Understanding Pump Station Malfunctions: Key Factors
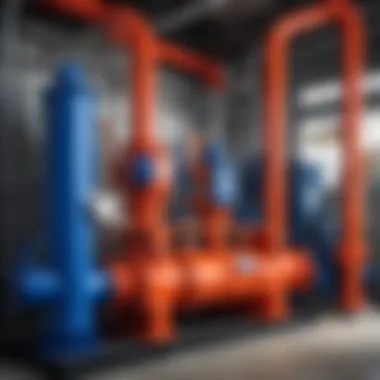
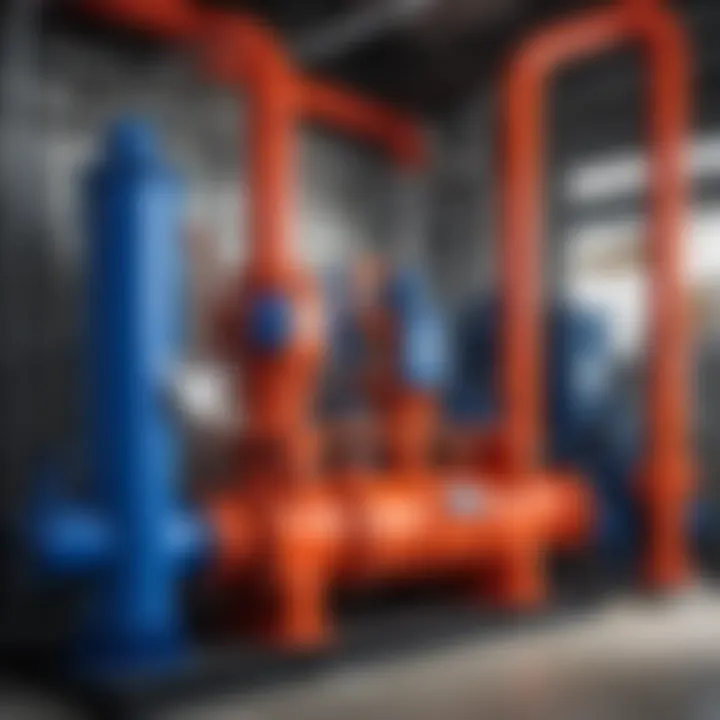
Intro
Pump stations play a crucial role in water management and distribution systems. However, they are not immune to malfunctions that can disrupt operations. Understanding the underlying factors that can lead to such issues is essential for both professionals and DIY enthusiasts.
This article will delve into various reasons why a pump station might fail to turn off, including operational inefficiencies, technical failures, and maintenance issues. By examining these concerns, it aims to shed light on best practices for diagnosing and addressing problems that may arise in pump station operations.
Knowing how to identify these faults can help extend the lifespan of equipment and maintain efficiency, ensuring a reliable service.
Проектирование и планирование
Planning is a significant part of any project involving a pump station. It involves choosing the right design and understanding how much time and resources will be needed.
Как выбрать проект для DIY
When selecting a project for a DIY pump station installation or repair, consider the following:
- System Requirements: Determine the flow rate and pressure needed for your specific application.
- Space Constraints: Ensure you have adequate space for the pump and any auxiliary equipment.
- Technical Expertise: Assess your knowledge and skills. If the project is too advanced, consider hiring a professional.
- Local Regulations: Familiarize yourself with local codes and standards that may impact the design.
Оценка времени и ресурсов
Evaluating the time and resources necessary is crucial for successful project completion. Take into account:
- Materials and Tools: Make a list of all required materials and tools.
- Team Size: Consider how many individuals will assist and their expertise levels.
- Time Frame: Create a realistic timeline for project phases.
By thoroughly planning and understanding the project scope, one can reduce the likelihood of malfunctions occurring later.
Выбор материалов
Material selection directly influences the performance and lifespan of a pump station. Choosing the right materials ensures efficient operation and minimizes the potential for breakdowns.
Типы материалов для различных проектов
Different projects may require various materials. Common materials include:
- PVC: Popular for its lightweight and corrosion resistance.
- Steel: Provides strength but may require coatings to prevent rust.
- Fiberglass: Great for harsh environments but can be more costly.
Советы по покупке и экономии
When purchasing materials, keep in mind these tips to save both cost and time:
- Bulk Purchasing: Buy in bulk to reduce per-unit costs.
- Local Suppliers: Consider local suppliers to save on transportation costs.
- Quality Over Price: Invest in quality materials as they will lead to lower maintenance costs in the long run.
Prologue to Pump Stations
Pump stations play a critical role in fluid management systems. They help transport liquids from one location to another, ensuring a smooth and efficient operation in a variety of applications. Understanding pump stations is important not only for those who design and install them but also for those who maintain and troubleshoot these systems. The purpose of this section is to frame the relevance of pump stations and their workings in the context of potential malfunctions.
Definition and Functionality
A pump station can be defined as a facility that includes pumps and equipment designed to transport fluids. Its primary function is to move water, sewage, or other liquids through pipelines effectively. The operation might include several components, such as intake structures, pump units, and control systems.
The pump unit itself is the heart of the station. It can come in different types, like submersible, centrifugal, or positive displacement pumps, serving various purposes. For instance, centrifugal pumps are often used for water transfer, while positive displacement pumps are more suitable for handling viscous liquids. Having a basic understanding of these functionalities aids in recognizing how a malfunction might arise.
Importance of Proper Operation
The proper operation of a pump station is vital for multiple reasons. First, it affects the efficiency of operations within a facility. A pump that is not functioning optimally can lead to increased energy consumption, thus raising operational costs. Moreover, inefficiencies can reduce the lifespan of the equipment, leading to costly repairs or replacements.
Secondly, proper operation is essential for safety. Many fluids handled in pump stations can be hazardous. A malfunction can lead to spills, which pose both environmental and regulatory risks. Continuous monitoring and maintaining peak performance can prevent these incidents.
Finally, understanding the fundamentals of pump station operations contributes to better troubleshooting. Knowing how elements like pressure sensors and control panels function allows technicians to diagnose issues with greater accuracy. This understanding is crucial not just for the professionals in charge of maintenance but also for anyone involved with fluid systems, including designers and contractors.
"Preventive maintenance is key to ensuring operational reliability in pump stations."
By grasping the basic principles, one can more easily delve into the complexities of pump station malfunctions discussed later in this article. This introductory section sets the stage to understand not just what pump stations are, but why their effective operation is non-negotiable. It is a foundational step in addressing the various issues that can lead to their malfunction.
Common Reasons for Continuous Operation
Understanding the common reasons for the continuous operation of pump stations is crucial. This knowledge not only aids in diagnosing issues but also helps in optimizing performance. Continuous operation can lead to energy wastage, increased wear on components, and potential equipment failure. Hence, identifying the underlying causes is essential for both cost efficiency and sustainability in pump station management.
Faulty Pressure Sensors
Faulty pressure sensors are one of the primary culprits behind continuous operation. These devices monitor the pressure levels within the system. When they fail to provide accurate readings, they can signal the pump to remain on, believing that pressure levels are not adequate. This malfunction can occur due to wear, debris accumulation, or electrical faults within the sensor. The result is an improperly functioning pump that operates beyond necessary limits, which can lead to overheating and other mechanical issues.
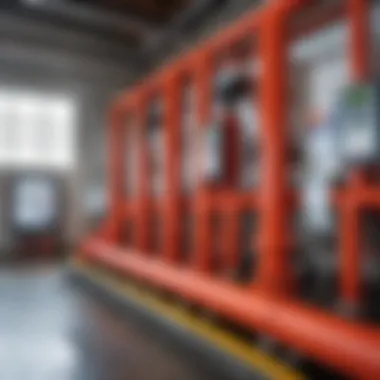
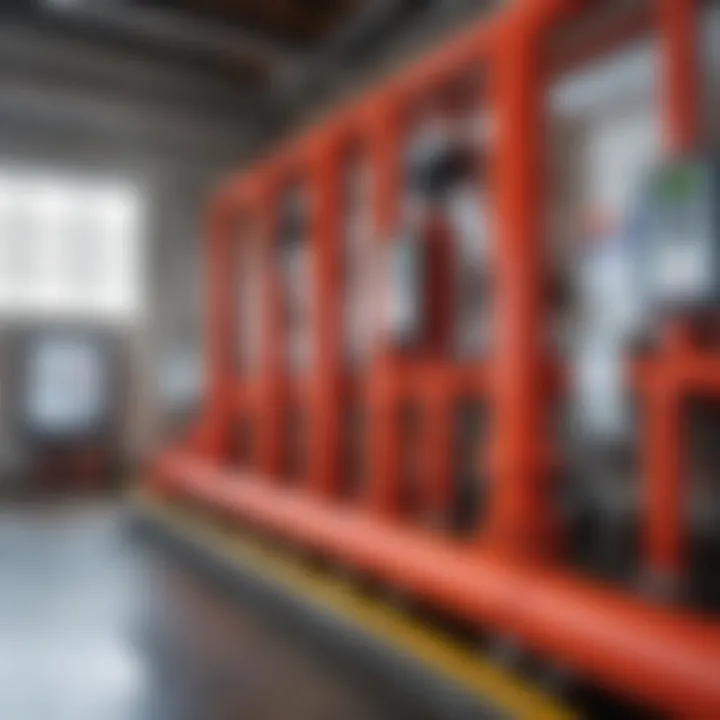
Electrical Failures
Electrical failures can severely impact the performance of a pump station. These failures may arise from issues such as short circuits, damaged wiring, or malfunctioning starters. When electrical components fail, they can create unintended feedback loops that keep the pump running continuously. As electrical systems age or are subjected to harsh environmental conditions, their reliability diminishes. Regular checks and maintenance of electrical systems are therefore critical to prevent unexpected downtimes and ensure reliable operation.
Clogged Filters
Clogged filters pose another significant challenge that can result in continuous operation. Filters are designed to remove particulates and contaminants from fluids. When they become obstructed, they can restrict flow, prompting the pump to work harder in an attempt to maintain pressure. This unnecessary strain can lead to prolonged operation cycles and potential damage to the pump itself. Implementing a regular filter maintenance schedule can mitigate these risks and promote efficient fluid movement.
Pump Overload Issues
Pump overload issues can occur when a pump is forced to operate beyond its designed capacity. This can stem from improper installation, changes in fluid dynamics, or mechanical failures upstream in the system. Overloading stresses the components, leading to excessive heat and increased wear. Monitoring the pump's performance parameters and ensuring compatibility with the system's demands is vital to avoid these problems. Identifying signs of overload early can save maintenance costs and extend the lifespan of the pump.
Operational Inefficiencies
Understanding operational inefficiencies in pump station management is critical for ensuring reliable performance and reducing malfunctions. Recognizing these inefficiencies allows operators and designers to identify root causes and implement strategies to enhance system functionality. When a pump station operates inefficiently, it can lead to excessive energy consumption, increased wear on components, and a greater likelihood of pump failures. Thus, addressing these inefficiencies is not just about improving performance; it also has significant long-term financial benefits.
Inadequate System Design
A pump station’s design can profoundly affect its effectiveness. Inadequate system design often leads to subpar performance that manifests as operational inefficiencies. The design must account for various factors, including hydraulic flow, pump selection, and system layout. If the layout fails to balance hydraulic requirements properly, it can create bottlenecks that impede flow. This inadequacy consumes more energy, as pumps must work harder to overcome the system's constraints.
Moreover, elements like pipeline material and diameter also play pivotal roles. If materials are incompatible with the pumped fluids or if the diameters are too small, significant pressure drops could occur along the system. Regular reviews of the system design help ensure compliance with evolving engineering standards and operational needs. Consideration of future expansions or adjustments during the initial design phase can lead to more sustainable operations.
Improper Pump Sizing
Another common factor leading to operational inefficiencies is improper pump sizing. Pumps must match the specific requirements of the system they serve. Undersized pumps can become overloaded, resulting in overheating and premature wear, making them susceptible to breakdowns. Conversely, oversized pumps can lead to excessive energy usage, inefficient operations, or even cavitation when flow rates are not adequately managed.
Choosing the proper pump involves understanding the system's minimum and maximum flow rates, head requirements, and the characteristics of the fluid being pumped. Miscalculations or assumptions made during the selection process can have lasting consequences on performance. A well-sized pump maximizes efficiency, reducing operating costs and extends the life of the equipment.
"Proper pump sizing directly correlates with long-term system performance and maintenance costs."
Recognizing and rectifying these operational inefficiencies is vital. By focusing on adequate system design and correct pump sizing, operators can enhance the reliability and longevity of pump stations. Ultimately, these efforts lead to improved performance and reduced maintenance burden.
Mechanical Malfunctions
Mechanical malfunctions are critical aspects when examining pump station failures. Recognizing mechanical issues is essential for maintaining consistent operational efficiency. These malfunctions can lead to prolonged downtime and costly repairs. Addressing them early can significantly enhance the longevity of pump systems and ensure optimal performance.
Worn-out Components
Worn-out components are among the most common causes of pump station failures. Over time, parts such as impellers, housing, and other internal mechanisms degrade due to constant usage and environmental conditions. This deterioration can diminish the effectiveness of the pump, causing inefficiencies in operation.
Signs of worn-out components include unusual noises during operation, vibrations, or changes in flow rates. Timely identification of these issues can prevent further damage. Replacing worn parts regularly helps maintain the system’s efficiency, ultimately facilitating better performance and reliability.
Bearing Failures
Bearings are crucial components that support pump shafts, allowing smooth rotation. When bearings fail, they can cause alignment problems and increased friction. This leads to overheating, which may cause severe damage to the motor and the entire system.
The primary indicators of bearing failure include excessive noise and heat. Regular maintenance and monitoring of bearing conditions are essential. Lubrication schedules should be adhered to, ensuring that bearings have the necessary protection against wear and tear. Investing in high-quality bearings can also enhance the overall performance of pump stations.
Seal Failures
Seal failures can lead to significant fluid leaks, affecting the operational integrity of the pump. Seals prevent contaminants from entering and fluids from escaping. When they fail, not only do they compromise the pump's efficiency, but they also pose potential hazards in the surrounding environment.
Common reasons for seal failure include improper installation, deterioration due to environmental factors, and pressure changes. Monitoring the condition of seals is vital. Frequent inspections and timely replacements will minimize the risk of seal failures, thus ensuring the pump operates effectively and without unexpected interruptions.
Key takeaway: Regular assessment and proactive maintenance of mechanical components are necessary to avoid unscheduled breakdowns and maintain high efficiency and reliability in pump stations.
In summary, understanding mechanical malfunctions and addressing worn-out components, bearing failures, and seal failures are paramount in safeguarding pump station longevity and functionality.
Electrical Problems
Electrical problems are a significant cause of pump station malfunctions. Understanding these issues is crucial for effective management of pump operations. When electrical systems fail, the entire functionality of a pump station may be compromised. Thus, addressing these problems can improve overall system reliability and efficiency.
Control Panel Issues
Control panels are the core of a pump station's electrical system. They manage various operations, including starting and stopping pumps, monitoring system performance, and regulating power supplies. If the control panel experiences malfunction, it can lead to severe operational disruptions.
Common issues include:
- Faulty Display Interfaces: Users may not receive accurate readings, which can lead to uninformed decisions.
- Ineffective Wiring: Poor connections can create short circuits or outages.
- Component Failures: Individual parts such as switches or relays may wear out over time.
Regular diagnostics of control panel functionality can prevent unforeseen complications. Addressing these issues proactively extends the lifespan of the control systems and reduces repair costs in the long run.
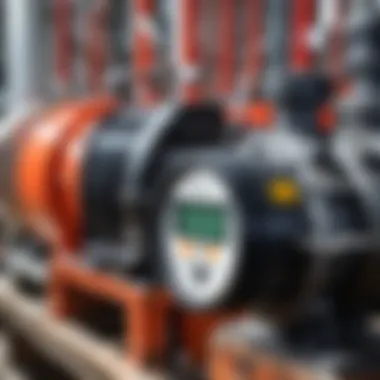
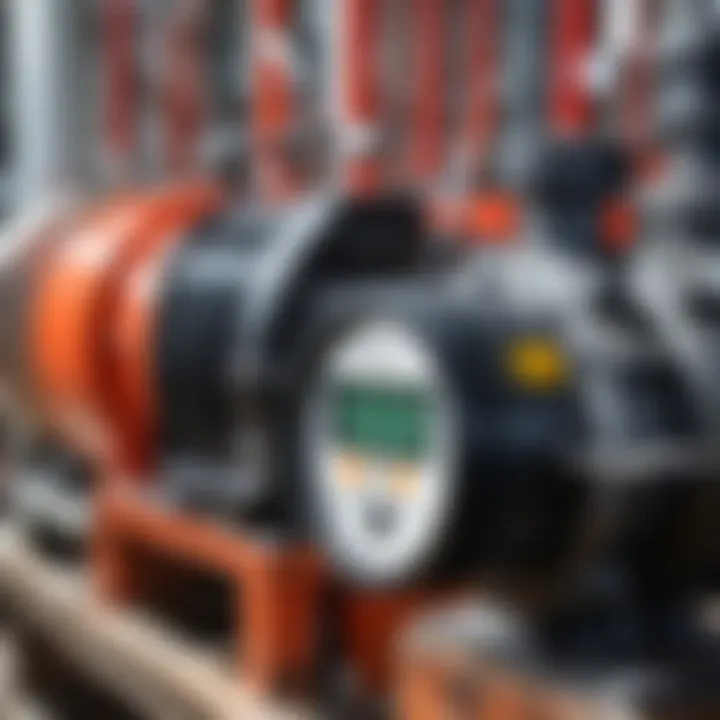
Voltage Fluctuations
Voltage fluctuations can cause significant chaos in a pump station. Uneven power supply can lead to inadequate performance or even equipment failure. High or low voltage can impact the operational efficiency of pumps. This is particularly concerning because pumps depend on consistent power to operate correctly.
Considerable effects of voltage fluctuations include:
- Overheating of Motors: Excessive voltage can lead to overheating, causing motor damage.
- Ineffective Pump Performance: Inconsistent voltage can lead to erratic pump behavior. This may include short cycling, which taxes machinery and increases wear.
- Damage to Controls and Sensors: Sensitive components may fail to operate with abnormal voltage levels, leading to further consequences.
Detecting voltage fluctuation issues requires regular monitoring. Tools like multimeters help in evaluating electrical stability and alerting operators to irregularities. Integrating voltage stabilizers might also be an effective preventive measure to ensure steady power supply to the pumps.
"Understanding electrical issues is fundamental in maintaining the longevity and reliability of pump stations."
By prioritizing the examination of electrical systems, operators can ensure better performance and lower risks associated with pump station malfunctions.
Diagnosing Pump Station Issues
Diagnosing pump station issues is a fundamental step in ensuring the reliability and efficiency of these systems. It involves assessing various operational factors and identifying potential problems before they escalate into more significant malfunctions. Effective diagnosis can save time, prevent costly repairs, and enhance the longevity of equipment. In the context of this article, a thorough understanding of this process leads to better maintenance strategies and heightened awareness of the operational capabilities of pump stations.
Visual Inspections
Visual inspections are critical in diagnosing pump station issues. They allow operators to quickly identify obvious physical signs of malfunction or wear. During a visual inspection, one should look for leaks around the pump, wear on components, and any signs of corrosion. Observing the condition of valves, piping, and filters is also essential.
It is recommended to perform these inspections regularly and at specific intervals, especially during routine maintenance checks. Documentation of findings can help track the condition of the equipment over time. Key elements to focus on during these inspections include:
- Leaks: Check for leaks around joints and seals.
- Corrosion: Look for rust or corrosion on metal parts.
- Physical Damage: Inspect for any cracks or physical damage on the pump body.
Addressing these issues promptly is key to maintaining functionality and effectiveness in operations.
Performance Monitoring
Performance monitoring involves analyzing operational metrics to assess the overall efficiency of the pump system. This can be done through various means, including gauging flow rates, pressure levels, and energy consumption. Data collected from monitoring can highlight irregular patterns that indicate underlying problems.
Regular performance evaluations assist in:
- Identifying Trends: Tracking performance metrics over time can reveal trends that may point to gradual deterioration.
- Detecting Anomalies: Sudden changes in performance may signal malfunctions that require immediate attention.
- Optimizing Operations: Understanding performance data helps in making informed decisions about necessary adjustments to improve efficiency.
Utilizing performance monitoring tools or software can significantly enhance the ability to detect these issues. Ensured continuity in monitoring establishes a proactive rather than reactive approach, significantly improving overall system reliability.
"Timely diagnosis can prevent small issues from becoming major failures, ensuring consistent operation and minimizing downtime."
Maintenance Practices
Maintenance practices are crucial for the longevity and reliability of pump stations. Regular upkeep not only prevents major failures but also ensures operational efficiency. Pump stations play a significant role in various systems, from water supply to wastewater treatment. Given their importance, having robust maintenance practices can safeguard against costly downtimes and extensive repairs.
Routine Checks
Routine checks are foundational to effective maintenance. These checks should encompass a variety of aspects, including:
- Visual Inspections: Regularly look for signs of wear, leaks, or corrosion. Observing changes early can mitigate larger issues later.
- Functional Testing: Ensure that all components, such as pressure sensors and control panels, are operational. Testing helps identify any anomalies in performance.
- Fluid Levels: Check oil and coolant levels in pumps. Low levels can lead to overheating and mechanical failures.
Routine checks should be scheduled at regular intervals, depending on the pump station's usage and environment. This can be weekly, monthly, or quarterly. Keeping a maintenance log will document the routine checks, helping in planning future maintenance needs and identifying recurring issues.
Scheduled Replacements
Planned replacements are vital to maintaining function and reliability. Components such as seals, bearings, and filters have defined lifespans, and replacing them on a schedule can prevent breakdowns. Key aspects include:
- Component Lifespan: Understanding the expected life of various components helps in setting a replacement schedule. For example, seals may need to be replaced every 1-3 years, while bearings can last longer depending on conditions.
- Manufacturer Recommendations: Always refer to the manufacturer's guidelines for specific timelines on replacements. Adhering to these recommendations ensures that parts work optimally.
- Training Personnel: Staff should be trained on the importance of these scheduled replacements. Awareness aids in emphasizing the value of preventive maintenance practices.
Scheduled replacements not only keep the pump station running smoothly but also can enhance the overall efficiency of the system by reducing the chances of unexpected failures.
"Preventive maintenance, including routine checks and scheduled replacements, is key to avoiding pump station malfunctions that can disrupt service continuity."
Troubleshooting Techniques
Troubleshooting techniques are vital in addressing pump station malfunctions. These methods allow operators to systematically identify issues contributing to the failure or inefficiency of the pumping system. A comprehensive approach minimizes downtime and enhances operational efficiency. When a pump station does not function correctly, quick diagnosis is essential to maintain service continuity.
Using effective troubleshooting techniques has several benefits. It not only saves time but can also reduce costs associated with excessive repairs or equipment replacements. The ability to recognize issues early can prevent minor problems from evolving into significant failures. Operators who are skilled in troubleshooting can conduct assessments rapidly and accurately, leading to informed decisions regarding repairs.
Considerations about troubleshooting techniques include understanding the typical issues that can arise, the appropriate tools to use, and maintaining a clear methodical approach. Knowledge of the system’s basic mechanics is equally important. Adopting a structured method or checklist can help streamline the troubleshooting process, making it easier for individuals involved in repairs or maintenance to follow through.
Step-by-Step Approach
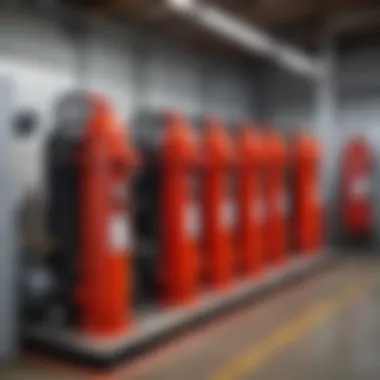
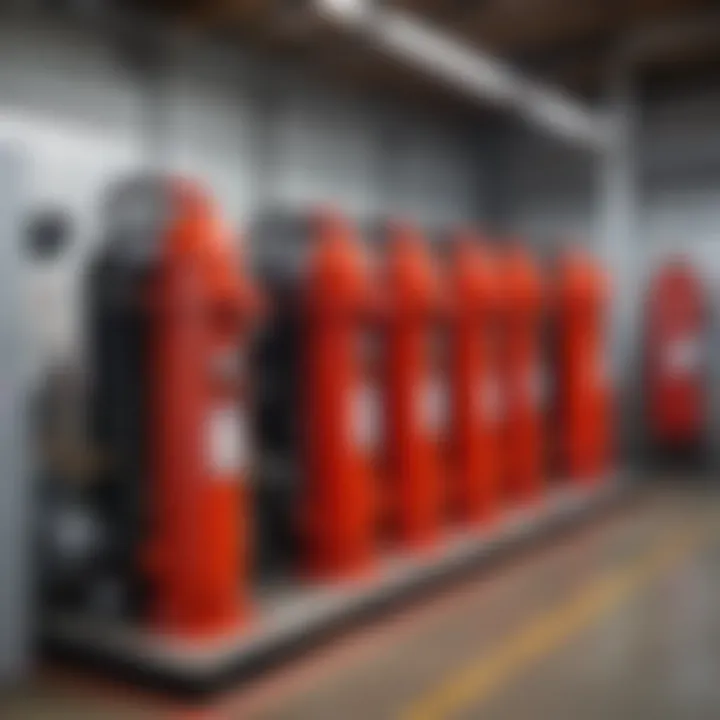
A step-by-step approach to troubleshooting helps in resolving issues efficiently. This method starts with an initial evaluation of the pump system and its operational parameters. Here are the steps involved in a structured troubleshooting process:
- Identify the Problem: Start by gathering information regarding the symptoms of the malfunction. This could include unusual noises, vibrations, or performance irregularities.
- Check for Alerts: Review any automation system for alarms or alerts that could indicate specific failures. Modern systems often provide alerts for critical failures.
- Conduct a Visual Inspection: Examine the pump station closely. Look for leaks, damages, or signs of wear and tear that may affect operations.
- Assess Performance Data: Analyze historical performance data and logs to identify patterns or fluctuations that may indicate ongoing issues. This insight helps to narrow down potential causes.
- Test Components: If safe to do so, conduct tests on various components. This can include checking electrical connections, testing sensors, or measuring pressure and flow.
- Eliminate Obvious Issues: Rule out common problems, such as clogs or electrical disconnections, before delving deeper into more complex solutions.
- Document Findings: Keep detailed records of the observations, tests, and outcomes. This information is useful for future reference and for maintenance planning.
- Implement Repairs: Once the issue is identified, proceed with the necessary repairs or replacements. Ensure that the standards and guidelines for safety are followed.
Using this structured approach can greatly ease the troubleshooting process. It keeps efforts organized and focused on solving the problem at hand.
"A systematic troubleshooting method not only enhances efficiency but also extends the life of pump station equipment."
Adopting such techniques promotes a disciplined approach to maintenance and repairs and can lead to significantly improved systems management and reliability over time.
When to Seek Professional Help
Determining when to seek professional help for pump station issues is essential for effective resolution. Many DIY enthusiasts may possess foundational knowledge about pump systems. However, certain complications can extend beyond their expertise. Recognizing these limits can save time and money while ensuring system safety and efficiency.
Identifying Complex Problems
Complex problems often arise from multiple factors. For example, if a pump station exhibits erratic behavior or inconsistent performance, it might indicate underlying electrical or mechanical failures. Insufficient knowledge about these complications can lead to incorrect assessments.
Moreover, identifying the source of a malfunction is not always straightforward. Sometimes, symptoms appear in symptoms distant from the actual problem. Taking heed of these complexities is essential. Attempting self-diagnosis can introduce unnecessary risks. In scenarios where diagnostic tools or extensive technical understanding are lacking, seeking professional help becomes crucial. Certified technicians can use specialized instruments and experience to identify issues accurately, preventing further damage to the system.
Cost-Benefit Analysis of DIY vs Professional Intervention
Considering the financial implications of repairs is essential. DIY repairs may seem cost-effective initially, but the hidden costs may quickly add up. Equipment can be misdiagnosed, and improperly executed repairs may lead to future complications. Sometimes fixing a small issue can inadvertently create larger problems.
On the other hand, professional services generally come at a higher initial cost. However, trained professionals can effectively address problems in one attempt. For complex issues, they can minimize downtime and ensure that repairs are done right.
A clear cost-benefit analysis can help in decision-making:
- DIY Advantages
- DIY Disadvantages
- Professional Advantages
- Professional Disadvantages
- Lower immediate costs
- Opportunity to learn and improve skills
- Potential for misguided repairs
- Longer repair times
- Risk of damage to equipment
- Expertise and experience in diagnosing issues
- Long-term savings from effective repairs
- Reduced risk of equipment failure
- Higher initial costs
- Dependence on external services
By weighing these aspects, one gets a clearer view of the best approach. Ultimately, making an informed choice about when to seek professional assistance is pivotal to achieving and maintaining functionality within pump stations.
Seeking help from professionals ensures that the root issues in pump stations are addressed effectively, thus safeguarding the investment made into the systems.
Preventive Measures
Preventive measures are crucial in maintaining the seamless operation of pump stations. By implementing proactive strategies, one can avoid common malfunctions that disrupt service and lead to costly repairs. These practices not only enhance the longevity of the equipment, but also optimize system efficiency and boost overall performance.
Improving System Efficiency
Improving system efficiency begins with understanding the components involved in a pump station. Each part, from the pump itself to the accompanying accessories, must function well in harmony. Regular maintenance checks can identify potential issues before they escalate into larger problems. It is vital to monitor system parameters such as flow rate, pressure, and energy consumption.
Optimizing system performance can often be achieved through:
- Routine calibration of pressure and flow sensors to ensure accurate readings.
- Regular cleaning of filters and strainers to prevent clogging, which can hinder efficiency.
- Upgrading control systems to state-of-the-art technology for more precise operation.
Implementing these measures ensures the pump operates at optimal conditions, leading to reduced wear and tear and thereby extending its life.
Training and Skill Development
Training and skill development for personnel working on pump stations cannot be understated. Knowledgeable operators are less likely to overlook crucial maintenance tasks or misdiagnose problems. Thus, investing in training can avert extensive downtime and expensive repairs.
Incorporating training programs that cover:
- Understanding pump technology and how various systems interact.
- Basic troubleshooting techniques, so operators can quickly respond to minor issues before they develop into significant faults.
- Safety protocols to promote workplace safety, ensuring staff is equipped to handle emergencies effectively.
Moreover, fostering a culture of continuous improvement among employees can yield significant benefits. Encouraging team members to stay updated on industry advancements and methodologies will enhance overall performance in the long run.
"Training is an investment in your workforce that pays dividends in operational excellence."
Ending
Concluding the discussion on pump stations, it is evident that a thorough understanding of malfunctions is crucial for both operation and maintenance. This article has highlighted several factors, including operational inefficiencies, mechanical failures, and electrical issues that can affect the performance of pump stations. Being aware of these elements helps in developing effective strategies to manage and remedy potential problems.
Recap of Key Points
In summary, the importance of regular maintenance cannot be overstated. Participants in this field should focus on:
- Monitoring system performance: Regular visual inspections and performance tracking can prevent minor issues from escalating into major failures.
- Proper training: Ensuring that all personnel are well-versed in both the functionality and the troubleshooting of pump stations enhances overall efficiency.
- Understanding complex issues: Recognizing when to seek professional insight helps avoid unnecessary costs and downtime.
Final Thoughts
Ultimately, the longevity and reliability of pump stations rely heavily on the proactive measures taken by operators and maintenance teams. Familiarity with the components and potential issues allows for swift action, ensuring that these systems function as intended. By integrating robust preventive measures, one can achieve a reliable service that can adapt to various operational demands. Continuous learning and adaptation will be key in managing this essential infrastructure effectively.