Exploring M400 Cement: Properties and Applications
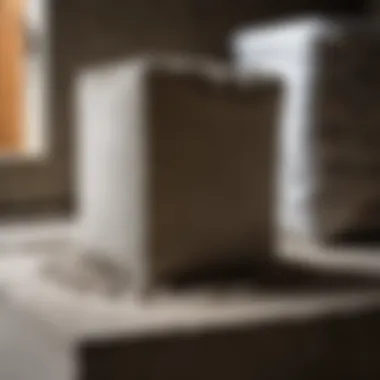
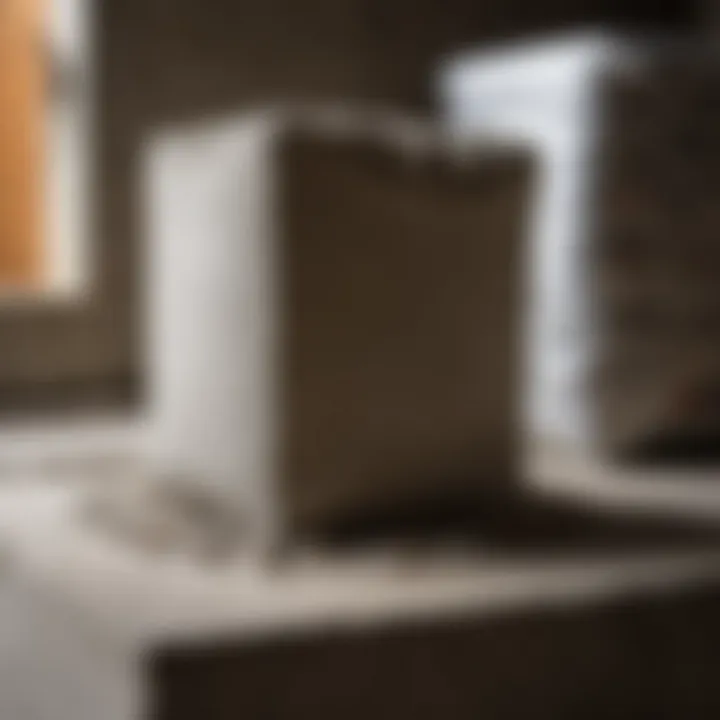
Intro
M400 cement is a specific type of cement known for its diverse properties and applications in modern construction. It is essential to understand the characteristics that set M400 apart from other cement grades. This article explores not only these properties but also the advantages of M400 cement in various construction projects. By focusing on its production processes and practical uses, we can gain valuable insights that will benefit both professionals and DIY enthusiasts.
In this article, we will cover significant areas related to M400 cement. This includes project planning, material selection, and the specific applications where M400 can be advantageous. Understanding these elements is crucial for achieving success in both large-scale construction and smaller DIY projects.
Проектирование и планирование
Before commencing any construction task, careful planning is vital. Whether one is a professional builder or a DIY enthusiast, a well-thought-out approach is necessary.
Как выбрать проект для DIY
Selecting the right project plays a crucial role in effectively utilizing M400 cement. It's essential to consider the project scale, objectives, and the capabilities of the involved materials. Some projects may benefit from the high strength provided by M400 cement, while others may require a different grade. Here are some factors to consider:
- Project Complexity: Choose projects that match your skill level and available time.
- Objective: Determine the primary goal of the project - whether it's structural integrity or aesthetic appeal.
- Material Compatibility: Ensure that other materials you plan to use align well with M400 cement.
Оценка времени и ресурсов
Assessing the time and resources required for a project helps create a feasible plan. M400 cement is known for its fast-setting nature, which can be advantageous when time is limited. Consider the following:
- Timeframe: Estimate how long the project will take, including preparation and curing times.
- Resource Availability: Ensure you have all necessary materials on hand, such as M400 cement, aggregates, and water.
- Labor Requirements: Factor in the number of people needed to assist in the project.
Выбор материалов
Choosing the right materials is crucial to the success of any construction project.
Типы материалов для различных проектов
While M400 cement is versatile, it is essential to understand what materials pair well with it. Commonly used materials include:
- Aggregates: Use fine and coarse aggregates designed for concrete mixes.
- Admixtures: Consider chemical admixtures that can enhance the performance of M400 cement. They can improve workability, reduce water demand, and speed up setting times.
Советы по покупке и экономии
When purchasing materials, including M400 cement, being economical can help manage project costs.
- Bulk Purchase: Buying in bulk often reduces the price per unit.
- Local Suppliers: Explore local suppliers to minimize transport costs.
- Quality over Quantity: Invest in high-quality materials to ensure a durable outcome, even if the upfront cost may be higher.
"Investing in quality materials ensures the longevity and integrity of projects."
By carefully considering project design and material selection, you can effectively harness the benefits of M400 cement for a variety of applications.
Preface to M400 Cement
M400 cement plays a vital role in the construction industry. Its unique characteristics make it a favored choice among builders and designers. In this section, we will explore the definition and composition of M400 cement, as well as its historical significance.
Definition and Composition
M400 cement is a type of Portland cement, primarily used for its high strength and durability. The designation "400" indicates its compressive strength measured in kilograms per square centimeter after 28 days of curing. The primary components of M400 cement usually include clinker, gypsum, and mineral additives.
- Clinker is the main ingredient, formed by heating limestone and clay together.
- Gypsum is added to control the setting time.
- Mineral additives, such as fly ash or slag, can enhance specific properties like workability and resistance to aggressive environments.
These components together ensure that M400 cement is suitable for various applications where structural integrity is paramount.
Historical Context
Understanding the historical context of M400 cement provides insights into its evolution and growing popularity. The use of cement dates back to ancient times, but modern cement types emerged during the 19th century. M400 cement itself developed as demands for stronger and more durable materials increased, especially in the post-war building boom.
In various countries, including Russia and some Eastern European nations, M400 became recognized due to its favorable properties for severe weather conditions. The transition from traditional materials to cement-based solutions illustrates the advancements in engineering and construction methods. This historical evolution underscores the ongoing relevance of M400 cement in meeting both old and new construction challenges.
Technical Properties of M400 Cement
Understanding the technical properties of M400 cement is crucial for anyone working in construction or related fields. The properties define its suitability for various applications, influencing both performance and longevity. Each property can affect choices during project planning and execution. Therefore, knowledge of these characteristics will help ensure successful outcomes in both residential and commercial projects.
Strength and Durability
M400 cement is known for its strength. Compressive strength refers to the ability of the concrete mix to withstand axial loads. It is measured in megapascals (MPa), and M400 typically attains a strength of 40 MPa. Such durability makes it ideal for heavy load-bearing structures, like bridges and tall buildings. The high strength also contributes to its long-lasting nature, meaning structures built with M400 can endure more wear and tear over time.
This capability reduces maintenance costs, a significant advantage for long-term projects. When durability is prioritized, M400 cement offers reliability, minimizing repairs or rebuilding. As a result, it is popular in areas subjected to harsh conditions, ensuring buildings maintain structural integrity.
Setting Time and Workability
The setting time of M400 cement is also an important factor. It defines how quickly the cement hardens and sets after mixing with water. This speed can vary based on temperature and mix design but typically falls between 30 to 45 minutes for initial setting. This relatively fast setting time is beneficial for projects requiring quick completion, minimizing delays.
Workability refers to how easily the cement mix can be handled, placed, and finished. M400 cement is designed for good flow and compaction, making it more user-friendly than some lower-grade options. Users can achieve complex shapes and finishes without compromising strength. Careful adjustments in water-cement ratios can enhance workability. Therefore, whether for intricate decorative elements or robust structural components, M400 cement is a fitting choice.
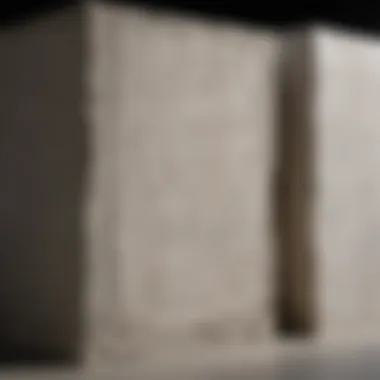
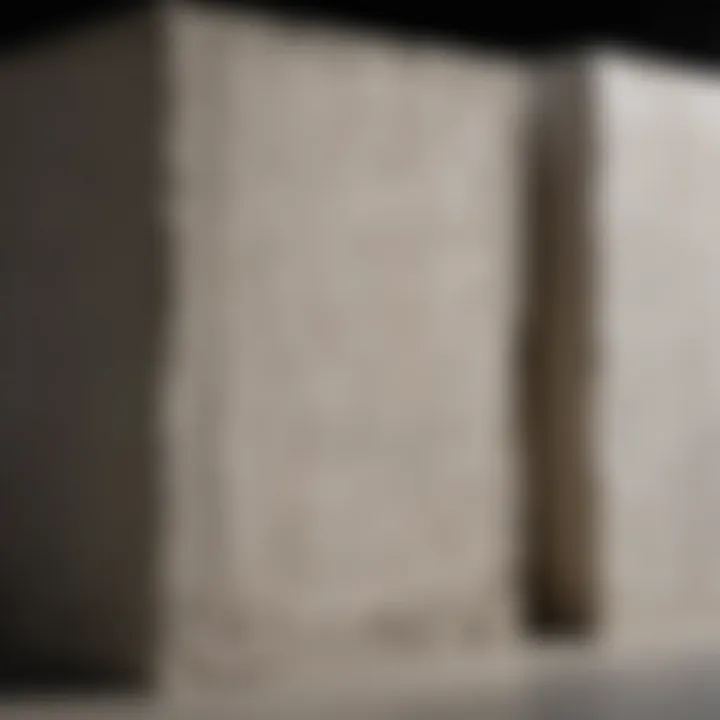
Chemical Resistance
M400 cement displays sturdy performance against various chemicals. Its resistance is essential for constructions exposed to aggressive environments, such as industrial sites or coastal regions. This property offers protection against acidic or alkaline substances. A structurally sound choice, this resistance reduces the chance of chemical degradation, which can be costly and time-consuming to fix later.
Additionally, additives can enhance chemical resistance further. When combining M400 cement with specific admixtures, users can improve its ability to withstand specific chemicals, tailoring the material to unique project requirements. Thus, for environments with potential risks, M400 cement provides confidence that the structure will hold long-term
In summary, the technical properties of M400 cement—its strength, durability, setting time, workability, and chemical resistance—make it a versatile choice for a range of construction projects. Understanding these factors is critical for any individual embarking on these endeavors.
Ultimately, a comprehensive grasp of M400 cement's technical properties allows designers and contractors to optimize their use, enhancing performance and ensuring project success.
Production and Quality Control
Understanding the production and quality control of M400 cement is essential for both manufacturers and construction professionals. These processes directly influence the performance, safety, and durability of the final product. A meticulous approach ensures that M400 cement meets the necessary standards required for various applications in the construction industry.
Raw Material Selection
The selection of raw materials lays the foundation for quality in M400 cement. Key components include clinker, gypsum, and supplementary cementitious materials. Clinker is produced by heating limestone and clay in a kiln, and its quality is paramount since it significantly impacts the cement's strength and durability. The right proportions of these raw materials must be maintained to achieve optimal results.
Using high-quality limestone can prevent impurities, leading to better overall performance. In addition, considering environmental factors during sourcing can also impact sustainability efforts. Local raw materials reduce transportation costs and support local economies.
Manufacturing Process
The manufacturing of M400 cement involves several steps, each critical to maintaining quality. After selecting raw materials, they undergo calcination in a rotary kiln, where they are heated to about 1450°C. This high temperature causes chemical reactions that produce clinker. Once cooled, the clinker is ground with gypsum to formulate the final product.
Control mechanisms during the production process are vital. Temperature, pressure, and grinding fineness must be monitored continuously. Any deviations can lead to poor quality cement. Employing advanced technologies such as sensors and automated systems can enhance the efficiency of this process, ensuring consistency across batches.
Quality Assurance Standards
Quality assurance standards for M400 cement involve rigorous testing protocols. Various properties, including compressive strength, setting time, and durability, must be tested to meet established norms. Regulatory bodies, such as ASTM or EN standards, outline the requirements needed for M400 cement in different environments.
Testing methodologies can include:
- Initial and final setting time measurement
- Compressive strength tests
- Chemical composition analysis
Regular audits and certifications are also necessary to guarantee compliance with industry standards. This structured approach to quality assurance not only safeguards consumer interests but also reinforces the credibility of manufacturers in the market.
"Quality control in cement production is not just a requirement; it is a commitment to excellence."
The attention to detail in production and quality control offers a competitive advantage in the industry, ensuring that M400 cement remains a reliable choice for construction professionals.
Applications of M400 Cement
M400 cement plays a significant role in the construction industry. It offers a diverse range of applications, which allow for enhanced durability and strength in various projects. Understanding these applications can help professionals choose the right material for their needs. The advantages of M400 cement span across different construction sectors, making it a valuable asset in both residential and commercial uses. Its versatility facilitates innovative designs, while its performance characteristics ensure quality results.
Residential Construction
In residential construction, M400 cement is frequently used for foundations, slabs, and masonry work. Its high strength enables it to withstand heavy loads, making it ideal for constructing sturdy walls and flooring.
- Foundation Work: M400 cement provides a solid base for homes, minimizing potential structural issues over time.
- Flooring: It is often chosen for floor slabs due to its ability to resist cracking, which enhances the longevity of the flooring.
- Masonry Applications: The cement’s strength aids in binding masonry units, ensuring durable and stable walls.
The fast setting time of M400 cement also benefits residential projects. It allows homeowners to complete tasks quicker, reducing downtime and project costs.
Commercial and Industrial Use
M400 cement is not limited to residential construction; it is prevalent in commercial and industrial projects as well. Retail spaces, warehouses, and factories often require strong, reliable materials that can handle high traffic and heavy machinery.
- Commercial Floors: Dual-purpose spaces like malls and shopping centers benefit from M400 cement's durability.
- Load-Bearing Structures: In industrial settings, the cement is essential for creating load-bearing walls and supportive beams.
- Cost-Effectiveness: Due to its strength and performance, M400 cement often reduces the need for additional reinforcements, offering a cost-effective solution for builders.
The adaptability of M400 cement makes it suitable for various types of commercial constructions, ensuring high performance under diverse operational conditions.
Infrastructure Projects
Infrastructure projects require materials that can endure harsh conditions and long-term usage. M400 cement is commonly employed in the construction of roads, bridges, and tunnels. Its unique properties enhance the longevity and safety of these vital structures.
- Road Construction: M400 cement contributes to the creation of durable roadways that can handle the wear and tear caused by vehicular traffic.
- Bridges: The cement's high compressive strength is crucial for bridge construction, enabling structures to support significant loads over extended periods.
- Tunnels: Its chemical resistance properties make M400 cement suitable for tunnels, as it can withstand exposure to moisture and various chemical elements.
M400 cement's ability to perform effectively in demanding applications is critical for maintaining the quality and integrity of infrastructure projects.
M400 cement not only ensures durability but also contributes to the efficiency of construction timelines across various sectors.
As professionals consider M400 cement for their projects, recognizing its diverse applications can guide them towards making informed decisions.
Advantages of Using M400 Cement
The advantages of using M400 cement are pivotal for professionals in construction. Understanding these benefits can lead to informed choices that enhance project quality and efficiency. Each feature provides distinct values, making M400 cement a preferable option in various applications.
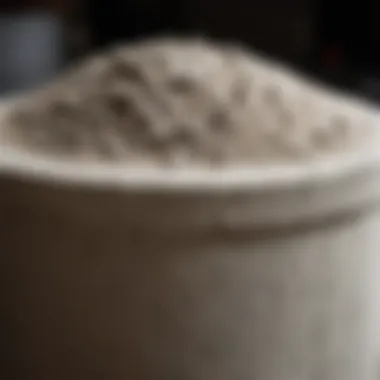
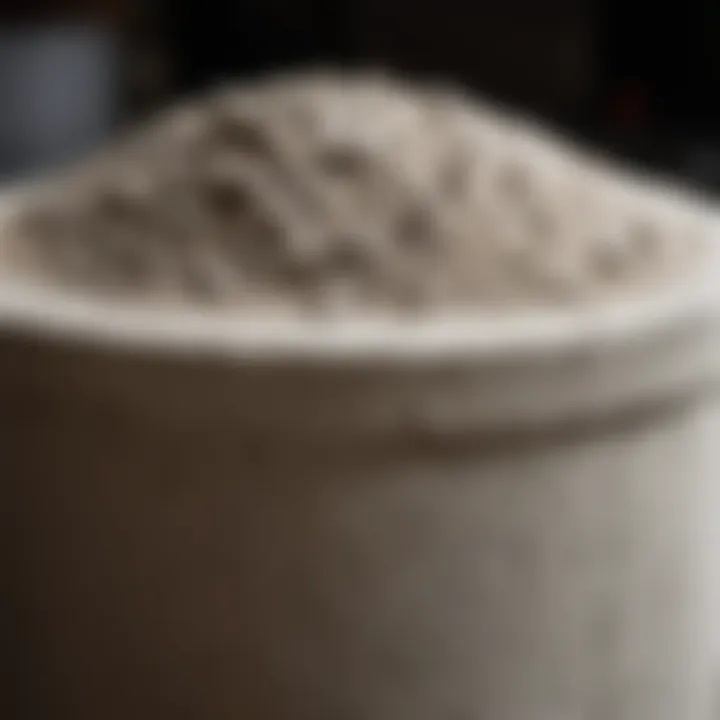
Fast Setting Time
One of the most important qualities of M400 cement is its fast setting time. This property allows construction to progress rapidly. In projects where time is crucial, such as commercial builds, the reduced curing time minimizes the interruptions.
In different environmental conditions, this rapid setting can lead to earlier project completion. For example, adverse weather can halt work. M400 cement's quick curing means time frames can be maintained more effectively. The speed does not compromise the quality, as it still meets required structural standards.
Cost-Effectiveness
Cost is a decisive factor in any construction project. M400 cement is often seen as cost-effective compared to other grades. Its ability to set quickly leads to decreased labor costs. Fewer man-hours mean significant savings. Furthermore, its durability ensures fewer repairs or replacements in the long term. This economic advantage is attractive to various stakeholders, especially for budget-sensitive projects.
Also, using this cement can reduce material wastage. When mix ratios are well calculated, M400 cement can be used efficiently. Thus, this leads to lower costs on materials and storage. Overall, it proves to be a financially savvy choice.
Versatility in Mixing
M400 cement is versatile when mixed with other aggregates and materials. This property enables it to be used in a wide range of construction methods and applications. Whether creating concrete blends for foundations, pavements, or decorative elements, M400 cement adapts well.
This versatility allows builders to customize mixtures based on specific project demands. For instance, incorporating various additives can enhance properties like water resistance or workability. Additionally, mixing with other cements can lead to improved performance characteristics.
"The adaptability of M400 cement makes it suitable for numerous construction scenarios where unique challenges arise."
Overall, the advantages of using M400 cement contribute significantly to its appeal in the industry. Time savings, cost-effectiveness, and versatility make it a leading choice for many construction professionals.
M400 Cement vs Other Grades
Understanding the differences between M400 cement and other cement grades is essential for making informed decisions in construction and DIY projects. This section will discuss comparative strengths and performance in adverse conditions. Comparing M400 with other grades helps illuminate its unique benefits and specific applications.
Comparative Strengths
M400 cement is known for its high compressive strength, which typically surpasses that of lower-grade cements, such as M200 and M300. This increased strength is attributed to the specific formulation and manufacturing processes involved in its production. The higher strength allows for the construction of structures that can bear more load, making it ideal for heavy-duty applications such as bridges and high-rise buildings.
Also, the ability of M400 cement to achieve strength quickly enhances its utility in projects that demand rapid completion. In practice, this means less waiting time for formwork removal, which also leads to faster project turnover. Its performance can be particularly beneficial for commercial and infrastructural projects requiring rigorous compliance with safety standards.
When comparing with higher grades like M500 or M600, M400 still provides an excellent balance between strength and affordability. It serves as a reliable option for projects that require strength without the extreme costs associated with the highest grades.
Performance in Harsh Conditions
One of the standout characteristics of M400 cement is its performance under harsh environmental conditions. It demonstrates exceptional resistance to both moisture and extreme temperatures. This feature makes it suitable for regions prone to heavy rainfall or fluctuating climates.
M400 cement's composition aids in preventing premature deterioration. This means structures made from M400 can endure water exposure without significant weakening, making it a popular choice for construction near bodies of water or in areas prone to flooding.
In addition, regarding chemical resistance, M400 cement can withstand various aggressive substances often found in industrial settings or coastal areas. This durability ensures long-lasting structural integrity and can minimize maintenance costs over time.
"Selecting the right cement grade is crucial for achieving the desired performance and longevity of structures. M400 provides an ideal mix of strength and resilience that sets it apart from other grades."
In summary, M400 cement’s strengths relative to other grades emphasize its value proposition for both versatile residential projects and demanding commercial applications. Considering these factors is vital in optimizing construction practices for cost-effectiveness and performance.
Safety Considerations
Ensuring safety when using M400 cement is crucial, both for health and the integrity of construction projects. Proper handling and storage can mitigate risks associated with cement dust, chemical exposure, and accidents during application. It also fosters a safer working environment, ultimately contributing to the successful execution of projects.
Handling and Storage Guidelines
Handling M400 cement requires careful attention to prevent dust inhalation and skin irritation. It is advisable to store the cement bags in a dry area, protected from moisture and direct sunlight. Sealing the bags tightly after opening can help maintain their quality.
The following guidelines should be followed:
- Keep Away from Moisture: M400 cement should be stored in a cool, dry place to prevent clumping and a reduction in effectiveness.
- Stacking: Store bags on wooden pallets to prevent direct contact with the floor. This avoids moisture absorption from the ground.
- Proper Labeling: Keep all storage containers labeled to avoid confusion during mixing and application.
- Avoiding Mixing with Contaminants: Ensure that cement does not come into contact with substances that can alter its chemical properties, such as oil or other chemicals.
Personal Protective Equipment
Wearing the right personal protective equipment (PPE) is critical when handling M400 cement. This equipment minimizes health risks associated with dust and chemical exposure.
Essential PPE includes:
- Respirators or Dust Masks: To prevent inhalation of cement particles.
- Eye Protection: Safety goggles protect against dust and splashes.
- Gloves: Wearing gloves reduces the risk of skin contact, which can cause irritation or allergic reactions.
- Long Sleeves and Protective Clothing: This prevents skin injuries while handling cement.
Using PPE correctly not only safeguards individuals but also enhances productivity by reducing the likelihood of work interruptions due to injuries or health issues.
"Safety is not just a priority; it is a prerequisite for successful outcomes in construction projects."
Sustainability in Cement Production
Sustainability in cement production is not just a trend; it is a necessity. The construction industry significantly contributes to global carbon emissions. Therefore, adopting sustainable practices in cement production is vital for reducing the industry's environmental footprint. M400 cement, when viewed through the lens of sustainability, showcases several key elements that both manufacturers and users should consider. These elements include the reduction of greenhouse gas emissions, the efficient use of raw materials, and the implementation of innovative processes that minimize waste.
Key benefits of sustainable cement production include:
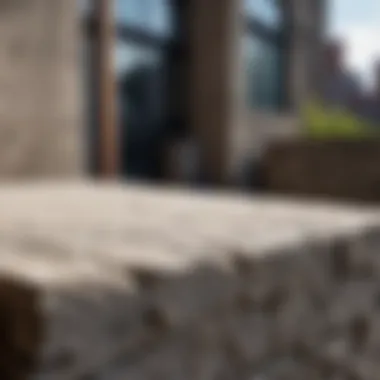
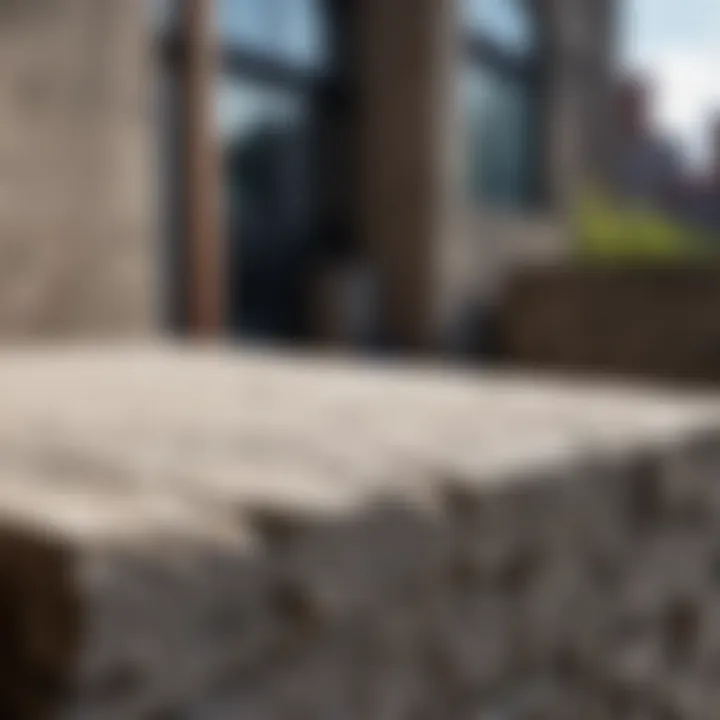
- Lowering carbon emissions: The cement industry is a major emitter of CO2. M400 cement producers are implementing technologies that can reduce these emissions, making the material more eco-friendly.
- Resource efficiency: By optimizing the use of raw materials, producers can offer M400 cement made from a smaller quantity of high-quality ingredients. This not only cuts costs but also conserves natural resources.
- Lifecycle assessment: Understanding the entire lifecycle of M400 cement ensures that its impact on the environment is continually assessed and improved upon.
Each of these points shows the commitment to sustainability and how it intertwines with the production of M400 cement, aiming towards a greener future in construction.
Environmental Impact
The environmental impact of M400 cement is an essential consideration for stakeholders. The manufacturing of traditional cement involves burning substantial amounts of fossil fuels, leading to high CO2 emissions. However, manufacturers of M400 cement are now adopting alternative fuels and innovative production methods to mitigate this impact. Using waste materials as substitutes for traditional fuels or raw materials can substantially reduce emissions during production.
Moreover, the efficient production of M400 cement requires less energy compared to other grades.
Some critical factors affecting the environmental impact include:
- Carbon capture technologies: Such technologies can capture CO2 emissions at the source, preventing them from entering the atmosphere.
- Use of supplementary cementitious materials: This includes materials like fly ash and slag, which can partially replace the clinker in cement, leading to reduced emissions.
- Enhanced durability and longevity of structures: M400 cement's unique properties contribute to longer-lasting structures, thereby minimizing the need for repairs and replacements which can have environmental impacts.
"Sustainable cement production considers both the economic and environmental aspects, striving for a balance between the two."
Innovation in Materials
Innovation in materials plays a crucial role in enhancing sustainability in cement production. Advancements in technology allow for the development of new composite materials that can replace or augment traditional cement. For M400 cement, this translates into better performance and reduced environmental impact.
Some innovations include:
- Geopolymer cements: These alternative cements can be created using industrial by-products and emit significantly less CO2, making M400 more sustainable.
- Nano-materials: Addition of nano-materials may enhance the strength and durability of M400 cement. This means less cement is required for construction projects, decreasing the overall consumption.
- Smart additives: These can improve properties such as workability and setting time, which increases the efficiency of construction processes using M400 cement.
The embrace of these innovations not only improves the characteristics of M400 cement but also aligns the production processes with modern sustainable goals, thus fostering a new era in the construction industry.
Practical Guide to Using M400 Cement in DIY Projects
Using M400 cement in DIY projects is both beneficial and practical. It brings durability and strength to various constructions, making it an excellent choice for home improvement enthusiasts. Understanding how to effectively use M400 cement can enhance the quality of work done, whether for repairs, building new structures, or decorative applications. This section provides essential guidance tailored to those who wish to undertake their own projects, addressing tools, mixing, and finishing techniques.
Essential Tools and Equipment
Before starting any project with M400 cement, it's crucial to gather the necessary tools and equipment. Here are some essential items you will need:
- Cement mixer: A mechanical mixer allows for consistent mixing throughout the batch.
- Shovels: Useful for transferring materials and mixing by hand if needed.
- Measuring buckets: For accurate measurements of cement and water.
- Trowels: Various trowel shapes allow for different finishing techniques on the cement surface.
- Safety gear: This includes gloves, goggles, and masks to protect against dust and exposure.
Investing in quality tools not only ensures a smoother workflow but also increases safety and precision throughout the project.
Step-by-Step Mixing Instructions
Mixing M400 cement requires careful attention to detail. Follow these steps closely to achieve the best results:
- Measure the materials: Use measuring buckets to ensure the right proportions of cement, sand, and aggregate (if required). A common ratio is 1 part cement to 2 parts sand, and 3 parts aggregate.
- Add water: Gradually add water to the dry mix. The amount of water affects the consistency; usually, a water-to-cement weight ratio of about 0.4 to 0.5 is ideal.
- Mix thoroughly: Use the cement mixer to blend the materials until the mixture achieves a uniform consistency. It should be workable but not too wet.
- Check the consistency: A test can be done by trying to form a ball with the mix. It should hold shape without crumbling or being overly soggy.
Following these steps ensures a well-prepared mixture suitable for various applications.
Finishing Techniques
Finishing your M400 cement project properly is essential for aesthetics and longevity. Here are notable techniques:
- Screeding: After pouring, use a straight edge to level the surface. This helps in achieving a flat finish.
- Troweling: Once the initial set occurs, trowel the surface until smooth. This can be done in stages based on how quickly the mixture sets.
- Grooving: For larger areas, consider grooving, which helps control cracking by allowing movement in the set cement.
- Sealing: Apply a concrete sealant after full curing to protect against moisture and stain penetration.
Proper finishing techniques not only enhance visual quality but can also extend the lifespan of the cement applications.
"The key to successful DIY projects with M400 cement lies in preparation, execution, and finishing. Attention to each step yields durable and visually appealing results."
By adhering to these guidelines, individuals engaging in DIY projects can navigate the practical aspects of using M400 cement, ensuring a gratifying construction experience.
Case Studies: Successful Uses of M400 Cement
The exploration of case studies involving M400 cement offers significant insights into its practical applications and effectiveness in various construction scenarios. It showcases real-world instances where this type of cement has been pivotal in achieving project goals. By analyzing these examples, we can better understand the cement's properties and its adaptability in different contexts. Thus, this section serves as an essential component of the overall discussion about M400 cement, highlighting its reliability and versatility in both residential and commercial projects.
Residential Projects
In residential construction, M400 cement is often chosen for its superior strength and durability. Homeowners and builders appreciate how it performs under different environmental conditions.
For instance, in many local housing developments, contractors have effectively used M400 cement for foundations and structural elements like beams and columns. The compressive strength of M400 ensures that the structures withstand loads over time. Projects in areas prone to earthquakes have also seen the benefits. M400 cement's performance in seismic resilience is particularly noteworthy, as it helps in maintaining structural integrity during such events.
Additionally, M400 is user-friendly for DIY projects. One case involved a homeowner who decided to build a personal workshop in their backyard. They utilized M400 cement to set the foundation, as the cement's fast-setting time allowed for a quicker project completion. This flexibility illustrates its suitability not only for professionals but also for individual users undertaking home improvement tasks.
"Using M400 cement made my project not only easier but more durable, too. I won't choose anything else for my next DIY endeavor!"
Commercial Projects
In the commercial sector, M400 cement plays a crucial role in various applications, from office buildings to large retail spaces. Its adaptability and strength have made it a popular choice for contractors.
A notable example includes the construction of a mid-rise office building where M400 cement was chosen for the load-bearing walls. Its high strength ensures that the walls provided necessary support for multiple floors without compromising safety. Moreover, the chemical resistance of M400 cement is a significant advantage in commercial environments that might encounter harsh cleaning agents or the potential for spills.
Another commercial project involved a shopping center where both aesthetics and durability were critical. The builders opted for M400 cement in decorative concrete features. The ability to set quickly allowed for a faster approach to finishing stages without sacrificing quality. This versatility made it possible to complete the design elements on schedule.
In summary, M400 cement's role in both residential and commercial projects highlights its capacity to meet diverse construction needs. The real-world applications elucidate the advantages and strengths of M400 cement, making it a reliable material choice in modern construction.