularly beneficial in the long term to invest in brands known for quality.
Comparative Analysis of Popular Models
When evaluating specific models, it is essential to consider power output and key features that suit your needs. Here are a few notable models from the previously mentioned brands:
- Hobart Handler 140: This MIG welder is suitable for light to moderate projects. It operates on a 220V supply, delivering a decent performance for DIY enthusiasts.
- Lincoln Electric K2288-1: This MIG welder is another solid choice, offering a user-friendly interface and robust capabilities. It suits both beginners and experienced welders.
- Miller Multimatic 215: This machine stands out due to its versatility. It can handle MIG, TIG, and stick welding, making it ideal for varied home projects. It's also portable, enhancing usability.
"Investing in a reputable brand and model not only ensures quality but also enhances safety and efficiency in your work."
Selecting between these models involves understanding your specific needs and project requirements. Features to consider include portability, ease of use, and the types of welding processes each model supports. Assessing the benefits and limitations of each option can help you make a more educated choice.
Safety Measures in Welding
Welding is a process that, while rewarding for DIY enthusiasts and professionals alike, presents certain risks that require careful attention. The importance of safety measures in welding cannot be overstated. Injuries can occur if proper precautions are not taken. This section explores the vital safety elements that should be followed to ensure a safe welding environment. Implementing these measures not only protects the welder but can also prevent potential hazards to bystanders and property.
Protective Gear
Protective gear is an essential part of welding safety. Each component serves a unique purpose to shield the welder from various dangers associated with welding tasks. The following subsections discuss three key items: welding helmets, gloves, and clothing.
Welding Helmets
Welding helmets offer crucial protection against harmful light emitted during the welding process. The key feature of these helmets is the dark lens which protects the welder's eyes from intense brightness and ultraviolet radiation. A popular choice, auto-darkening helmets, allow for quick shifts between light and dark conditions, enhancing visibility prior to welding. This unique feature helps welders maintain focus while setting up their work, significantly lowering the risk of eye damage. However, one downside is that the auto-darkening function can occasionally malfunction, necessitating regular checks to ensure proper functionality.

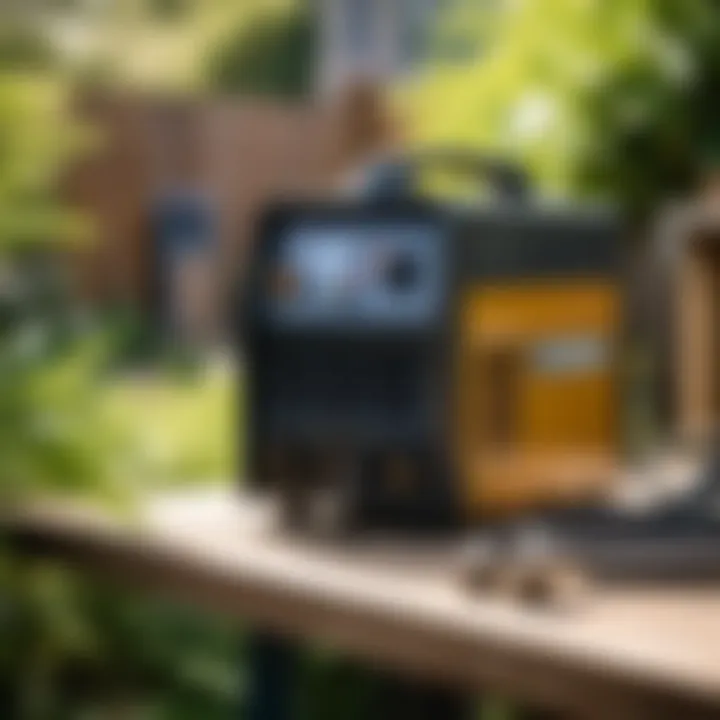
Gloves
Welding gloves serve to protect the hands from heat, sparks, and any potential cuts. The key characteristic of welding gloves is their heat resistance, generally achieved through materials such as leather. These gloves are particularly beneficial because they allow for dexterity while providing excellent protection. A unique feature is their reinforced seams, which enhance durability against wear during intense tasks. However, gloves can limit tactile sensitivity if too thick, so selecting the right thickness for the task at hand is crucial.
Clothing
Choosing the right clothing is also paramount for welding safety. Flame-resistant fabrics are a must, as they provide a barrier against sparks and heat. A key characteristic of welding clothing is its durability and ability to withstand extreme conditions. Long sleeves and long pants are recommended to cover exposed skin. The added benefit of wearing specialized welding jackets is they often come equipped with additional pockets for tools. Still, properly fitting clothing is essential; too loose can catch on equipment, while tight clothing may restrict movement.
Working Environment Safety
The working environment plays a vital role in welding safety. Ensuring adequate ventilation is one of the most important factors. Fumes from welding can be harmful, making it necessary to conduct operations in well-ventilated areas or use respirators if required. Furthermore, keeping the working area free of clutter reduces trip hazards, leading to a safer work process. Organizing tools and materials can also enhance efficiency during welding tasks.
Additionally, it’s necessary to ensure that fire safety measures are in place. This might include having a fire extinguisher readily accessible, especially when working with flammable materials nearby.
"Safety is not just a priority; it’s a commitment to protect yourself and those around you while welding."
By adhering to these safety measures, welders can create a secure environment that allows them to focus on their tasks without worrying about potential hazards.
Maintenance and Care of Welding Machines
Proper maintenance and care of welding machines are vital for ensuring their efficiency, safety, and longevity. A well-maintained machine consistently delivers optimal performance, which is especially crucial for home and garden projects where reliability is key. Neglecting maintenance can lead to reduced output quality, increased risk of accidents, and ultimately, higher costs due to repairs or replacements. Therefore, understanding how to maintain and care for your welding machine is essential for anyone engaging in DIY projects.
Regular Maintenance Practices
Regular maintenance adds substantial value to your welding machine. It can prevent minor problems from becoming major issues. Here are key points for effective maintenance:
- Clean the machine: Dust and debris can severely affect the performance. Regularly wipe down the outer casing and keep the ventilation areas clear.
- Inspect cables and connectors: Look for wear and tear that can lead to electrical failures or safety hazards. Damaged cables should be replaced promptly.
- Check gas levels: For MIG and TIG welders, ensure that the gas flow is adequate and that the connections are leak-free. This is essential for quality welds.
- Lubricate moving parts: Some machines have moving parts that may require lubrication to function smoothly. Always refer to the manufacturer’s instructions.
- Examine the welding nozzle and tips: These components can accumulate spatter and other debris, affecting the process. Cleaning or replacing them regularly helps maintain consistent performance.
Implementing these practices can result in improved efficiency and safer operation. Taking a little time for maintenance goes a long way in protecting your investment.
Troubleshooting Common Issues
Despite regular maintenance, issues may still arise with welding machines. Here are common problems and solutions to troubleshoot:
- Poor arc stability: This can be caused by incorrect settings, poor workpiece fit-up, or worn-out consumables. Check your settings and replace any worn items.
- Inconsistent welds: This often points to varying speed or feed rates. Ensure you are maintaining a steady pace and check the feed mechanism.
- Overheating: This can occur during prolonged use. Allow the machine to cool down on a regular basis and check the duty cycle.
- Excessive spatter: High spatter levels can result from incorrect voltage settings or using the wrong wire. Adjust the voltage or wire type to resolve this.
- Gas leaks: If you're using a shielding gas, detect leaks by using a soapy water solution. If bubbles appear, replace faulty fittings.
"Understanding how to troubleshoot common welding machine issues allows for swift resolution and less downtime on projects."
Effective troubleshooting is essential for maintaining functionality and ensuring safety. Following these guidelines can help you manage problems as they arise, ensuring that your home and garden projects proceed smoothly.
End
Selecting the right welding machine for home and garden use on a 220V supply is a significant decision. It impacts not only the efficiency of the projects you plan to undertake but also the quality of the results you can achieve. Various elements should be taken into consideration when making this choice. Understanding the types of welding processes available, for example, equips you to match your specific requirements with the appropriate machine.
Another vital aspect is the power output and duty cycle of the welding machine. These factors determine how much welding you can do within a given timeframe. Machines with higher power outputs generally permit deeper weld penetrations, suitable for more intensive tasks, while a good duty cycle helps maintain consistent performance without overheating.
Welding safety also cannot be overlooked. Proper gear and a safe workspace are non-negotiable factors that can greatly influence both the experience and effectiveness of welding projects. This article has emphasized the importance of embracing safety and maintenance practices, ensuring that your equipment lasts and remains reliable.
Lastly, the budget considerations serve as a key cornerstone of your decision-making process. It is crucial to identify what you can invest while seeking the best quality available within your price range. Affordable options may not always meet your needs, hence weighing pros and cons is necessary.
In summary, thorough research and consideration of each of these factors will lead to informed and effective selections that enhance your DIY welding endeavors.
Final Thoughts on Selection and Usage
Ultimately, the decision on which welding machine to use should come from a clear understanding of your objectives and capabilities. Your projects might vary in complexity, so being adaptable in your approach can lead to better outcomes. Take the time to evaluate the features that are most crucial for your operations, such as portability or ease of use. Remember that a suitable welding machine not only meets your requirements but also fits well within your operational framework.
In engaging with your welding tasks, constant learning and adaptation is vital. There will always be room for improvement in your techniques and approaches. Utilizing the resources around you and optimizing your equipment will yield substantial benefits.
"An informed choice is always the best choice."
The process does not end upon selecting your machine. Maintenance and understanding how to use it effectively will determine its longevity and your overall satisfaction with your projects. Therefore, invest wisely, prioritize quality, and approach each task with careful planning.
By focusing on these aspects, you pave the way for successful home and garden welding, enhancing your DIY skills and ultimately achieving outcomes you can be proud of.